A Customized Automation System Has Made the SLB Facility in Béziers a World-Leading Part Manufacturer for Multiple Industries
In 2021, the SLB facility in Béziers, France, implemented a unique flexible manufacturing system (FMS) that integrates the entire production value chain. Thanks to a process-centric, rather than a product-centric, approach to manufacturing, the facility is now capable of developing complex technical parts for various industries at globally competitive prices.
The facility in Béziers builds on a century-old history, which began in 1920 in the railway industry. In 1958, the facility became a center of excellence for machining, welding, assembly, and testing of large equipment for oil and gas exploration. In 2016, the facility became part of SLB and is now one of their flagship manufacturing facilities.
With the energy transition, international competition and market fluctuations, the SLB facility in Béziers started to diversify its production and opened to new market areas in France and in Europe. In 2021 the facility was selected to host Genvia, a clean hydrogen technology company, as its pilot plant for manufacturing systems and modules for high temperature electrolyzers for decarbonized hydrogen. The same year, the facility was equipped with the Fastems flexible manufacturing system (FMS), enabling the facility to adopt new ways of working to achieve greater flexibility, efficiency, and innovation.
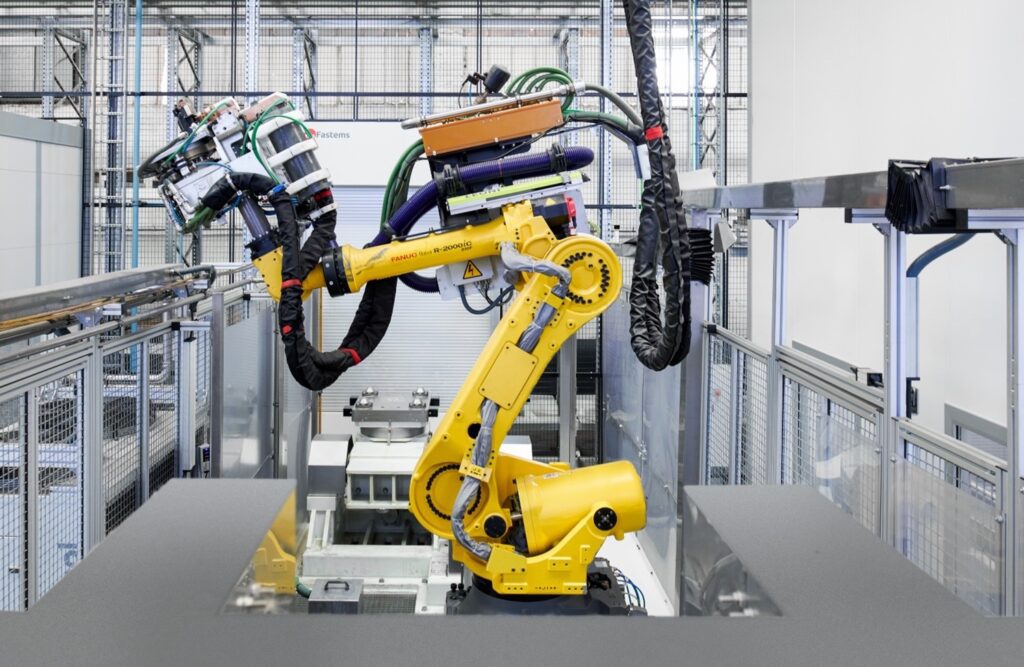
A Single FMS that Integrates the Entire Production Value Chain
Having become one of the city’s leading employers and a leading industrial player in France’s Occitanie region, the SLB facility in Béziers continues to evolve to meet the challenges of the energy transition, focusing on projects in decarbonized hydrogen and renewable energy. The FMS has been a real game changer.
To make the most of the FMS technology, SLB’s system at the facility in Béziers not only automates machining — it also integrates the entire production value chain, including heat treatment, dimensional control, and deburring. The FMS takes care of everything from raw materials to semi-finished products.
SLB Facility in Béziers Breaking Records in Lead Times, Efficiency, and Quality
“This strategic investment was part of the current movement for reindustrialization in many countries. When we decided to set up an FMS to reach our ambitions, we explained our particular needs to our automation partner Fastems, who listened carefully. We wanted to integrate the entire production value chain into our FMS, starting from raw materials and getting semi-finished products out. The system is not designed to manufacture a sole product; it includes the entire process, and it is extremely flexible even on a global scale. It gives us the possibility to manufacture a variety of complex technical parts for many different industries,” says Luc Mas, director of the SLB facility in Béziers.
The FMS at the facility in Béziers started operating in 2021, after seven months of design and installation work in close collaboration between the SLB and Fastems teams. In only three years, the facility has set a new standard among all Fastems installations in this sector, becoming one of its most productive and efficient flexible manufacturing facilities globally.
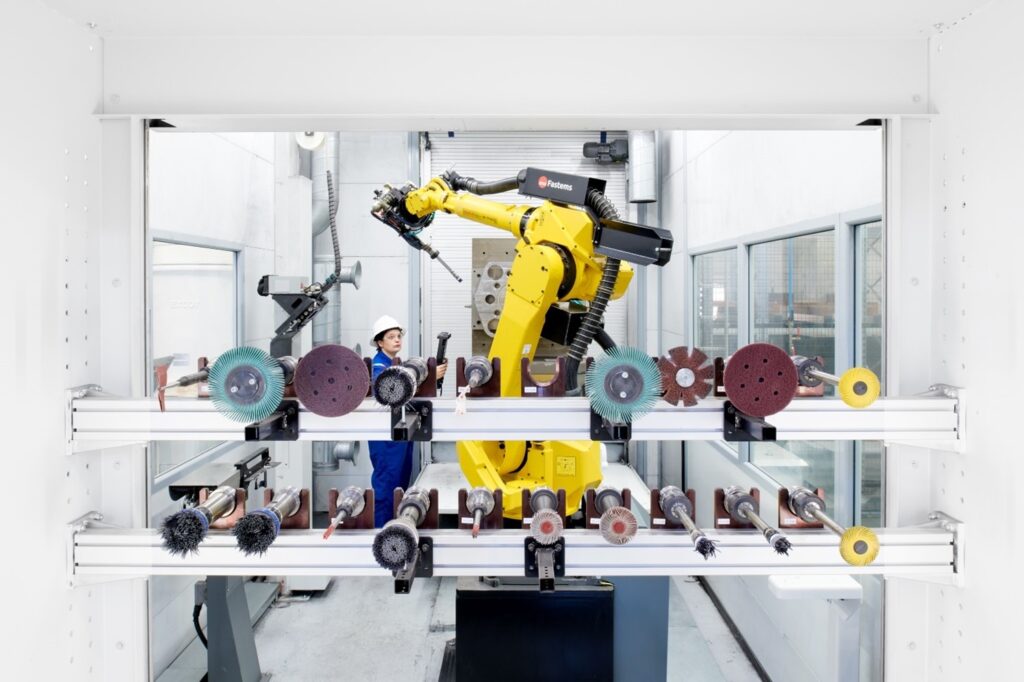
Having operated 24/7 from the moment it was commissioned, the FMS has several notable achievements. The facility has improved the production quality and shortened lead times by 70%. The high production flexibility also means that the facility can adapt in real time to demand changes. In addition, with spindle utilization rates above 90%, the FMS is efficient in terms of resources, unlocking three times higher production capacity per machining center.
“Thanks to the capabilities of our FMS line, the facility in Béziers has become extremely competitive. We are now even able to manufacture certain parts here in France that have been manufactured abroad until now. This has had a positive impact on local employment, with not only the creation of new qualified positions, but also increasing the skill levels of current jobs through training in automation processes and artificial intelligence,” Luc Mas says.
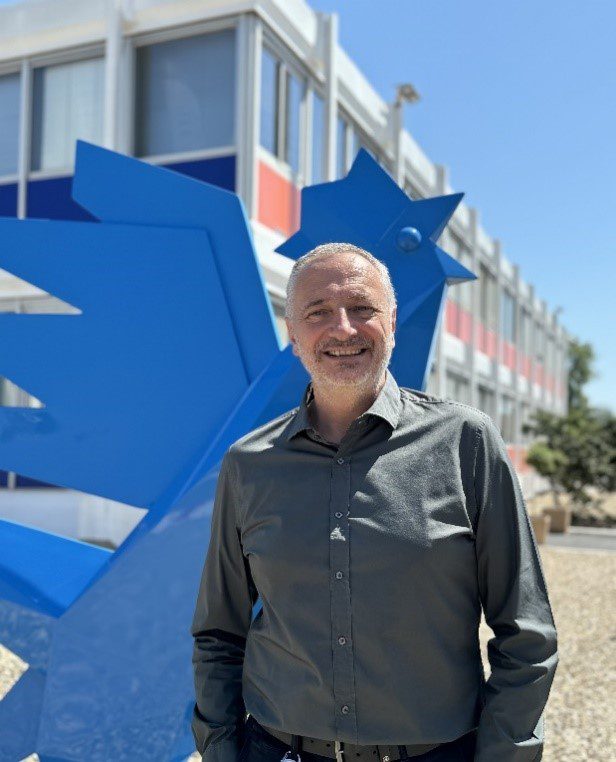
The System Sets New Standards as an Employer and Manufacturer
Ultimately, automated manufacturing transforms jobs of today and tomorrow to be more ergonomic and safer. This plays an important role in transforming the outdated image of the manufacturing industry, making it a more attractive industry for younger generations.
From a technological point of view, an essential asset of the FMS at the facility in Béziers is its capacity to take on new manufacturing work with reduced risks that are often associated with new production activity. Creating an economical multi-product manufacturing process is a significant competitive advantage that removes dependency of a single cyclical industrial sector.
“The FMS has set new standards in at the SLB facility in Béziers. With industrialization through digital manufacturing, we have become a major player in industrial revitalization on a regional, national, and global level. The modernization of our manufacturing has put us in the French Fab spotlight, and we obtained the “Vitrine Industrie du Futur” label in 2022. What a great recognition! This is really just the beginning of our FMS adventure…stay tuned for more to come!” Luc Mas concludes.
Technical information of SLB Béziers FMS:
- Five 5-axis machining centers
- 53 machining pallets and 33 material pallets
- Gantry Tool Storage (1,000 cutting tools)
- Robotized deburring and marking cell
- Induction hardening cell
- Coordinate measuring machine (CMM)
- Washing machine
- Connection to remote applications, shared data
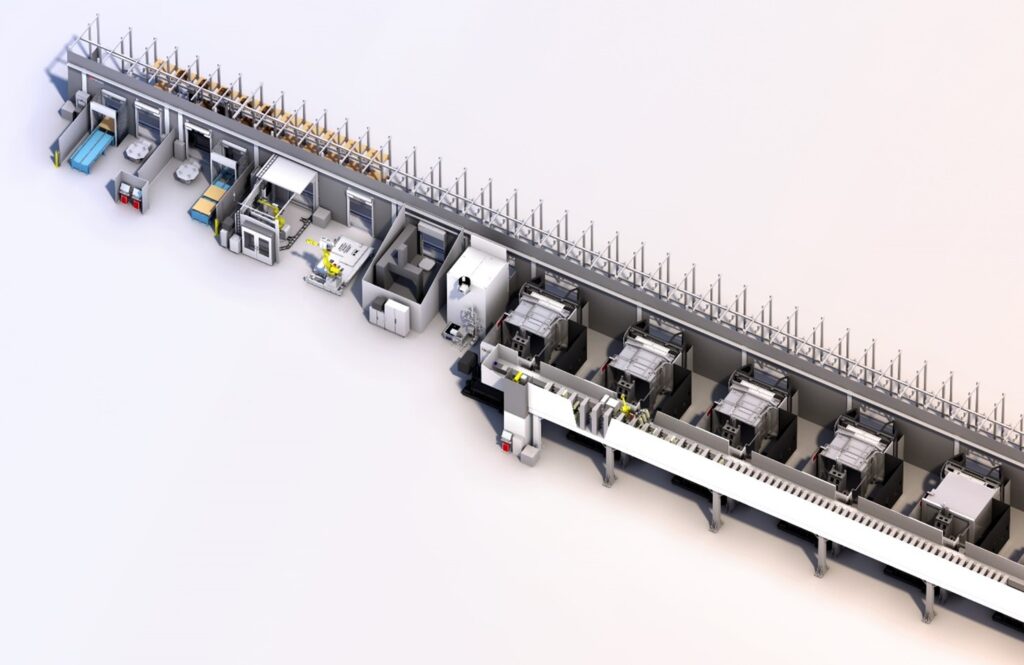