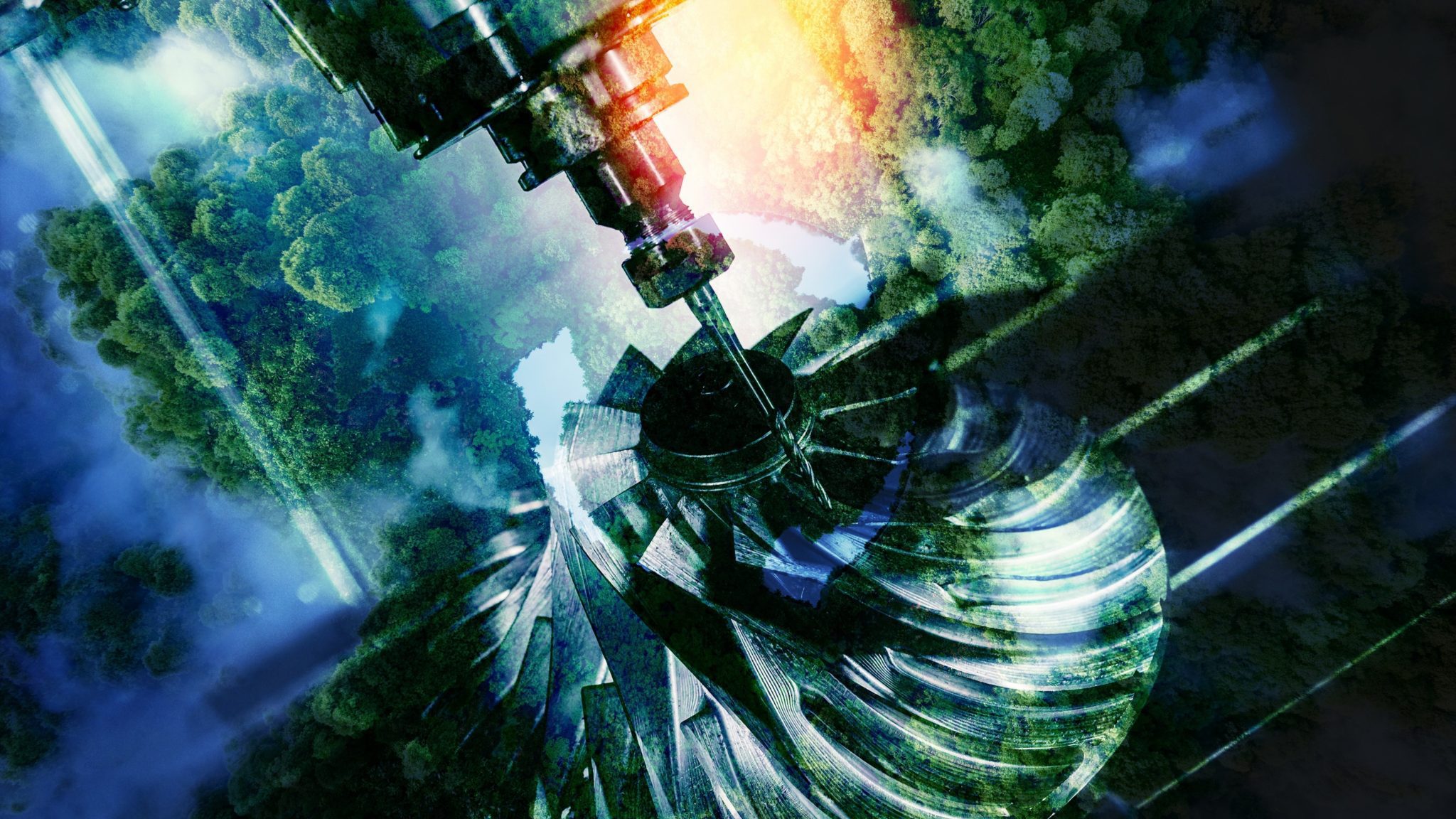
Sustainable Manufacturing
Automation Makes Manufacturing More Sustainable
Sustainability can be significant a source of competitive advantage and thus and important asset in today’s business environment. This page is about the sustainability impact of automation, including the carbon handprint of a flexible automation system. Look here for more information on Fastems’ sustainability strategy and carbon footprint. Automation can also help with sustainability reporting (CSRD). Sustainability means a balance of outcomes between people, planet and the economy. This model is also known as the ‘triple-p’ for planet, people and profits. Automation builds more sustainable manufacturing by four major ways, illustrated below:
- Reducing CO2 emissions (carbon handprint)
- Making manufacturing jobs more meaningful and safe
- Enabling compliance, traceability and transparent management
- Making manufacturing more competitive, nearer and just-in-time.
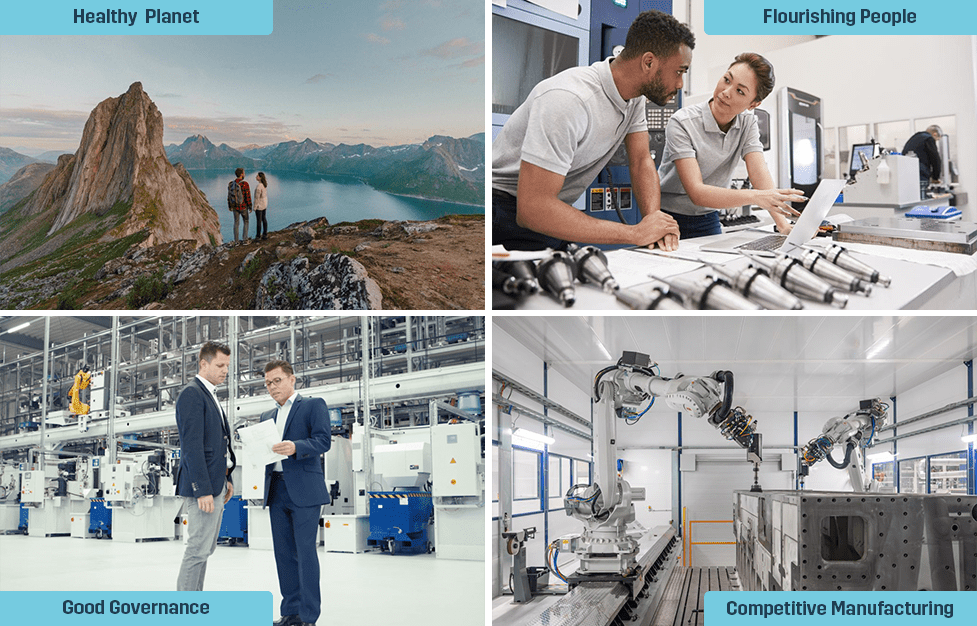
PLANET: How Automation Reduces CO2 Emissions?
CNC automation can significantly reduce emissions, building a positive carbon handprint of up to 868t of CO2e during it’s typical lifecycle. This is an outcome of improvements in efficiency, floorspace use and quality:
- Automation takes full use of machine tool capacity, reducing required machinery and the emissions around production capacity investments.
- Fewer machine tools need less space and automation systems store parts and raw materials vertically. In greenfield investment, this means saved building and heating costs, and in brownfield only the heating.
- Automation improves quality as it facilitates process standardization and removes potential for human error, meaning less scrapped material and energy.
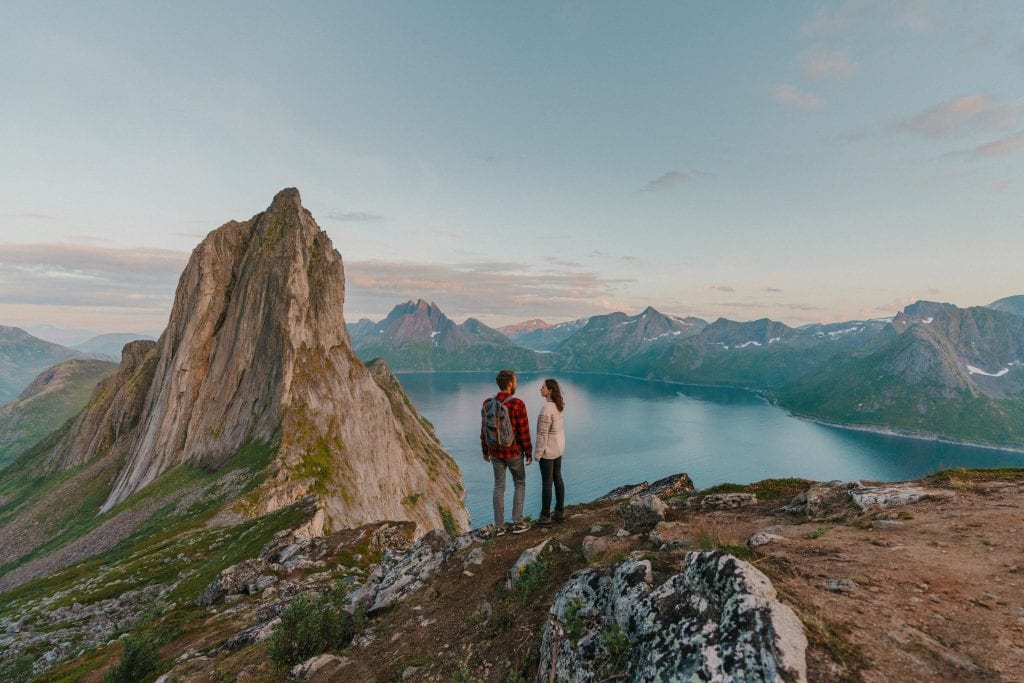
The carbon handprint of a flexible automation system
Carbon handprint means the reduction in emissions enabled by a product or a service. As automation multiplies the utilization rate of machine tools and stabilizes quality, it enables manufacturers to reduce the CO2 emissions related to their production development investments. This happens by reducing the amount of machine tools necessary to reach a certain production capacity. With a typical flexible manufacturing system (FMS) with two integrated machine tools running on utilization rates of 75 % each, the system can replace six stand-alone machine tools that typically won’t yield more than 25 % of utilization. As automation introduces process standardization is typical that scrap rates are significantly reduced. This could mean and increase of part yield from 97 % to 99 % as an example.
Fewer machine tools means less used floorspace, affecting building and heating cost. Furthermore, automation systems can store parts and raw materials vertically. Based on real-life customer examples and LCA (life cycle analysis) framework, Fastems has calculated that a flexible automation can reduce up to 868t of CO2 emissions during its lifecycle of 20 years, presuming system use in Germany. After this time, both automation and the machine tools would undergo large modernizations. Normal maintenance during their lifecycle is assumed to have a minor impact on emissions and thus excluded from the calculation.
Closely related to the carbon handprint, intelligent automation can support you with data and metrics needed in the sustainability (CSRD) reporting. One of the most important requirements for a manufacturer is to begin measuring and reporting the carbon footprint of their produced parts. MMS 8.2 measures and reports the machine tool energy consumption per each NC program, allowing the manufacturers calculate the energy usage in part level. The information can also be utilized to adjust the inefficient NC programs, or running certain parts overnight when the electricity demand is lower. For minimizing unnecessary energy usage, the new “Auto-Power On/Off” function of MMS 8.2 turns machine tool off automatically when there are no planned NC-programs to run. With the automatic wake-up function, the machine starts and warms up before by the next NC-program begin time. Read more about how automation can help with CSRD requirements!
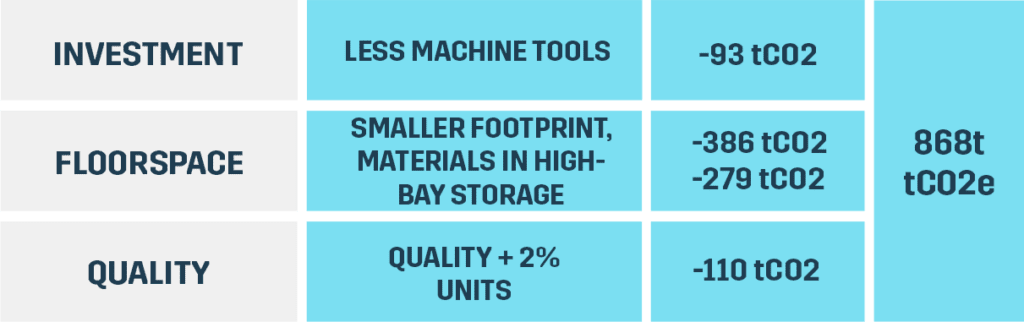
Did you know? The average non-automated CNC machine cuts chip 20-25 % or about 2000 hours per year. Here’s why!
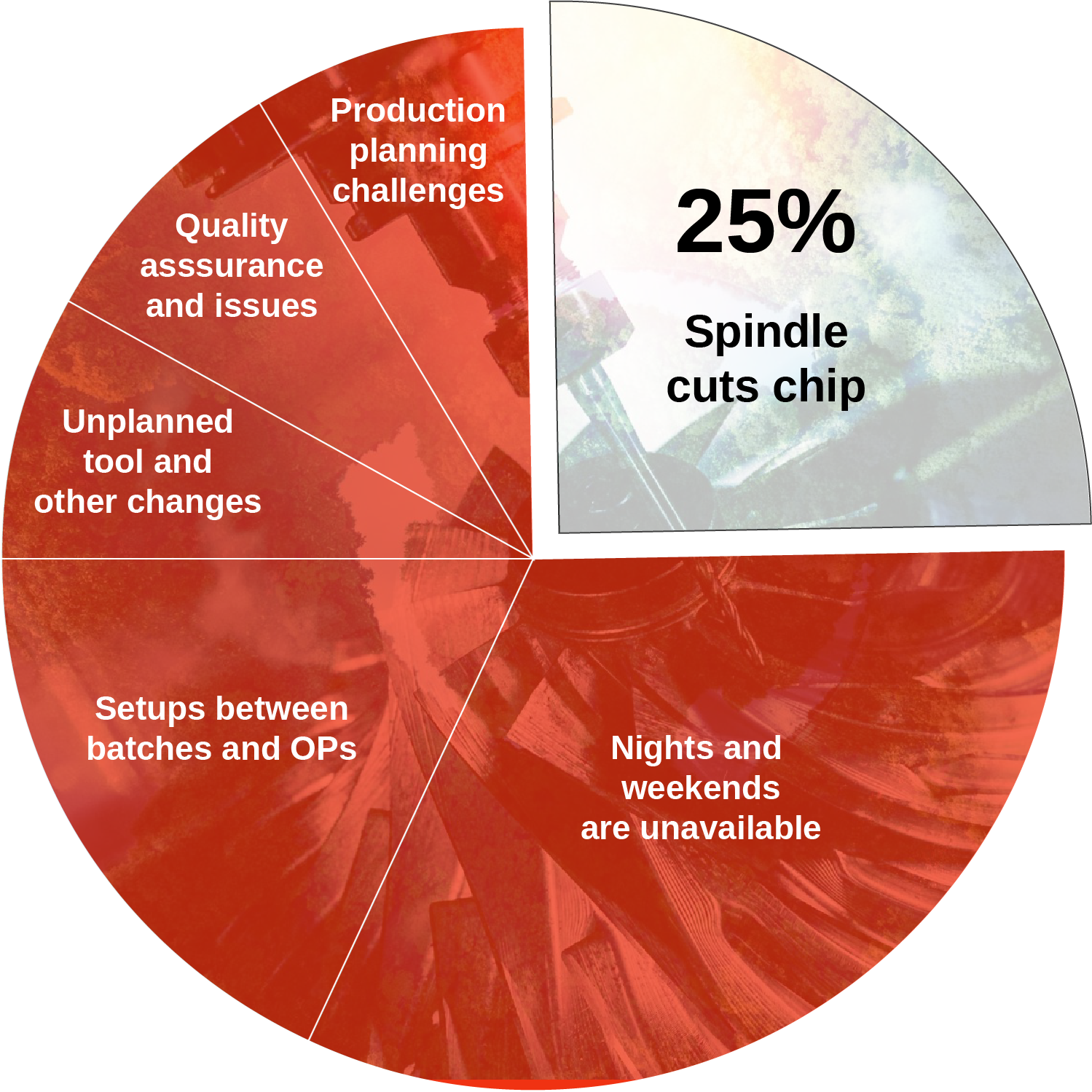
The situation is a result of losing most nights and weekends as it’s difficult to get people to work then. In machine shops, set-ups between batches and OPs are typically performed on machine tables, eating much of the available cutting hours. When including capacity wasted due to challenges in chaotic production planning, the impact of sudden changes, or missing resources, one arrives at the inevitable conclusion: high-mix manufacturing is by default quite inefficient – and consequently not very sustainable. According to our decades of experience, automation can triple the spindle utilization from about 2000 to around 6000 hours per year and beyond.
PEOPLE: How Automation Builds More Meaningful and Safe Manufacturing Jobs?
Most manufacturing businesses, especially in metalworking, are reporting workforce challenges around finding and keeping talent. Sometimes these challenges are even the bottlenecks limiting business growth. Here’s a summary on how automation can help. Look here for a longer version on how automation helps with workforce challenges.
Manufacturing jobs have been long considered ‘triple-d’ for dirty, dull and dangerous but that is about to change. Automation improves the physical and digital ergonomy of machinists as lifting positions get more comfortable and the user experience of automation is intuitive and empowering. With better production planning the daily shopfloor work becomes more organized and meaningful, reducing stress and boosting the feelings of outcome and teamwork.
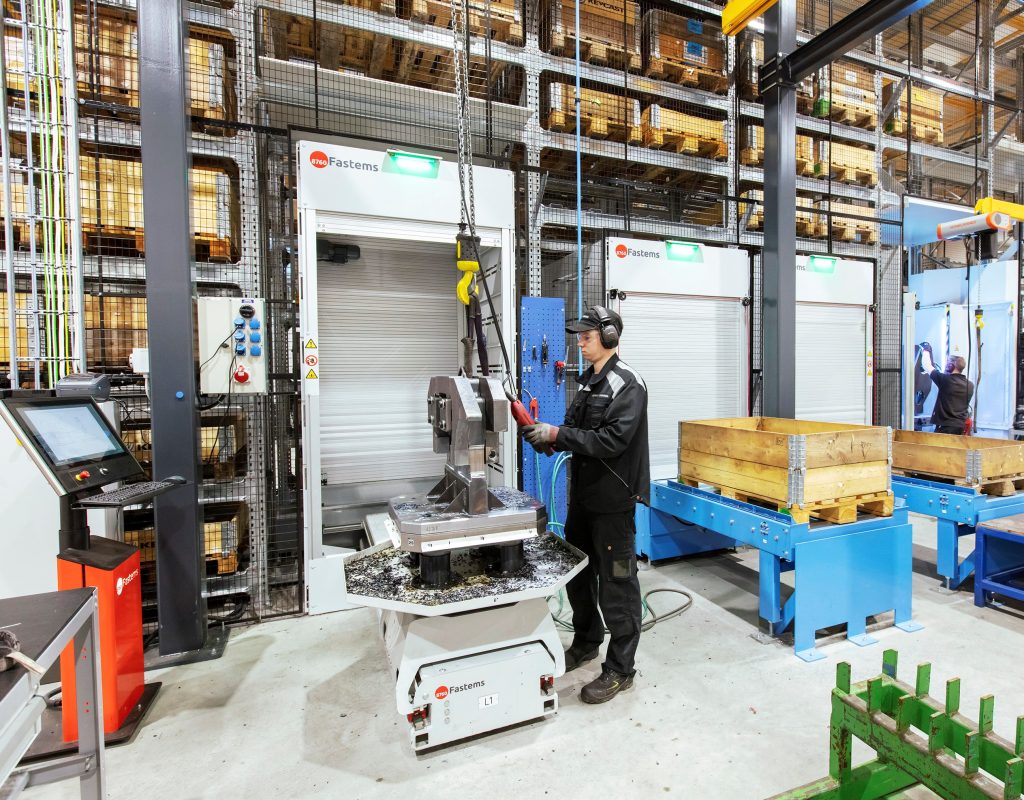
It’s a myth that automation should steal jobs in high-value-adding manufacturing like precision machining. Rather, automation enables you greater resilience facing the ever-changing market conditions, summarized well by one operations manager from a large German vice-manufacturer: “Automation secures jobs since we can now respond significantly better to order fluctuations“.
According to our experience manufacturers investing in automation produce a larger volume with the same staff or even recruit more people because the business needs it – and the bottom line allows it. Gilbert Products’ founder and president Silvain Gilbert concludes: “We basically doubled our production output with the same number of employees. That enabled us to expand our product line and to more than double our sales revenues in just a few years“.
GOVERNANCE: How Automation Helps Building Compliance, Traceability and Transparency?
In manufacturing, compliance can refer to reporting, providing traceability data, or following and tracking sustainability metrics like energy consumption. Sustainability is becoming increasingly important due to legislation such as CSRD in the EU and the drive for sustainability from the largest OEM manufacturers of the world. This means that manufacturers who can’t report on and prove the compliance of their production can lose business.
Intelligent automation control software like Fastems’ MMS can report on its energy consumption but also the energy (and material) consumed per NC-program or machine tool. This offers an opportunity to start improving energy efficiency. Automation can also do more by shutting down and waking up machine tools vs production needs, decreasing electricity use. Read more about MMS’ energy-saving features and CSRD compliance.
Having an accurate picture of your production is the first step in improving it and staying in control. Creating management models based on data-driven decision-making rather than opinions can increase organizational buy-in and commitment. Transparency also offers a way for misconduct to surface, supporting healthier business and just governance.
Automation supports and enables process standardization which is at the heart of high and constant quality. This way, automation can also support manufacturers in their visions for building certified quality systems, for example according to the ISO 9001 standard.
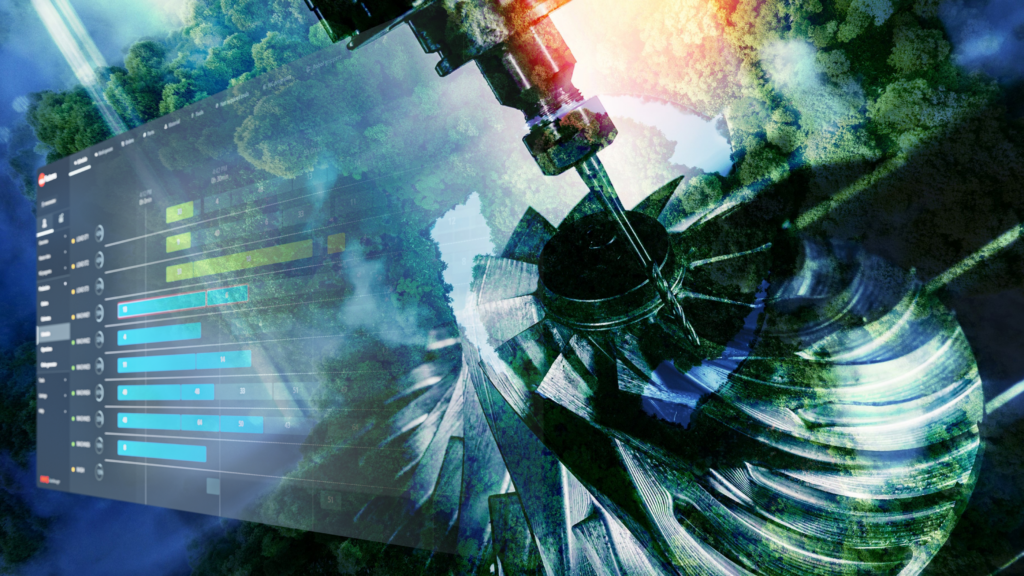
COMPETITIVITY: How Automation Makes Manufacturing More Efficient, Nearer and Just-In-Time?
Sustainability is also about healthy businesses that can provide value to their customers and thus grow the local economy. As many manufacturers are typically fighting with low margins, automation is the key factor enabling the profitability and longevity of the business. Prosperous businesses can invest more, completing the positive cycle. Read more on automation benefits.
Today, manufacturers want to make parts closer to their use thus avoiding long and potentially risky supply chains. Automation makes manufacturing competitive anywhere. This also supports the regional economy as building healthy national economies is not viable without a competitive manufacturing sector. Finally, intelligent automation enables just-in-time manufacturing, decreasing the materials and capital tied to WIP and stock. The risk of scrapping items from stock as obsolete is also reduced this way.
For example Wärtsilä, with headquarters in Finland, is a global leader in innovative technologies and lifecycle solutions for the marine and energy markets. Automation means for Wärtsilä, that their “single piece flow is just as efficient as high-volume manufacturing would be”. Read the full Wärtsilä story.
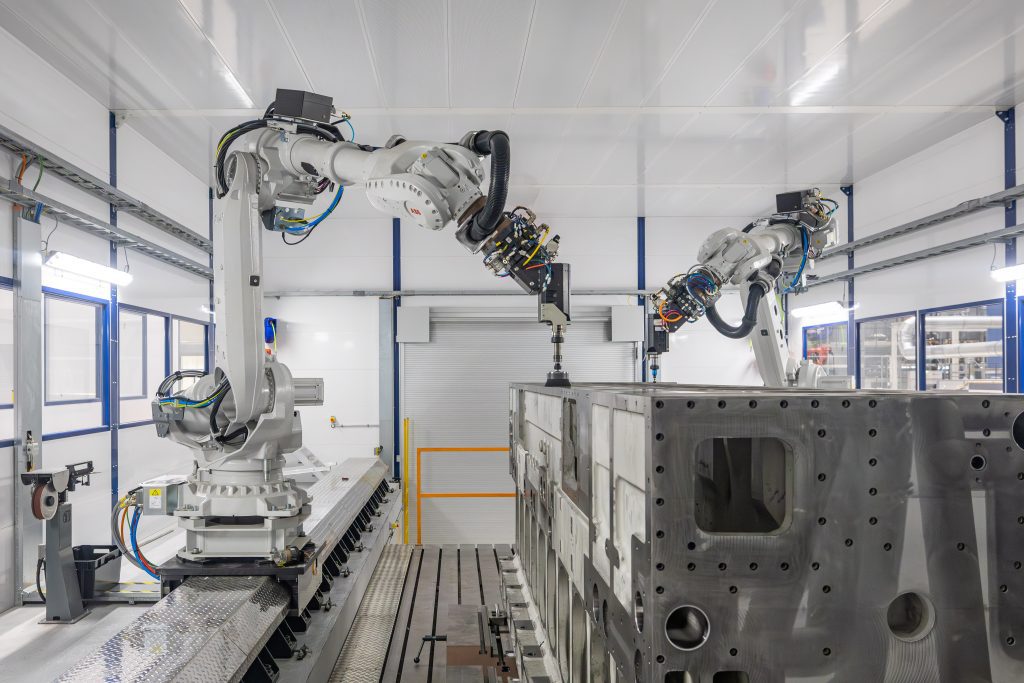
Want to Learn More?
Give us a call or send an email
Contact us
"*" indicates required fields