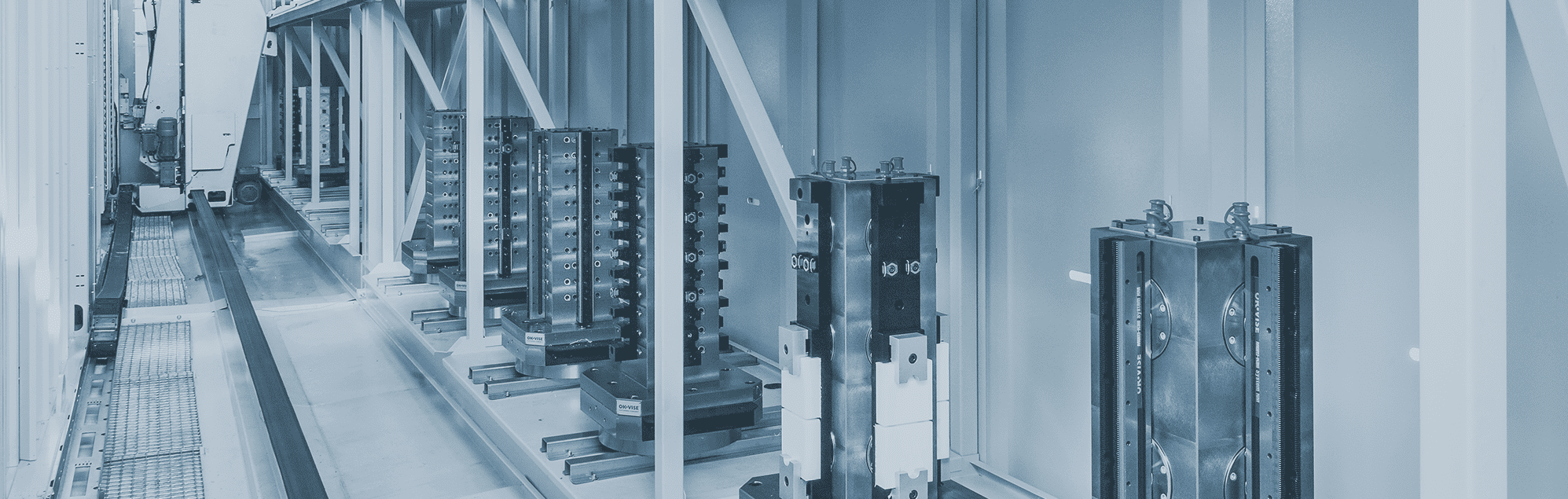
The Best Practices of CNC Automation
This page explores the best options for automating CNC machining processes like milling and turning. It also considers CNC supportive operations such as deburring, finishing, measuring, marking and more. The question is not ‘if’ one should automate but ‘what’ and ‘how’ to automate. To learn more, keep on reading!
What is CNC Automation?
CNC automation means reducing human intervention in manufacturing processes that use machine tools. In practice it can mean transferring workpieces or pallets through the manufacturing process from machine tools to other supportive devices like washing stations or measuring cells. Today CNC automation also deals with more effective management of information like constantly updating production execution plan, based production resource availability and production order priorities.
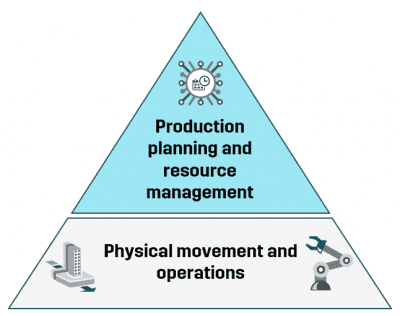
Automating production planning and resource management
Automated production planning and resource management calls for a software capable of turning production orders (e.g. from ERP) into a constantly-up-to-date plan on what should happen in the production and when. By managing the production resources like raw materials, NC-programs and tools the software can forecast any problems beforehand. It also guides the operators for right action at the right time. This gives the control fully to the production manager and makes meeting lead time requirements much easier and less stressful. Situational awareness is enabled by automated dashboards. Example of such software is Fastems MMS.
Automating physical movement and operations
Automating physical movement and operations requires automation hardware like robots, so that the system can execute the planned production (machining) in practice. This happens by transferring the machining pallets or by direct workpiece manipulation. In addition, the system can also manage the physical movement of cutting tools and integration of supportive processes like deburring, washing, measuring, marking… This level is what has been traditionally and exhaustively understood with ‘automation’ in CNC manufacturing context but is only one side of the coin as we learn in the best practices chapter.
It’s important to notice that production planning and resource management can be automated independently to physical operations but greatest benefits are achieved only when they are combined.
What Can You Automate in Each Category?
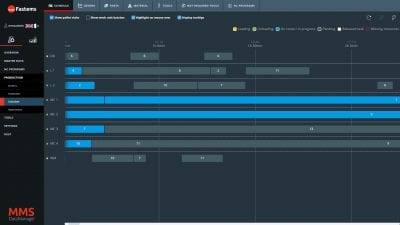
Automating Production Planning and Resource Management
Orchestrating your people, machinery and IT-systems to work as one. In practice this means features like:
- Automated information flows between different data systems and machinery or cells.
- Proactively and constantly updating production plan based on production orders and their priorities
- Automatic fetching of orders from ERP
- Operator guidance to always take the right action at the right time
- Workpiece manufacturing ‘recipe’ handling
- Managing of (complex) production phasing within production process
- Proactive resource management vs production plan and reports of missing resources.
- Fixtures, pallets and grippers
- Raw materials
- NC-programs
- Cutting tools, tool data and off-sets
- Reporting and analytics
- Production and machinery KPIs such as utilization, OEE, availability…
- Order progress views
- Inventory / work-in-progress
- Production event history and traceability
- Automated documentation (paperless production)
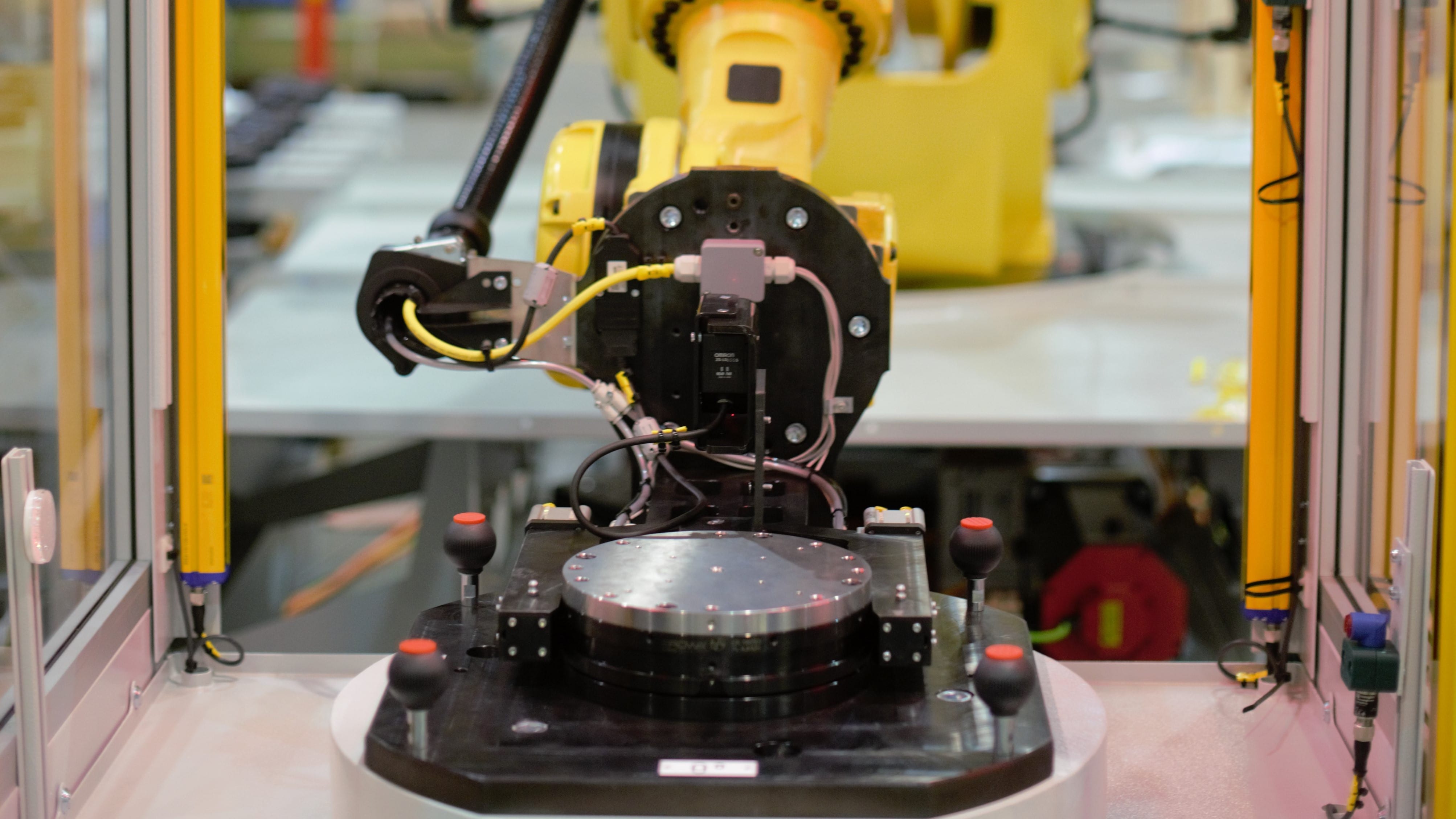
Automating physical movement and operations
Automation hardware can replicate reproducible and stable processes with very high efficiency and accuracy. In practice this can mean activities like:
- Transfers of (zero-point) machining pallets to/from machine table.
- Automated fixture loading/unloading with a robot
- Direct transferring of workpieces to machine table or chuck
- Automated chuck adjustments or changes
- Gripper and tool changes in robots
- Tool transfers to tool magazines
- Workpiece movements to/from machining supportive processes like
- Deburring
- Washing
- Heat treatment
- Washing
- Marking
- Polishing
- Measuring
- Raw material management and transfers
- Semi-finished product management and transfers
What Are the Best Practices of CNC Automation?
Here are the typical approaches to manufacturing we have observed during the four decades history we have in business. To understand the best practices, it’s the easiest to consider how intelligent CNC automation can solve the issues with the two first ways of manufacturing:
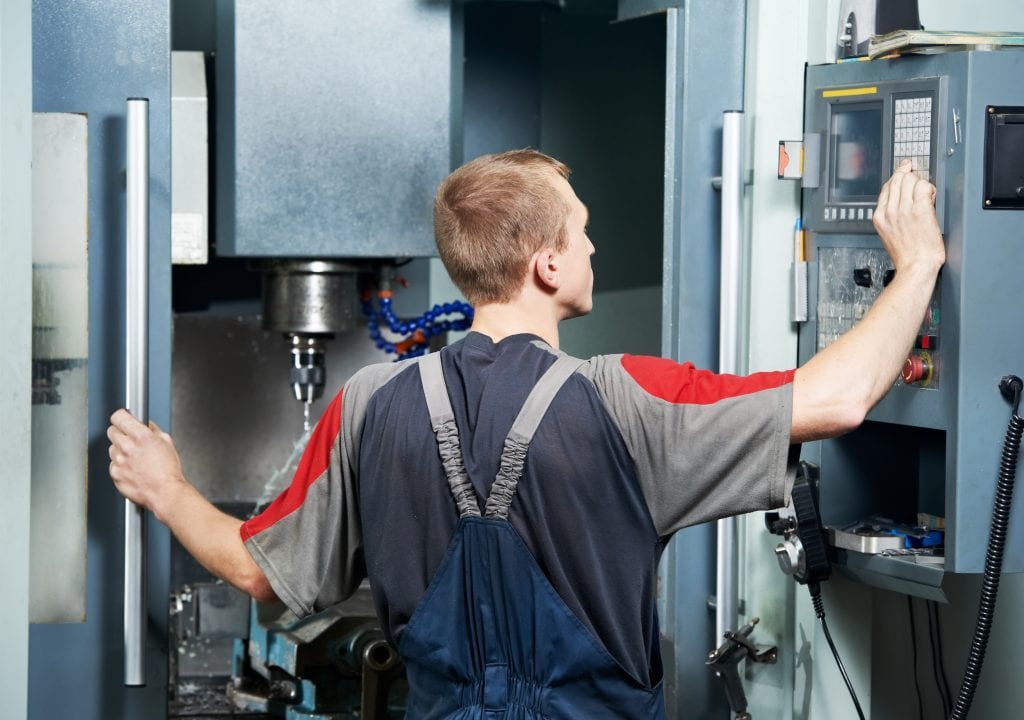
Manual Operations
Doing (something) sometimes
The first approach is the non-automated traditional machine shop where one person controls 1-3 CNC machine tools manually. This if of course a robust and proven way to operate but the disadvantages are obvious. This way, the typical machine tool can be utilized (=cutting chip) for only about 1000-2000 hours out of the yearly 8760. The reason lies in manual set-ups and all of the hassle with manual production planning, non-stable processes and occasionally missing resources like raw materials or tools.
In total this leads to longer lead times, oftentimes to quality issues and creates unnecessary work-in-progress (WIP) as parts are not truly manufactured on demand but in too large batches vs what was the actual order. This is usually because of the need to cope with set-up times.
End result: production does value adding activities only a small portion of the potential time. The production is far away from its full potential.
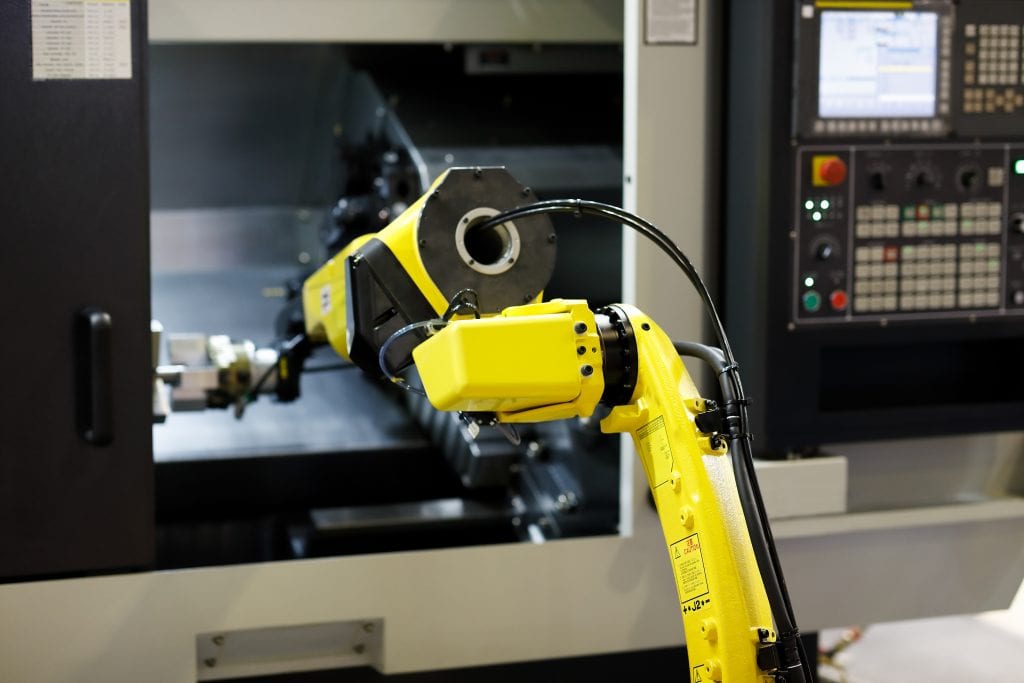
Traditional CNC Automation
Doing (something) most of the time
The second category just replaces the operator with a robot. This can mean tremendous increases in utilization as the robot/crane is capable of feeding the machine almost 24/7. As positive this sound, we have seen manufactures implementing automating this way to run lots of problems: now that the machine tool is running constantly, we can’t keep up in efficiently handling our resources, tools or smartly manage our production orders vs machining capacity. In other words: production planning and resource management become bottlenecks instead of the utilization rate leaving the manufacturing still far beyond its full potential. Before automation, the clock speed of production was slower and handling that was perhaps possible even with pen and paper or simple excel sheet.
End result: the machine tool utilization can be raised by replacing the operator(s) with a robot(s) but often that raises other issues related to production management or resource management leaving the production far from its full potential.
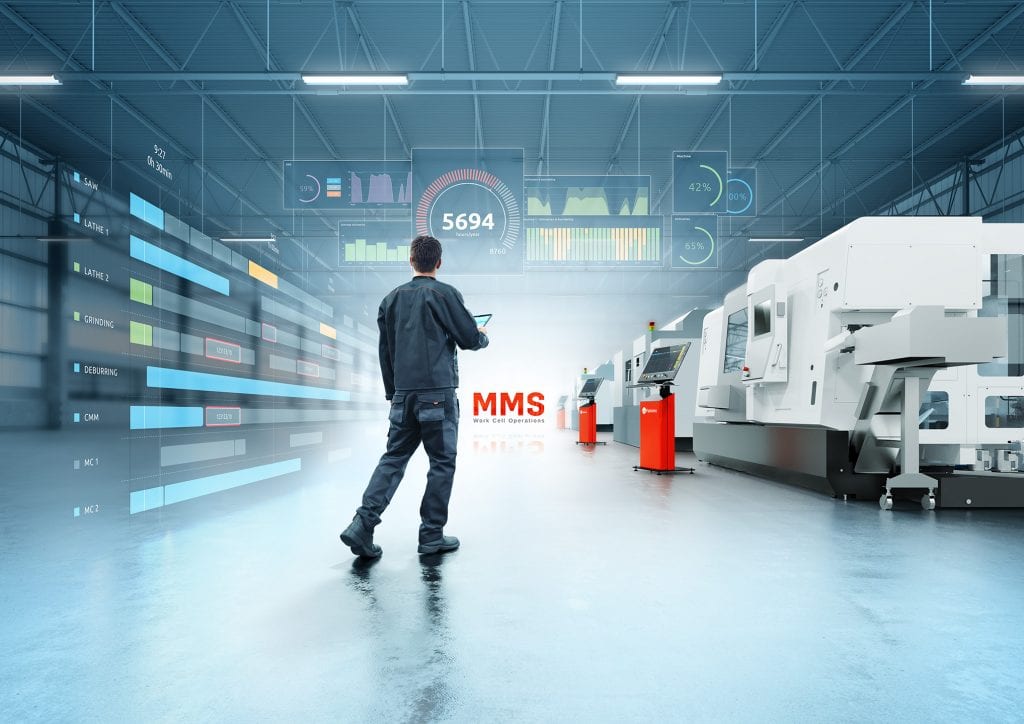
Intelligent CNC Automation
Doing the right things, at the right time – all the time
In the final stage all benefits from the physical automation of efficiently moving parts are combined with the advantages of automated production planning and resource management.
The production orders (e.g. from ERP) set the ‘pace’ of production and synchronize everything around them. The software, such as Fastems MMS, knows all needed resources and machining capacity and prompts the operators for exactly the right action at the right time. Furthermore, it alarms proactively if what is being planned can’t be done – because of e.g. missing tool from the machines tool magazine. To make production managers life easy, the production plan is automatically update based on changes such as quick delivery (skipping the production ques) or machine malfunction (re-allocating the works to other machines capable of handling them).
End result: the production as total is always doing the right things at the right time – all the time. This means most optimal machine utilization, low WIP, fast lead times, minimal hassle, high quality… Read more from the benefits section!
What Are the Benefits of CNC Automation?
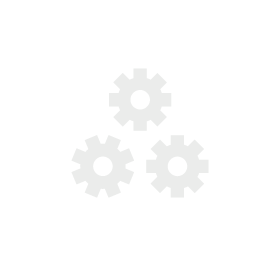
Operational excellence
Less idle times, higher and more stable quality, more effective and integrated processes, automated production planning and resource management and unmanned production are factors that result in operational excellence.
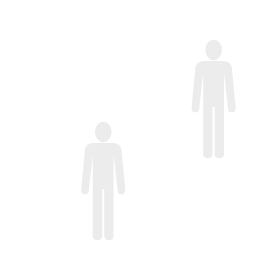
Happy customers & employees
By utilizing intelligent automation, the work of operators becomes more meaningful and safe. High and constant quality combined with fast and reliable lead times supply the customers with the right parts, right time and right measures while keeping you profitable.
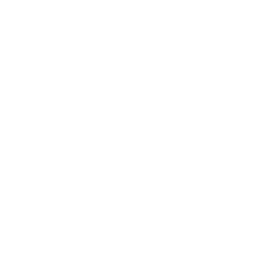
Financial performance
Higher production capacity, decreased labor and machine tool investment costs per part combined with decreased work-in-capital are all benefits enabled by automation.
What type of companies can benefit from CNC automation?
The short answer is: for almost any manufacturer utilizing CNC machinery! The longer answer takes the following chapters:
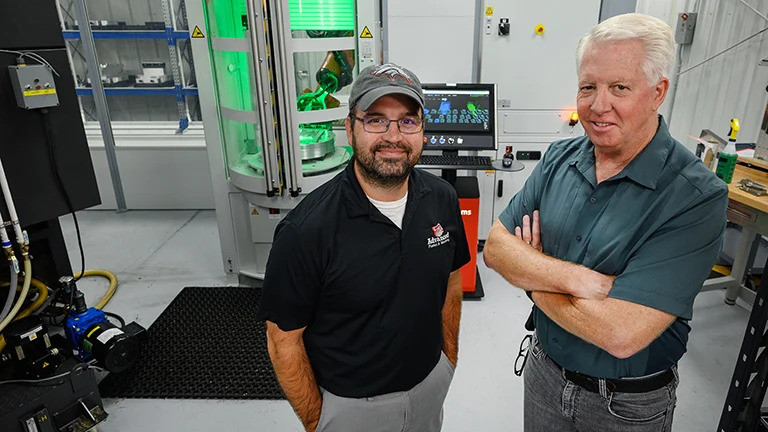
Companies of all sizes
Based on our over 4000 installed automation systems fleet, we have examples of SMEs with only a few employees investing to automation – with excellent ROI. On the other hand, mid-size corporations and global enterprises can benefit from it just alike. This usually happens in more complex technical setting in terms of production volumes & variants, process complexity, processed materials and so on.
Here are just three examples:
Product owners and subcontractors (job shops)
Product owners manufacture for their own need. During the last years, the trend of turning manufacturing into a competitive advantage has increased. This is also boosted by the re- and near-shoring of manufacturing. By controlling larger parts of the value chain, product owners can reap great benefits from manufacturing automation development.
Subcontractors (or job shops) focused on the manufacturing of certain sets of workpieces to end customers draw their competitive advantage almost completely from the efficiency and flexibility of their production. This makes them oftentimes ideal candidates for automation.
One example of automation excellence by a subcontractor:
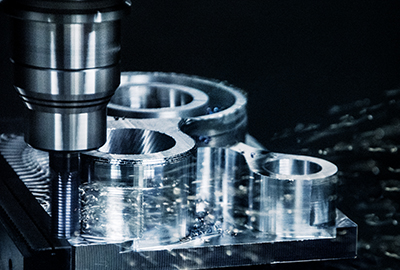
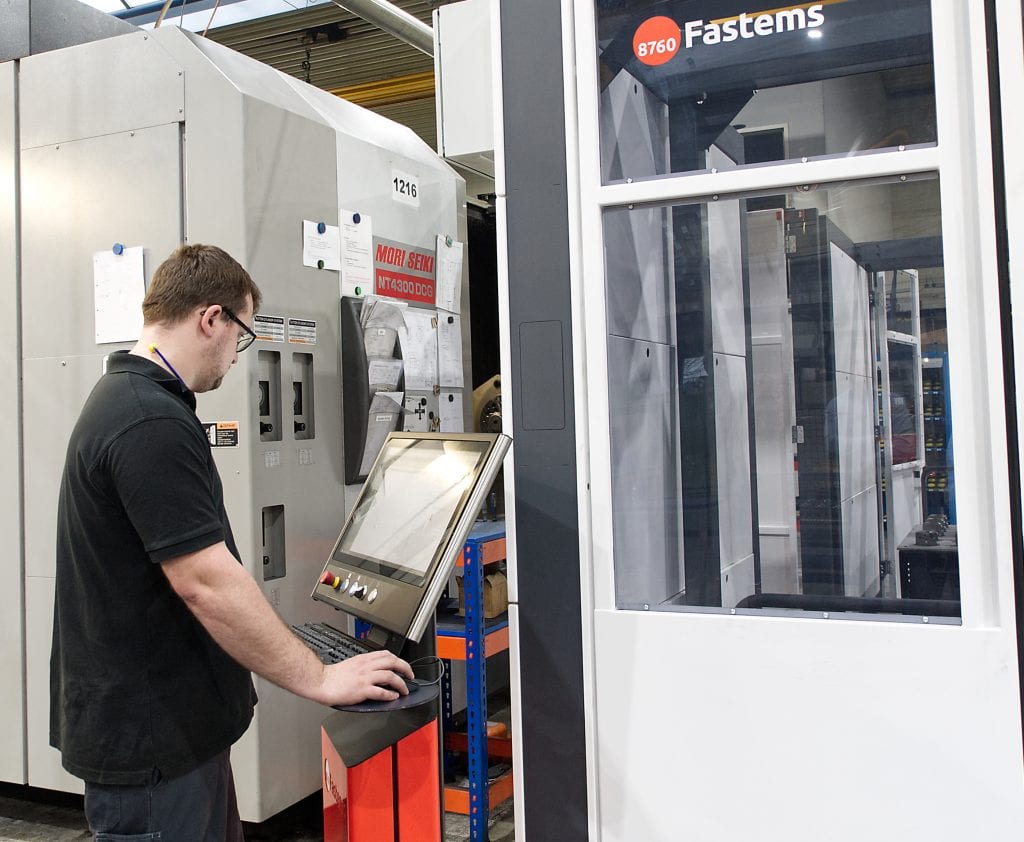
For new and existing machine tools
The usual automation investment happens when new machine(s) are acquired. This is mainly because the needs and drivers behind the investment can be met with automation – sometimes even exclusively, making the automation a must rather than an option. Practicalities also matter. Interfacing and physical features of the machines can be easily fitted to the automation solution. This could mean making sure the crane or robot has access to machine table or automation control software can transfer NC-programs or read tool data.
Automation solutions can just as well be implemented to existing machinery. One recent example of such is our customer story with Kongsberg Automotive in Norway where five existing Makino a55’s were automated to a Fastems FMS. Here the focus needs to be in good pre-study on the feasibility of the automation and then profession implementation in terms of interfacing and project management. Another example is Buck CNC Teknik where an existing and a new turning machine were integrated to a Fastems RoboCell ONE.
What Type of Industries Can Benefit from CNC Automation?
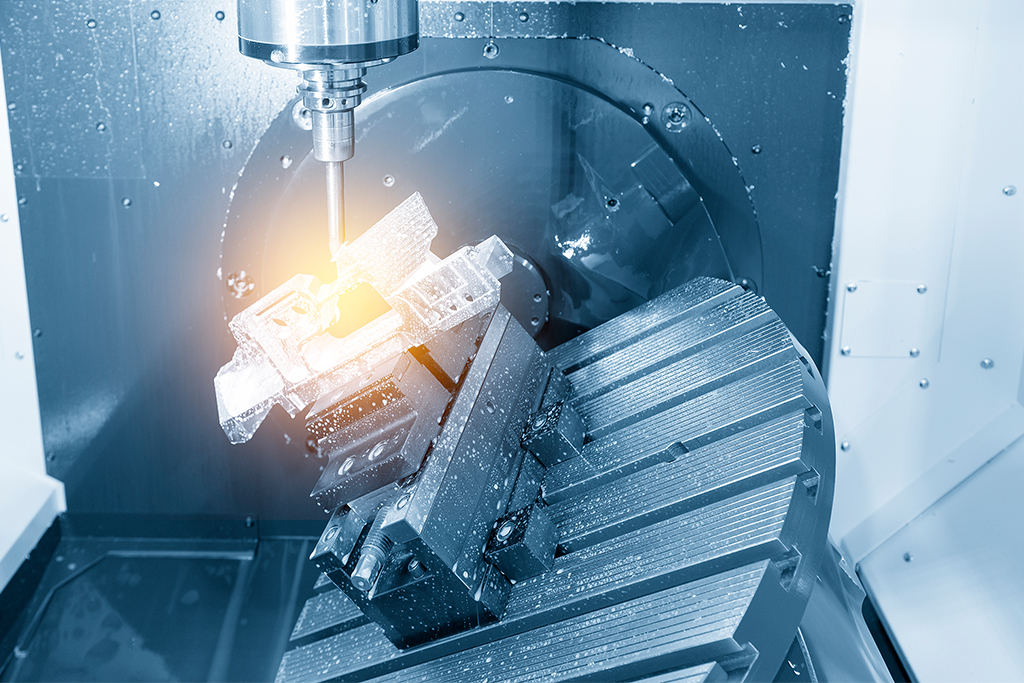
Machine Building
- General and special purpose industrial machinery
- Motor & gear components
- Die & mold equipment and machinery
- Marine industries
- Machine tools, tooling pallets and fixtures
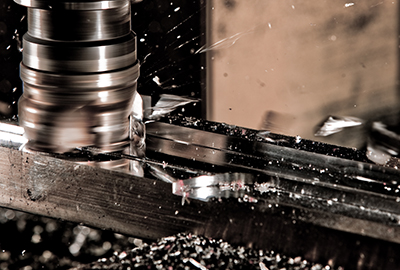
Subcontractors / Job Shops
- General subcontracting
- Special subcontracting
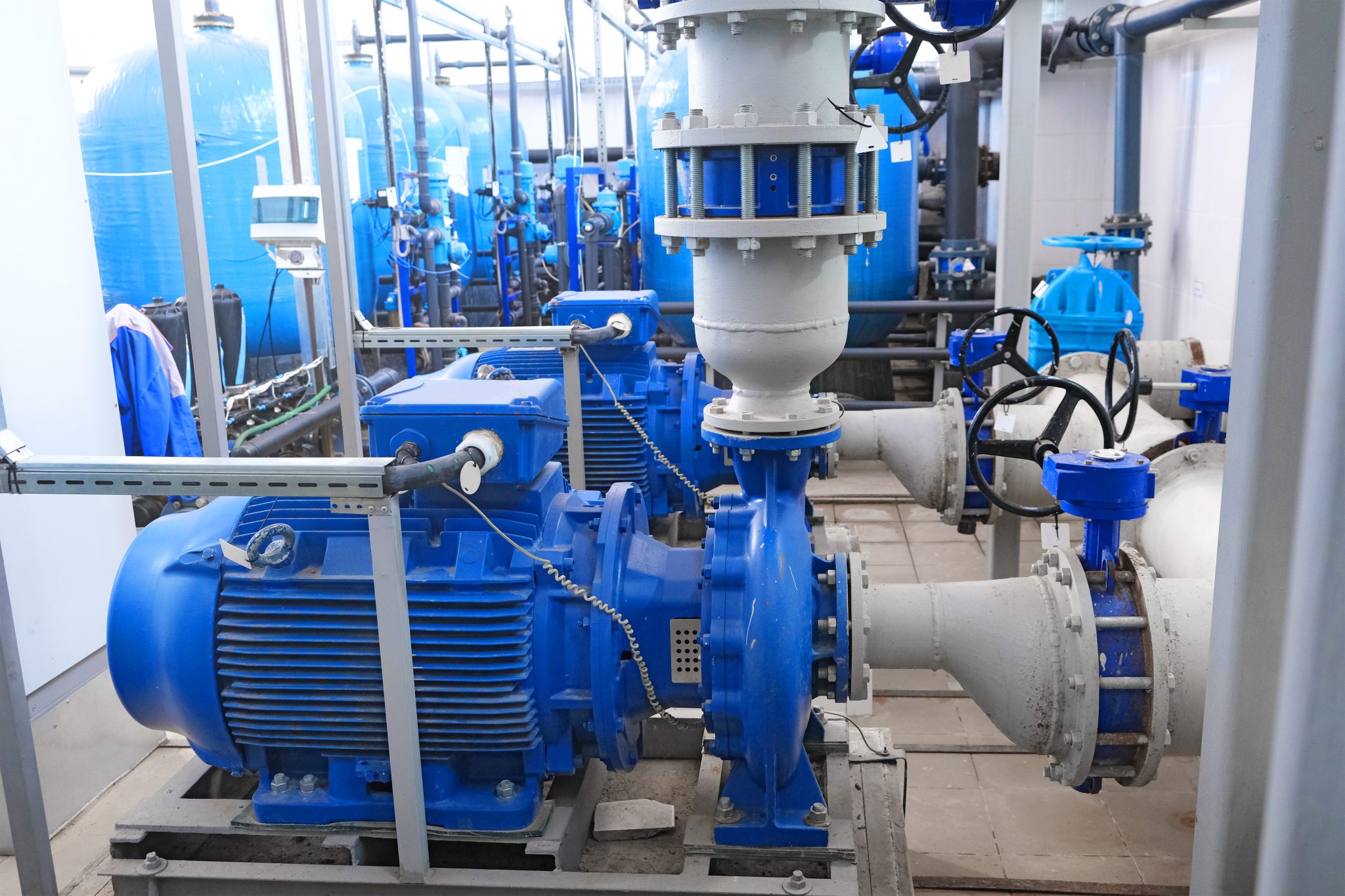
Fluid Technologies
- Pumps
- Compressors
- Valves
- Pneumatics
- Hydraulics
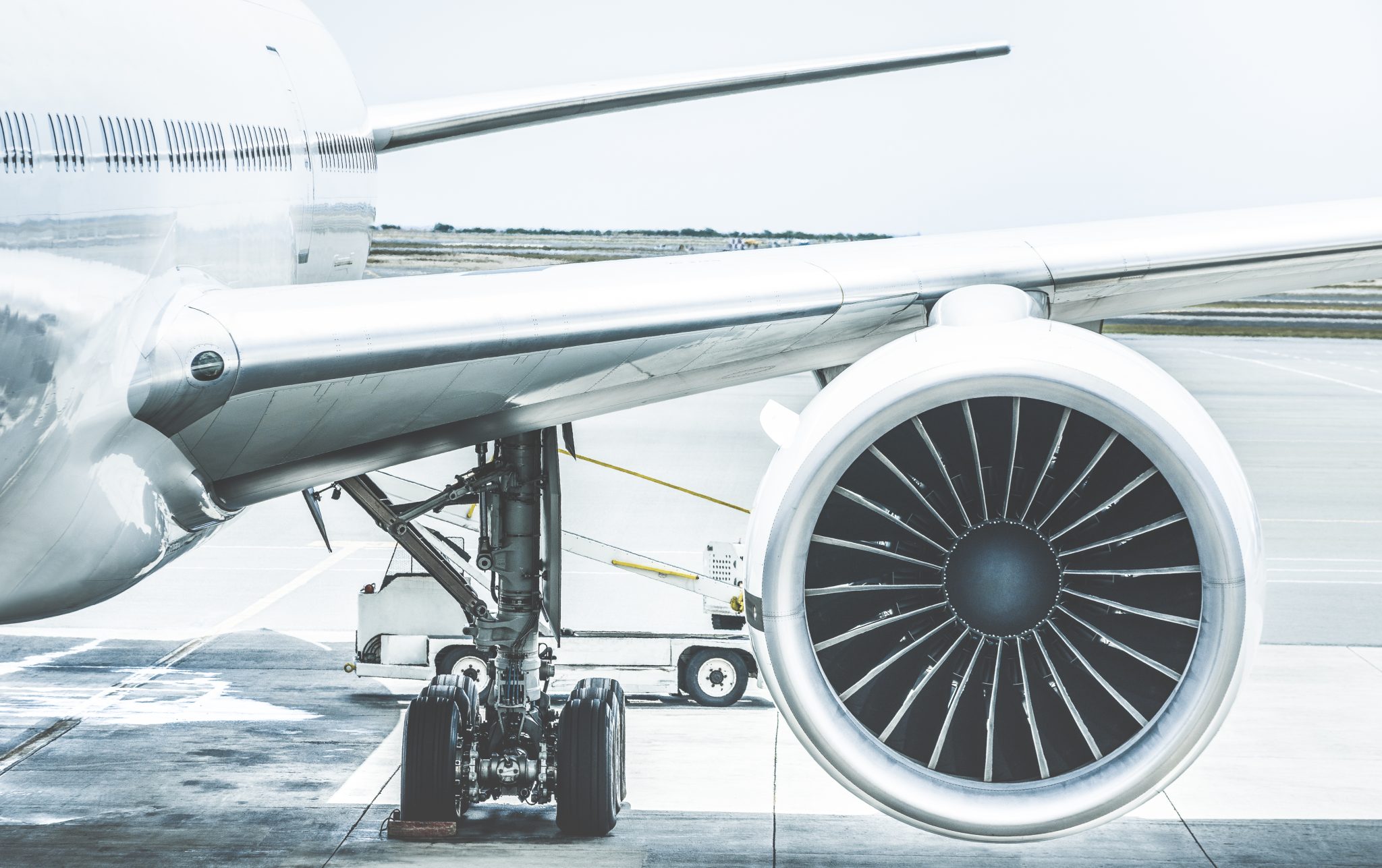
Aerospace & Defense
- Engine parts
- Landing gear part
- Interior part
- Structural parts
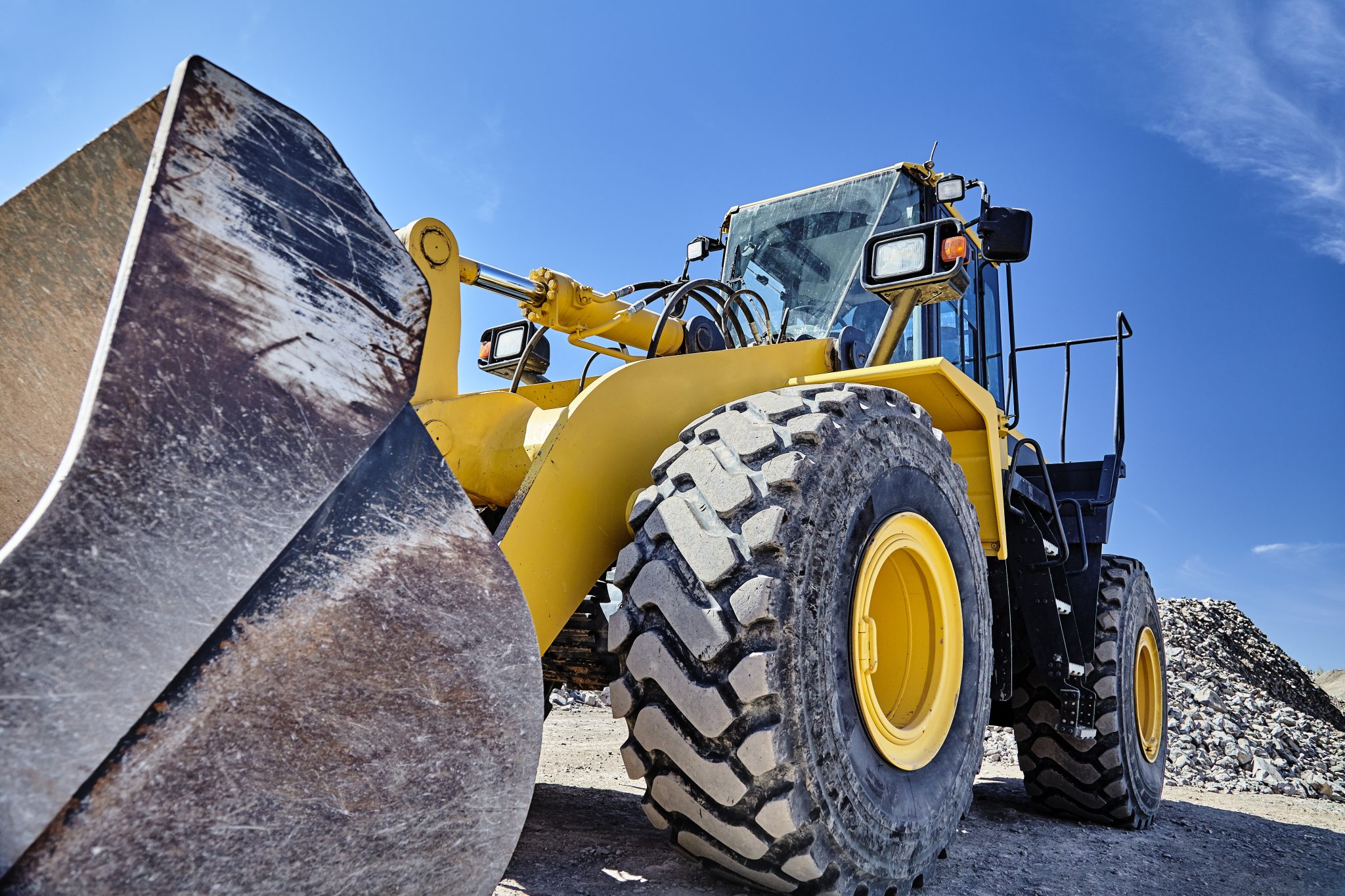
Heavy Vehicles and Machinery
- Agricultural machinery and equipment
- Forestry machinery and equipment
- Construction and mining machinery
- Trains and locomotive
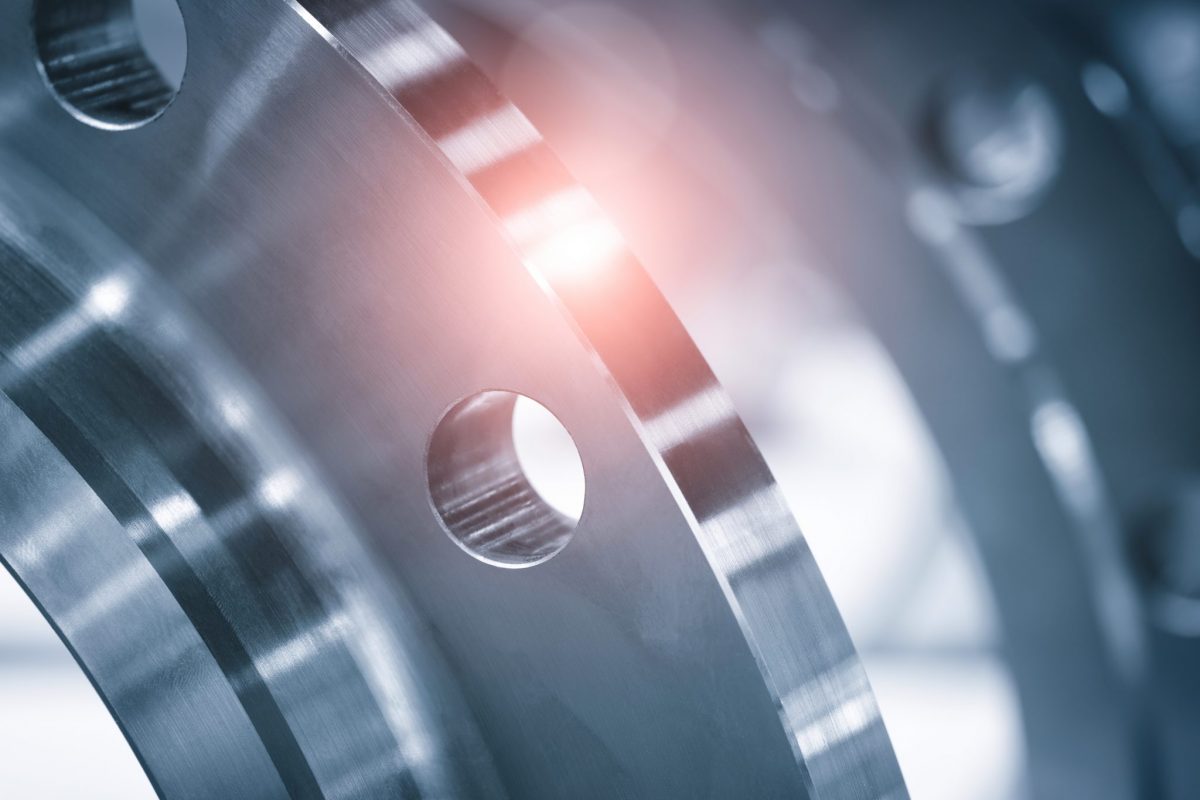
Medical
- Special purpose medical equipment
- General and special medical subcontracting
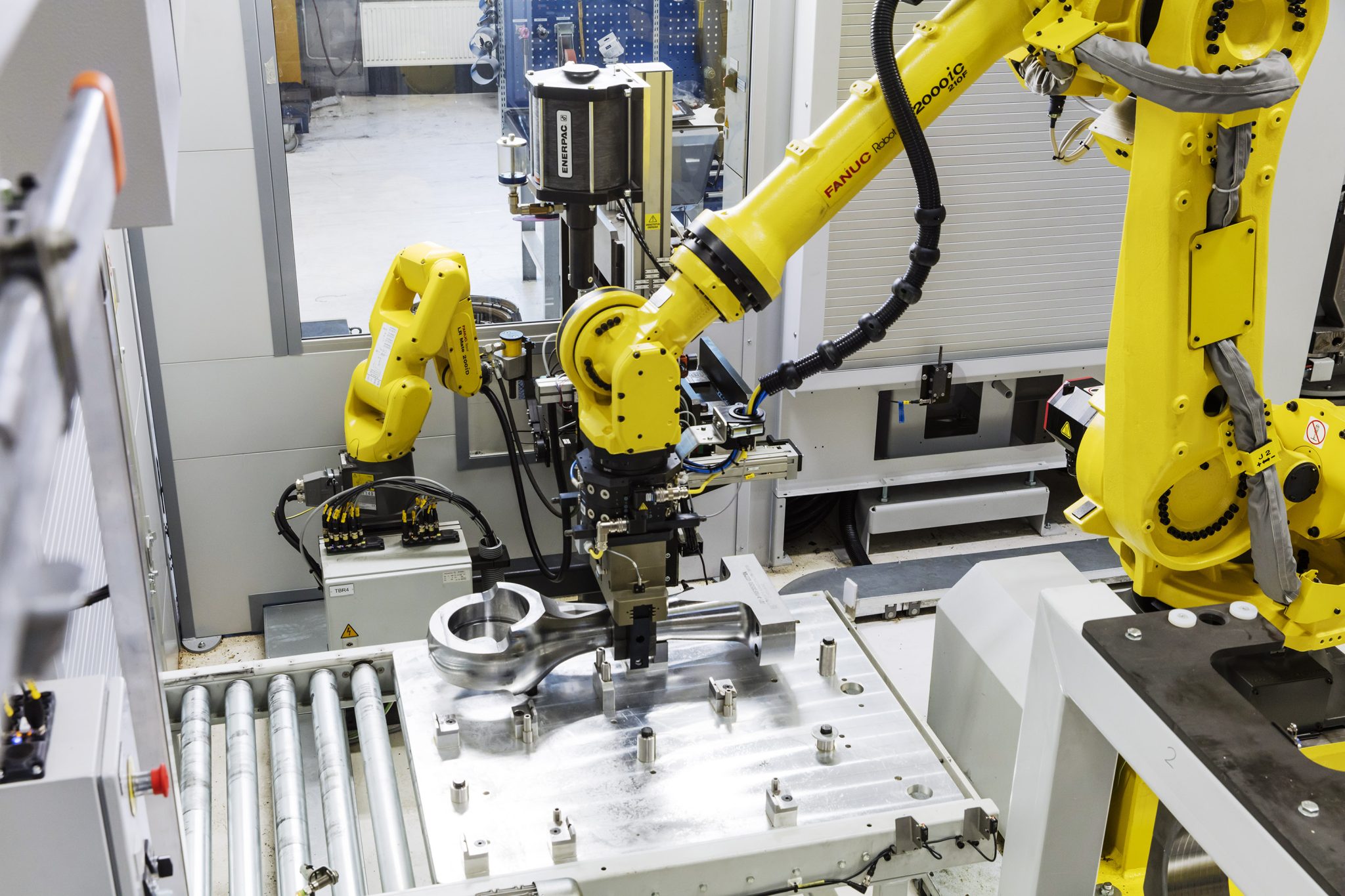
Energy
- Engines, generators and turbines
- Renewables (wind)
- Oil, gas and off-shore industries
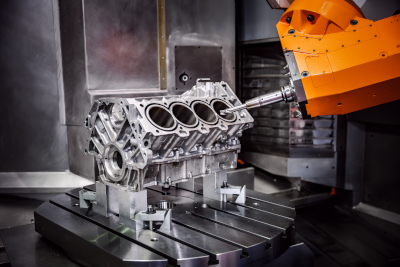
Automotive
- Sportscars & motorbikes
- Automotive general subcontracting
- Personal vehicles
- Heavy vehicles
- Other special automotive
Next steps? Download the CNC Automation guide!
If you are under consideration on how to solve the challenges of production cost per unit, high WIP or inventory, long lead times, ensuring quality and tracing, this guide is the one to download.
"*" indicates required fields
Contact us
Give us a call or send an email
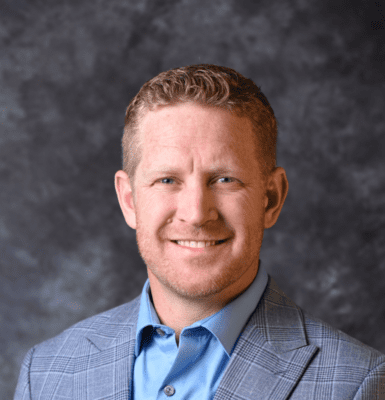
"*" indicates required fields