Getting The Most out of a CNC Machine Tool With Automation
Originally published in Finnish on the Fastems blog
The automation of an existing machine tool turned out to be an investment worth making for Supset. In fact, through the investment the CNC subcontractor gained both the capacity and confidence to meet future demands.
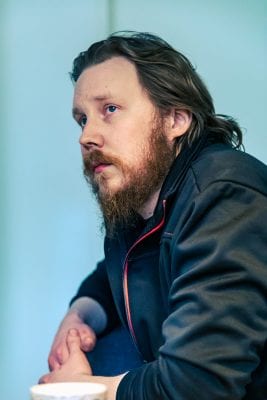
Henri Kolehmainen is in charge of developing Supset’s production
The Machining Expert Grows and Develops
Two years ago, Supset’s existing 4-axis Matsuura H.PLUS 603 was automated with a Fastems FPC (Flexible Pallet Container). The particular machine had already previously been automated, but the machine’s low utilization rate prompted Supset to search for other alternatives. Now, by the combination with the Fastems FPC, the Matsuura’s production capacity as increased nearly by 50 percent and the relability is excellent.
Supset is a versatile CNC contract manufacturer located in eastern part of Finland. The company was founded in 2005 and currently employs 25 of the industry’s experts with annual turnover of around three million euro. Supset’s long term goal is building strong and cost efficient relationships with its contract customers. CEO Pekka Kolehmainen is in charge of running the family-owned company and Henri Kolehmainen is responsible for production development. Among other things, Supset manufactures industrial heavy vehicle parts from cast ADI-steel (austempered ductile iron).
“Machining ADI is no walk in the park. As a material, it’s hard and produces long, tough chip. We have around 15 different parts in production from this material, and batch sizes are small, some dozens of parts”, explains Henri Kolehmainen.
From an Idea to Execution – Automating Existing Machine Tools
The idea behind making a new automation investment kicked off with a trip to the UK, remembers Henri. “We visited a factory that had a similar automation unit to the Fastems FPC. We had heard about the benefits of the solution from other manufacturers and now we got to see it for ourselves. It was easy to calculate the return on investment and we knew it was a solution that really worked. This truly turned out to be the case, as we haven’t had much trouble with the FPC – only one interference over the past two years. People in this industry understand how valuable it is to have production that runs smoothly”, notes Kolehmainen.
In the beginning of 2018, Supset contacted Makrum: a Finnish representative for Matsuura. Through them, Supset heard about an inexpensive and easy way to automate existing pallet machines – The Fastems FPC. Thereafter, the planning of the automation was then carried out together with Fastems Sales Manager Matti Nenonen and Makrum’s Marno Miettinen. In the end, Fastems delivered the automation solution and Makrum played an important role in the machine interfacing.
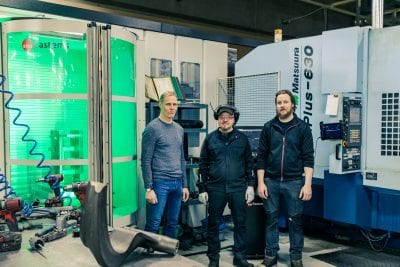
Pekka Kolehmainen, operator Petri Toivanen and Henri Kolehmainen infront of the FPC ja Matsuura machine tool.
The integration of an existing machine tool with any automation solution always requires case by case planning. The needed mechanical changes in the pallet machines might have to do with access to the machine table. In addition, machine integration has to take into account the level of data transfer. In the more simple cases, an NC-program’s start signal is enough. In more complex cases, machine integration can involve the transfer of NC programs, tool data and information related to machine status.
For Supset however, the planning and execution of machine integration was straight forward. The company quickly received confirmation from Matsuura Germany that the integration can be carried out according to Fastems’ interface description. In more practical terms, the integration was tested and executed as a combined effort by Makrum and Fastems during installation. The project was carried out on schedule, and the comissioning only required a two-week production stop.
Day-to-Day with FPC
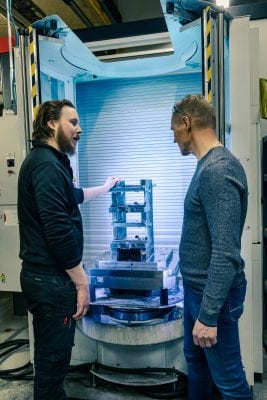
Henri and Pekka Kolehmainen are pleased with the results of day-to-day production with the Fastems FPC
“We are still learning how to get the most out the system. This kind of a change affects the entire organization’s operations, and we’ve have been learning how to better utilize work queuing features. For example, we recognize that we still have untapped potential in lights-out manufacturing capacity. What’s most important however, is that we now have the capability to unleash this. It feels good to see that production is running even as I arrive to work in the morning, because the demand is definitely there.”
The machine tool is typically utilized for around 20 hours a day. The remaining four hours as well as weekends are used as needed for peaks in demand. Kolehmainen opens up the situation further: “The output of the machine is almost twice as it was before. This is a huge improvement and what’s best is that we can trust the system. According to our calculations, we have now reached availability of well over 90 percent.”
Supset’s operators learned to use Fastems MMS (Manufacturing Management Software) in a matter of hours and with only a few training sessions. The operators utilize Supset’s own support materials for daily operations and production orders are retrieved from the ERP system. The improved ergonomics of the factory’s loading stations ensures the company’s operators both comfortable work posture as well as more manageable work loads.
Supset has its sights set hard on the future. “We could be getting even more out of the Fastems FPC once we would integrate more machine tools to it. This would allow us to utilize the production planning and resource management features of MMS even better. We’ve have been thinking of extending the system as it could feature up to two more machine tools in that way, explains Kolehmainen. “Having the two automated, parallel machines side by side would increase the flexibility of production. In addition, the tool resource management ensures the success of unmanned production and eases the work of our operators remarkably.”
An Outcome To Be Proud Of
The results of the investment at Supset goes to show that existing machine tools can be automated with excellent results. The needed automation should always be always chosen based on machine tool type and quantity. With this in mind, Fastems FPC is an easy and reliable solution suitable for 1-3 machining centers. When it comes to interfacing, Fastems’ library of over 90 integrated machine tool brand helps a lot, as well as good cooperation with machine tool builders. The long list of ready-made interfaces was the key to success while integrating Supset’s Matsuura as well. To conclude Kolehmainen recommends similar investments for other players in the industry: machining capacity has nearly doubled and the return on investment is estimated to fall somewhere between two to three years.