Bringing Transparency and Situational Awareness to The Shopfloor – Factory Cockpit at Tasowheel
Tasowheel is a Finnish family-owned contract manufacturer founded in 1979. The company has established itself as a leader in precision engineering with over 45 years of experience.
Renowned for its expertise in power transmission, controlled motion, and complex machining, Tasowheel specializes in the design and manufacture of high-quality components, sub-assemblies, and gearboxes. The company’s in-house capabilities span the full production cycle – turning, milling, hobbing, gear shaping, hard turning, grinding, and gear grinding – allowing them to deliver tailored, customer-specific solutions. With cutting-edge facilities and a commitment to quality, Tasowheel excels in producing multi-staged precision components, even those with complex geometries and tight tolerances, for both small and large production series.
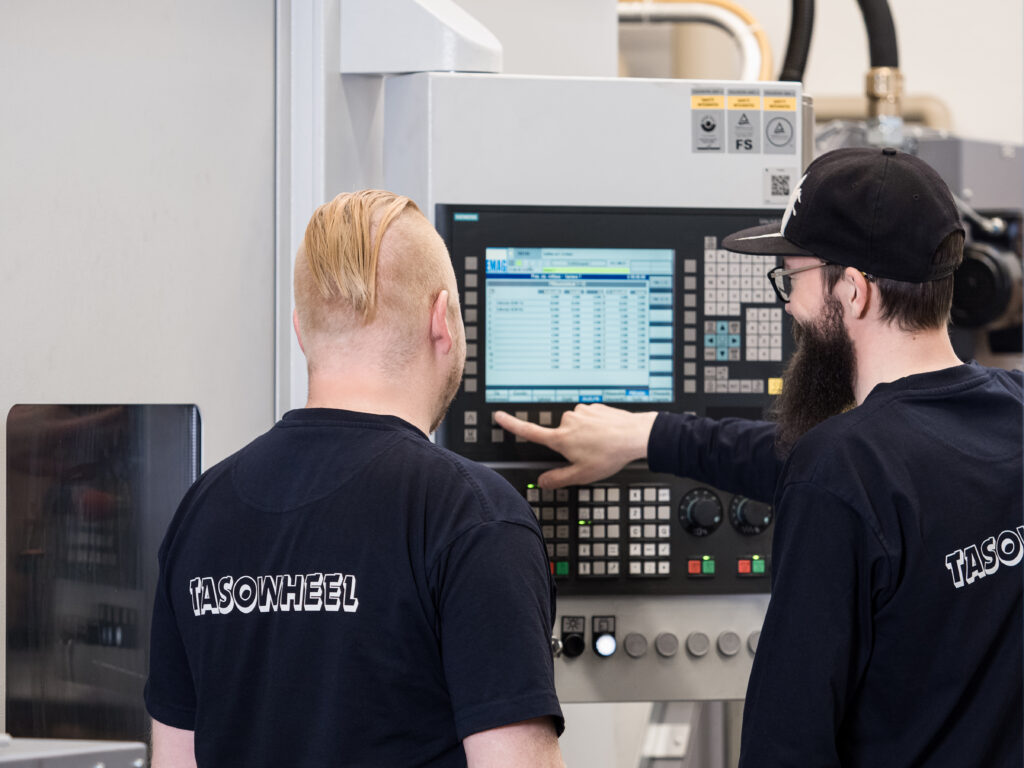
The Need for Digital Transformation
Manufacturing companies, Tasowheel included, often face challenges related to limited visibility into machine activity and utilization, which can lead to communication gaps between production leaders and planners. This lack of real-time information might make it more difficult to ensure that production is progressing according to schedule.
Another common challenge in manufacturing is maintaining efficient machine utilization and minimizing downtime. Without clear insights into machine performance and production processes, workers may spend excessive time troubleshooting issues and managing the operation when unexpected production stops occur. This can lead to bottlenecks, under-utilized resources, and difficulties in optimizing production schedules. As a result, overall efficiency is decreased and order progress can be slowed down.
Recognizing these issues, Tasowheel aimed to find a solution that improved real-time insights, supported informed decision-making, and helped improve communication among different departments within the organization. The company also recognized that digitalization was crucial in ensuring such seamless information flow across all levels; making it easier for managers to make informed decisions and enabling operators to stay fully aligned with the production plan. This not only enables quicker responses to problems but also strengthens knowledge-based management by providing more data on potential challenges. As a result, transparency is improved from the shop floor all the way to upper management, and that is what Tasowheel was aiming for.
Introducing Factory Cockpit
To improve manufacturing digitalization, Tasowheel partnered with Fastems to implement Factory Cockpit, a leading production analytics tool for manufacturing. FC connects IT systems like ERP or MES and shop floor machinery, offering real-time view to production key metrics, machine statuses and the progress of production orders. The outcome is full situational awareness, enabling faster and better decision making, production process development and more.
Jarmo Kuikka, the former Managing Director of Tasowheel, concludes on the pilot project, “ Factory Cockpit is a must-have. It has enabled real-time production visibility and tools for tracking production efficiency and sharing information conveniently.” Let’s look at what that means in practice and how the implementation of Factory Cockpit took place.
Implementation Project
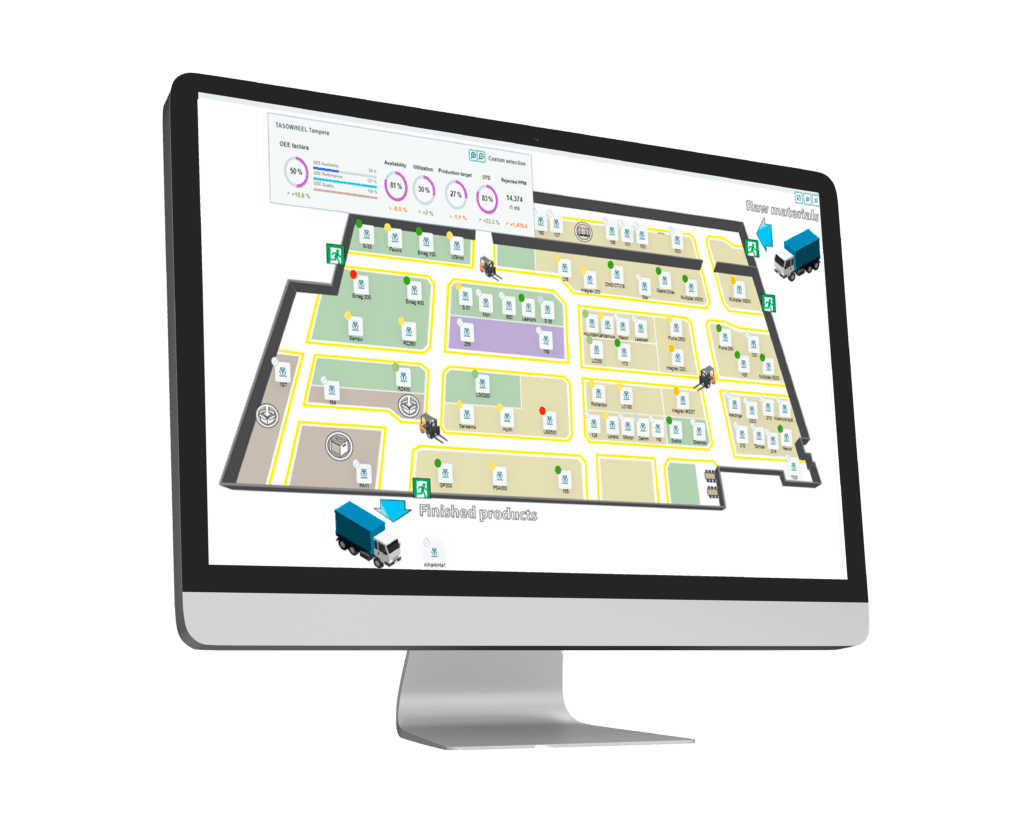
Figure 1. Photo of Tasowheel’s factory floor, depicted in Factory Cockpit with factory-level KPIs and metrics
At the start of the project, it was concluded that Tasowheel has had sufficient data and capabilities for effective production performance analysis. However, to enhance the accuracy and reliability of this production planning data, direct information from machines is also essential. Combining these datasets was a key objective of Factory Cockpit, therefore the integration between these different systems was implemented.
Tasowheel has already implemented basic data collection for some of its machines, but the goal is to gather valuable insights from all equipment. This includes data from different kind of machines from all production plants. Given the complexity of gear production, which involves numerous operations, it is essential to ensure that data integration is done thoroughly and precisely to guarantee the reliability of the analytics. Therefore, although they could have opted for a machine integration service from Fastems, Tasowheel decided to work with a third party familiar with their machines and production history. This approach allows for the optimal integration of raw machine data into Factory Cockpit for comprehensive analysis.
Factory Cockpit communicates with Tasowheel’s API Rest, utilizing the same data that feeds the PowerBI reporting system, production planning software, and ERP, which are all integrated. This ensures that machine data is consistently shared across platforms for real-time insights. The data is stored in the cloud, forming the basis for data visualizations and the calculation of critical manufacturing metrics such as Overall Equipment Effectiveness (OEE) and utilization rate. In addition to these, Factory Cockpit tracks other essential order-related metrics, error metrics, and combines order and machine Key Performance Indicators (KPIs) to provide a comprehensive overview of operations.
With Factory Cockpit connected to 60 machine tools across Tasowheel’s multiple sites in Finland, it delivers consistent KPIs and insights, ensuring that all production activities across different locations are seamlessly integrated and monitored. This centralized approach enables Tasowheel to maintain high standards of efficiency and quality across all its facilities.
Benefits
For different user groups FC enables different use-cases and values.
For operators, Factory Cockpit provides convenient access to production order statuses, making it easier to meet daily goals and enhance efficiency. In this view, the production plan of the day is specified, with production metrics, goals, and current performance displayed clearly. This allows operators to have instant access to the current production flow and know the targets clearly, so that they can do their job more efficiently.
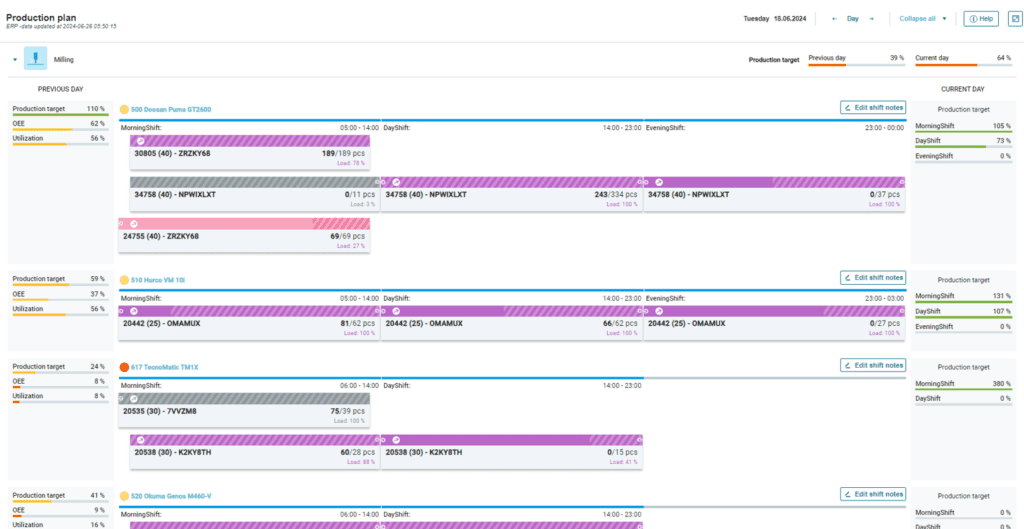
Figure 2 In this view, the production plan of the day is specified, with production metrics, goals, and current performance displayed clearly.
For production managers and management, Factory Cockpit gives real-time information about their systems’ performance and order flows, so they can make the right decisions at the right time. Factory Cockpit also helps to identify development targets and, above all, facilitates analyzing effects of each ongoing issue and prioritizing them, so the users know what needs to be done first.
FC’s real-time data capabilities enabled accurate machine monitoring and easy target tracking, leading to more optimized production management. A practical example of this can be seen in figure 4, tracking the OEE of a specific department. This makes comparison and monitoring between departments easier.
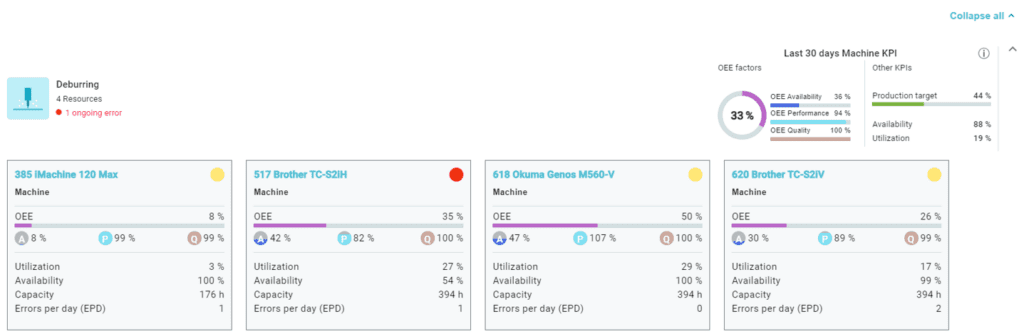
Figure 3:Factory Cockpit enables OEE tracking per department
Factory Cockpit Key Outcomes for Tasowheel
- Improved production management decision-making: FC provides a clear picture of production performance, enabling better resource allocation and timely responses to issues.
- Enhanced communication: The tool facilitates seamless communication across departments, making information sharing more efficient and allowing users to use the insights in ways that benefit their daily tasks
- Increased efficiency: By identifying and addressing bottlenecks, Tasowheel has reduced machine downtime and improve overall productivity.
- Data-driven insights: FC’s comprehensive visualization capabilities allowed Tasowheel to detect quality issues, assess product profitability, and make informed investment decisions.
Looking Ahead
Tasowheel’s partnership with FC is far from over. The company plans to further integrate FC’s capabilities into its continuous improvement strategy. With FC as an enabler, Tasowheel is determined to achieve even greater efficiency and data-driven manufacturing excellence.