Intelligent Automation Enables Order-driven and Sustainable Manufacturing at Wärtsilä

“We walk the talk. Our ambition is to decarbonize the marine and energy sectors, and we make our own operations as sustainable as they can get. We only produce per order and have made our single-piece flow just as efficient as high-volume manufacturing would be. Practically, our production incorporates high equipment utilization, precise quality on the first run, and short delivery times for our customers.”
This is how Juha Päivike, Logistics Chain Director describes their goals and ambitions at Wärtsilä’s Sustainable Technology Hub (STH), their newest and largest production site opened in 2021 in Vaasa, Finland. With the global climate targets to reduce ocean transport emissions by 75% by 2050, and the rapid increase of renewable energy sources also in other industries, Wärtsilä’s strategy helps their customers to make the most out of this transformation.
“1 out of 3 ocean-sized vessels is equipped with Wärtsilä’s technology.”
“Our solutions are mostly used for power generation in vessels and as regulator power in energy plants. A l lifetime of an engine can be as much as 40 years – to reach the climate targets within the next 25 years, we need to act now,” Päivike says and continues: “We delivered the first methanol engine to a customer last year, and today already 25% of our order pipeline consists of engines that run with renewable fuels.”
A big business turnaround has also made Wärtsilä rethink their manufacturing to pace up their R&D and streamline processes for maximum customer benefit. Having partnered with Fastems for over 30 years already, the manufacturing facility of STH is an impressive example of how process development, flexible automation and high integration level pay off in production efficiency and quality. We asked from Rami Hakala, Senior Development Manager at Wärtsilä how STH manufacturing differs from their previous process:
“We have a long history using Fastems flexible manufacturing systems, so we already had automated machining as well as many other processes such as finishing, washing and measuring. But we had automated these as separate cells. Now we have integrated all processes into a single system where we just input raw material and then get ready components out. And it’s not for just a few different components – it is for over 60 of them.”
Two Highly Integrated Systems Producing Over 60 Different Components
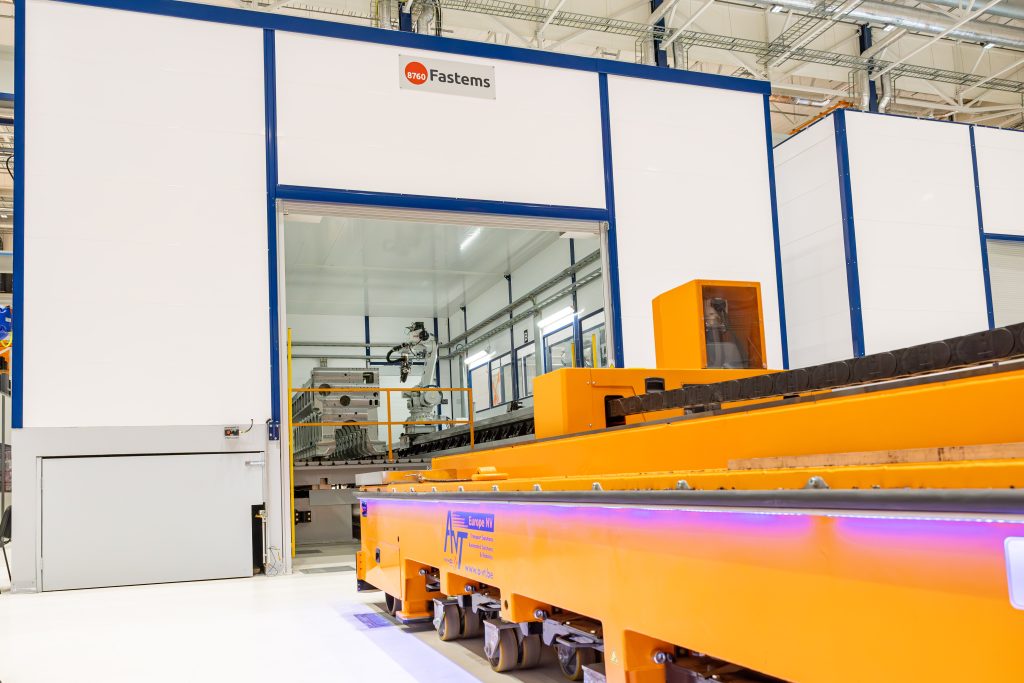
Wärtsilä´s STH manufactures engines and components for three different use cases: new orders, spare parts for engines in use, and R&D purposes. In the machining area of the 60,000m2 production hall, there are two flexible manufacturing systems by Fastems: AGV-FMS for engine block manufacturing, and Multi-Level System for manufacturing components attached to the engine blocks. Like all Fastems automation systems, these systems are controlled by Manufacturing Management Software (MMS) which is specifically designed to plan and run high-mix manufacturing efficiently.
“MMS fetches customer orders from our ERP automatically and then schedules production of both systems so that every engine block and its components are ready just in time in our assembly. We don’t need to produce parts to inventory, and our production is flexible when demand varies. In addition, we have integrated quality assurance process in both systems to ensure top quality and full traceability for each component,” tells Tero Kujamäki, Manufacturing Technology Development Manager at Wärtsilä.
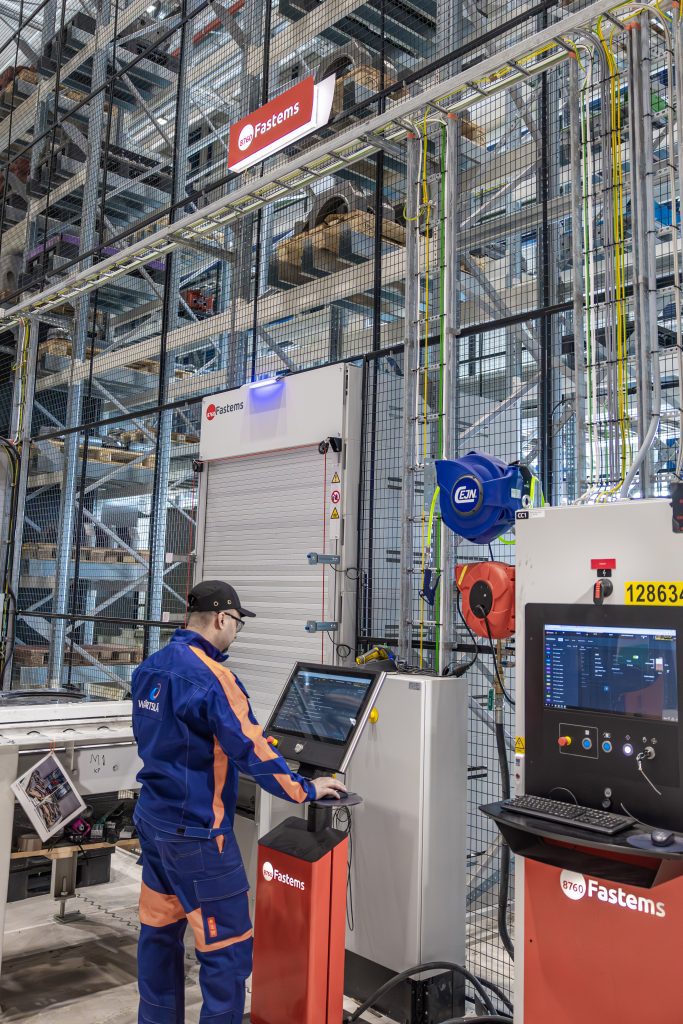
“What we are especially proud of is the new ‘fast lane’ for urgent customer orders. Our production system is capable of automatically adapting to any changes, meaning we can just prioritize our rush jobs in ERP and then MMS finetunes the production schedule so that we meet our delivery targets. If we couldn’t reach that target MMS would also notify us on that well in advance so that we can consider the options,” says Hakala.
“Now we have integrated everything into a single system where we just input raw materials and get the ready parts out.”
There is one more automation leap Wärtsilä has taken in STH: they have automated tool delivery and data management with Fastems Gantry Tool Storage (GTS). GTS stores over 750 cutting tools in a centralized way and based on the production plan, it schedules the tool usage and delivers each tool to six different machining centers just in time. When a tool is worn out, GTS delivers the tool automatically back to the tool room for reworking. GTS also automatically provides the machines with tool off-set information from the pre-setter.
“Our tool operators always know – in advance – which tools need to be reworked to keep the spindles running. This system allows sharing tools between machines instead of equipping every machining center with the full tool set,” says Kujamäki. “We can also monitor tool usage and for example, build additional pieces of bottleneck tools if needed”.
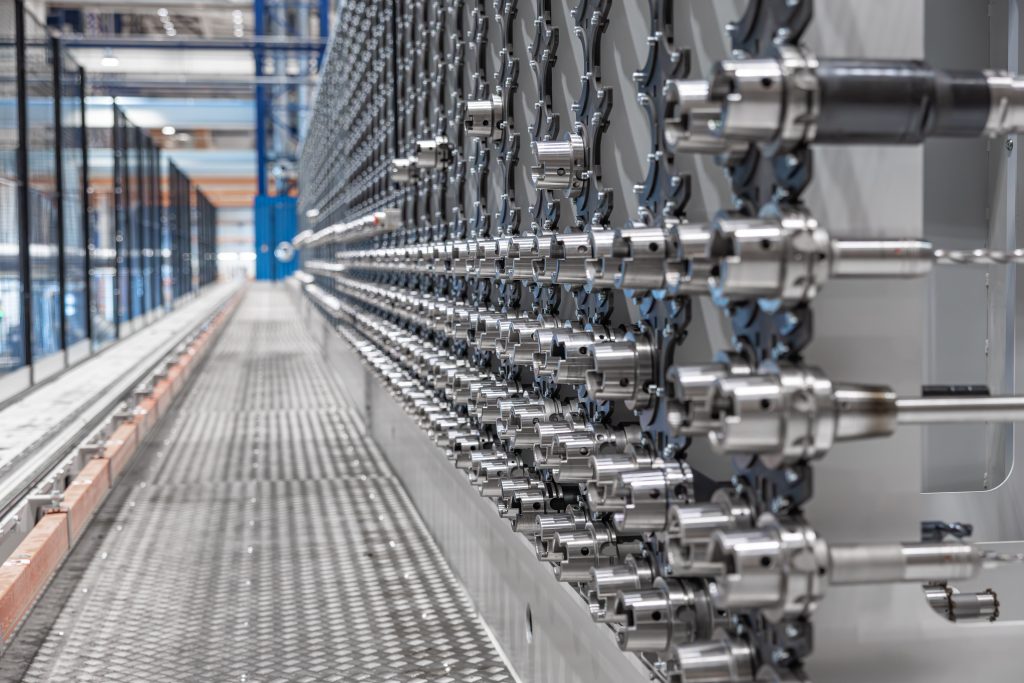
Wärtsilä is available for their customers 24/7, and the same applies to their production. The day shifts prepare all the materials and programming, and the evening and the night shifts, of just a couple of people, take more of a monitoring role in unmanned production. “We don’t have traditional machine operators here – we offer people more specialist roles where they can focus on production development rather than fighting to keep the machines running. This is certainly one reason why our people retention is at a good level,” says Hakala who himself has worked at Wärtsilä for over 20 years already. “With our great team and partners, we have been able to develop this system and now we want to see how much more we can still get out of it!”
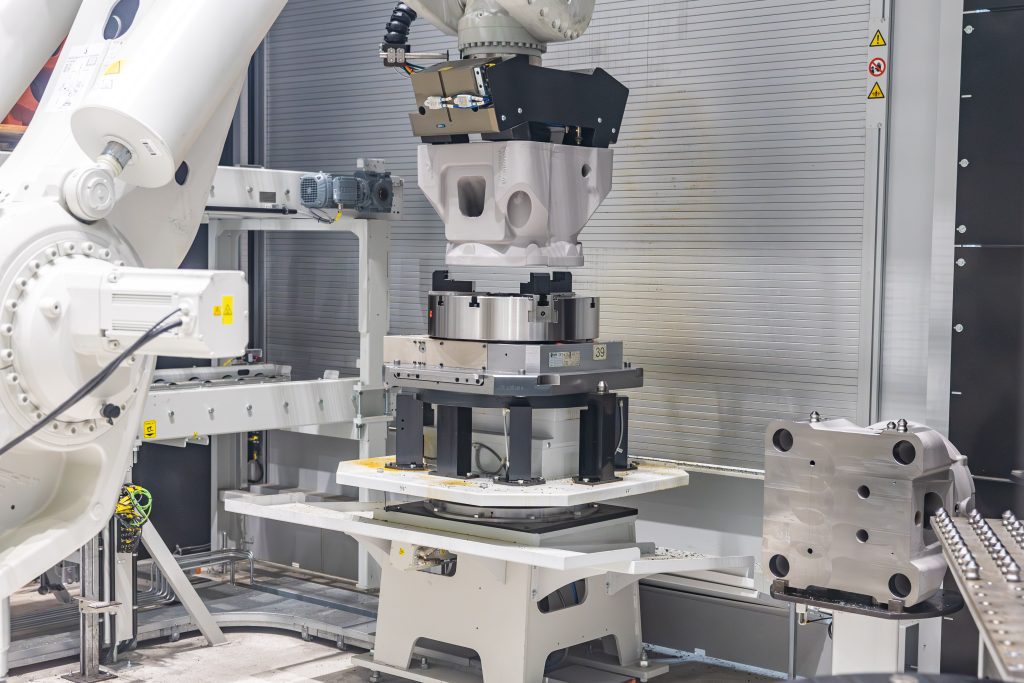
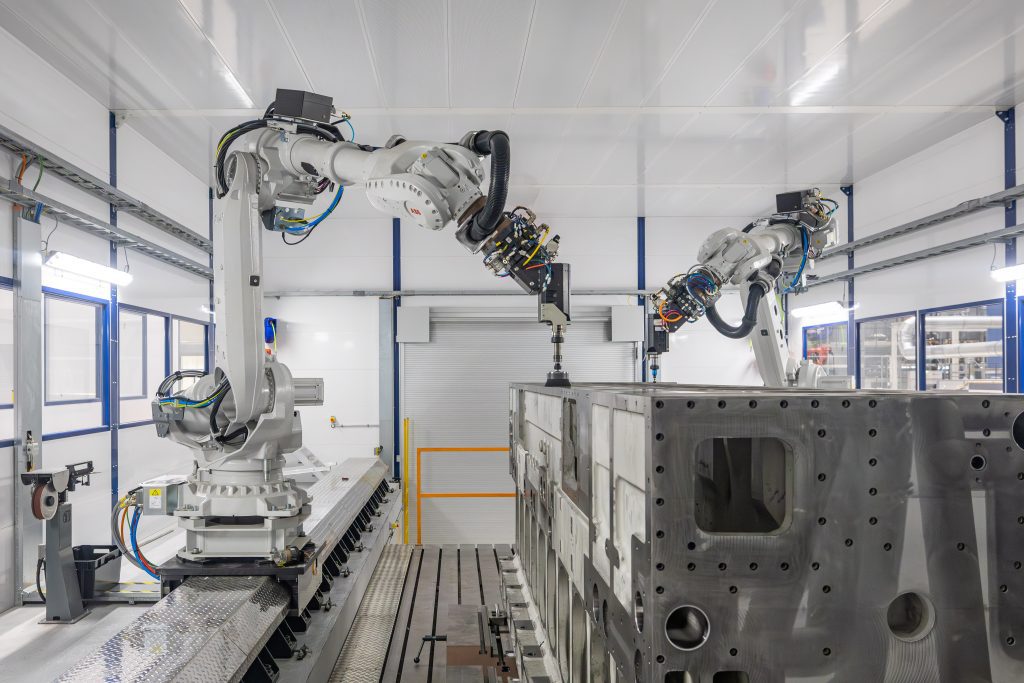
Fastems Systems at Wärtsilä STH
Multi-Level System MLS
With this flexible manufacturing system, Wärtsilä manufactures over 60 types of connecting rods and cylinder heads for their engines. The machining cycles vary between 10 minutes and 8 hours. The system includes:
- Five HELLER horizontal machining centers
- Crane for moving the pallets
- 60 machining & 124 material pallets
- Cutting tool deliveries (also for a large portal machine in AGV-FMS)
- Robotic clamping of parts into pallets (ALD)
- Automated washing, deburring and marking
- Automated inspection (CMM)
- Automated sub-assembly
AGV-FMS

The large engine blocks weighting up to 60 000 kg are manufactured with this FMS that utilizes a large AGV instead of traditional crane as a transfer device. The system consists of:
- WaldrichSiegen portal machine
- One AGV moving the pallets
- Three pallet loading stations for clamping the engine block into machining pallets
- Storage places for four pallets
- Robotic finishing
- Robotic assembly
- Optical measuring (non-Fastems)
- Washing (non-Fastems)