Automating existing machine tools is no myth or sci-fi utopia, but instead a practice that flexible automation supplier Fastems has been doing for years. The company has shown that there are plenty of situations where automating current machine tools pays off. There are always ways to navigate through the necessary technical landscape around machine tool interfacing, table or chuck access, safety and more.
A rising trend
In practice, existing machine tool automation or “EMTA” can mean automating completely stand-alone machines, machines that are already integrated into some kind of an automation system, or a hybrid of these two. In all its forms, EMTA has experienced an increase in demand that is also visible in recently published customer case studies around the topic:
- Kongsberg Automotive integrated five existing Makino a55s to a flexible manufacturing system.
- Buck CNC automated an existing Mori NT-4300 and new Index G220 turning machines into one system.
- Supset automated an existing Matsuura H.PLUS 603 milling machine.
To help manufacturers navigate the landscape, Fastems has conceptualized the most relevant perspectives around EMTA into a visual whitepaper. The paper discusses possible automation options as well as the drivers behind automating existing machine tools. Practicalities in the domains of interfacing, project management, safety and physical changes to machines are also discussed in detail.
Automation benefits for existing machine tools
Fastems’ product manager for robotized products, Teemu-Pekka Ahonen, explains the drivers behind investing in EMTA: “Production capacity is an obvious reason. Automation can boost production capacity tremendously, and also brings unique opportunities when floor space is limited. In addition to this, the classic production development parameters around machine tool utilization rate, lead times, their reliability, profitability, quality, as well as employee engagement are also very important, and a desire to improve in these often drives EMTA. On top of this, production might be lacking in analytics and KPIs, which are things automation can provide instantaneously. Finally, sometimes the existing automation hardware is malfunctioning, or there is a business risk which needs to be solved. In sum, all the so-called traditional benefits of automation are accessible for EMTA cases, and a desire for them usually drives the investment.”
Plenty of development paths
While the ‘WHY’ is being established, Teemu-Pekka continues to elaborate on the available automation options for existing machine tools: “At large, EMTA falls in two main categories. If, for any reason, a physical interface connection is not deemed viable, the production planning, resource management and operator guidance can still be automated using software like Fastems Work Cell Operations (WCO). WCO is part of the Fastems’ Manufacturing Management Software (MMS) and automates production planning and resource management tasks, boosting the efficiency of the production. If the physical interface is there, then automating the machine’s physical movement, say for example a robot accessing a chuck or machine table, is possible and unleashes the traditional benefits of flexible manufacturing.”
Succeeding in practice
The key for success in EMTA is a combination of project management, interfacing and safety. From Fastems’ perspective, an EMTA project should always consist of a pre-study phase and a project phase. Based on the information collected during pre-study, the opportunities, technical realities and the following business case can be determined in detail. In the project phase, the responsibilities of the manufacturer, the automation provider and the machine tool builder or dealer are carefully defined, and the project team is selected. After this, the schedule and disruption prevention plans are agreed upon.
Teemu-Pekka continues: “Probably the most vital part of an EMTA project is to plan and execute the interfacing of the machine tools. Things to consider include the quantity, type and age of the machines, the controller and the machine software versions – just to name a few. Close collaboration between the machine tool builder and the automation provider is necessary to succeed. The level of interfacing is carefully selected and implemented based on the manufacturer’s need, the desired outcome, and the current setup on the shop floor.”
When automating, the physical changes to the machine tools vary case by case. Relevant factors include the existing integration status and automatic pallet changer (APC) for pallet machines. The required safety level can be met either with existing safety features or by adding physical changes or connectivity to the machine tool(s).
Conclusion
The average non-automated machine tool cuts chip for only about 20% of the yearly 8,760 production hours, which means that a major opportunity remains untapped on the shop floors of manufacturing companies around the globe. Fastems is driven by a passion to help manufacturers boost their profitability and competitiveness. Because of this, developing solutions for EMTA has become a no brainer:
“We want to help the manufacturing industries get the most out of their production assets and reach the full potential of their manufacturing. This is why we see EMTA as the future: a way to sustainably boost efficiency. That’s what our 8760-mission is all about,” Teemu-Pekka concludes.
For more information, please contact:
Heikki Hallila, VP Part Automation, heikki.hallila@fastems.com, +49 1629923343
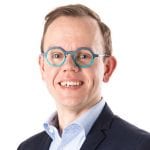