Flexible Automation in High-Performance Machining
Flexible and highly efficient machining in a small space: Kostwein chose Flexible Pallet Tower FPT from Fastems to automate their 5-axis machining center to run aluminum parts. Now they run a third shift unmanned, setup next jobs meanwhile the previous ones are being machined – and have full production transparency.
Austrian Kostwein is one of the largest contract manufacturers in Europe, employing around 1,400 people worldwide and having ten manufacturing sites in Austria, Croatia, Italy, India, and the USA. “We operate in build-to-print business, manufacturing complete custom machines and systems. Our customers can focus on developing their product innovations, while we take care of the implementation across the entire value chain. Our strengths lie in extensive know-how and diverse manufacturing capabilities for various industries,” explains the CEO Stefan Kostwein.
Space-Saving & Automated 5-Axis Machining
Kostwein has invested in automated production to offer extensive and efficient manufacturing capabilities for its customers, and to combat the shortage of skilled labor. In 2021, the company started their journey with Fastems by installing their first flexible manufacturing system (FMS) to automate machining operations and cutting tools for three DMG Mori 4-axis horizontal machining centers. In 2024, they got their second system, Flexible Pallet Tower FPT, installed in their Klagenfurt facility, automating a Grob G552 five-axis machining center.
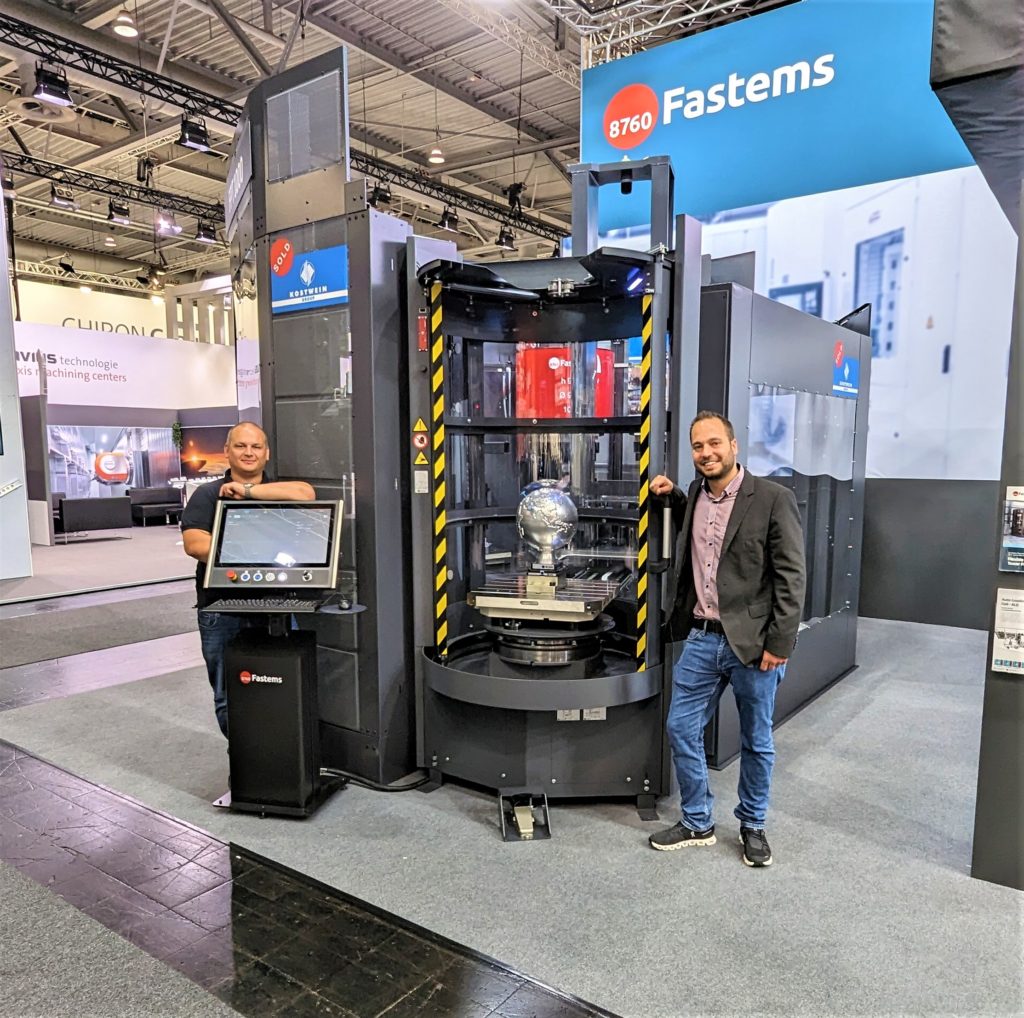
Thomas Baumann, Head of Maintenance Management at Kostwein, explains: “We chose this five-axis machine because we needed to machine aluminum tool molds and other parts more efficiently. Since we follow another manufacturing strategy with the other machining centers due to higher spindle and machining speeds, this machine is somewhat decoupled from the rest of the automated production. It was always clear to us that we needed to automate this machine in a way that would allow the maximum flexibility and productivity when running small batch sizes.”
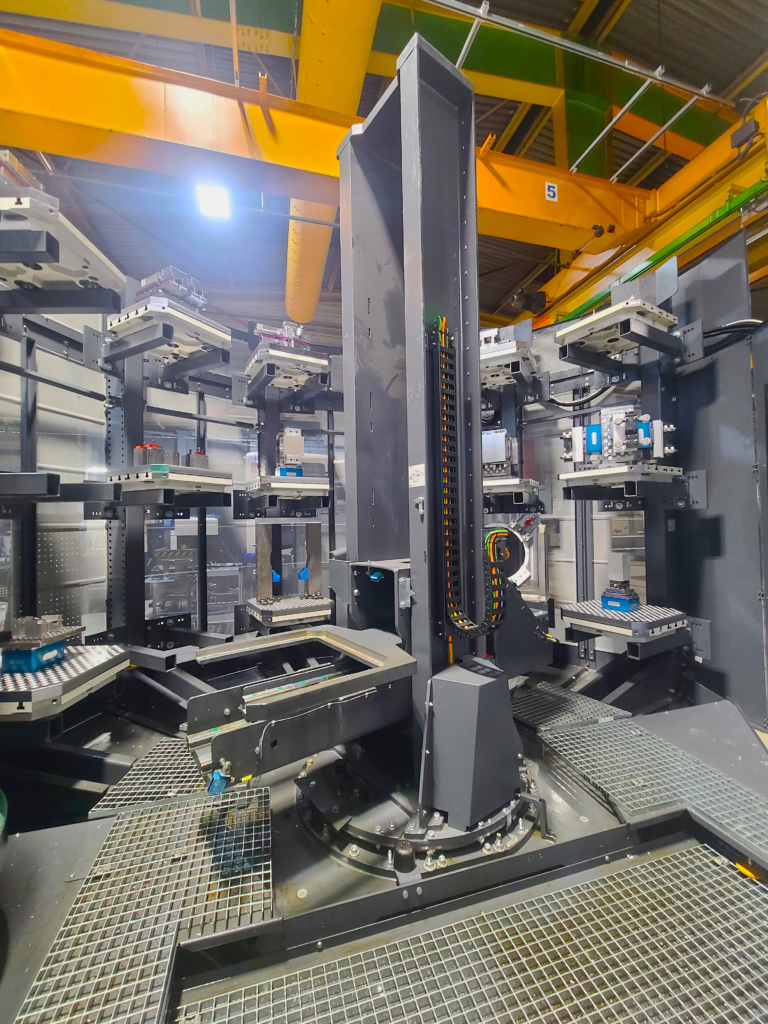
Maximizing Spindle Utilization Around the Clock
One of the key reasons for choosing the FPT-1000, according to Stefan Kostwein, was its large pallet storage capacity in a relatively small footprint.
Kostwein’s system features a total of 18 pallets (630 x 630 mm) on three levels with two different heights, optimized for the machine’s kinematics: 900 mm for 5-axis machining and 1200 mm for 4-axis machining of workpieces.
The machine is loaded directly from the pallet storage using a zero-point clamping system. Depending on the order, part size, and machining complexity, the number of workpieces per pallet vary between 1 and 8.
“Thanks to our clamping solutions, we are very flexible here,” says Stefan Kostwein.
Thanks to high pallet capacity of the FPT, the large 430-tool magazine of the Grob G552, and ability to setup next jobs meanwhile the machine runs previous parts, Kostwein can now run extended unmanned production shifts.
“We aim to keep the system running for a third, unmanned shift with our long-running tools. Additionally, we always load as many parts as possible onto each pallet to optimally utilize the spindle capacity during the day shifts. This isn’t easy since 20-30% of our production is new parts – every week,” says Stefan Kostwein.

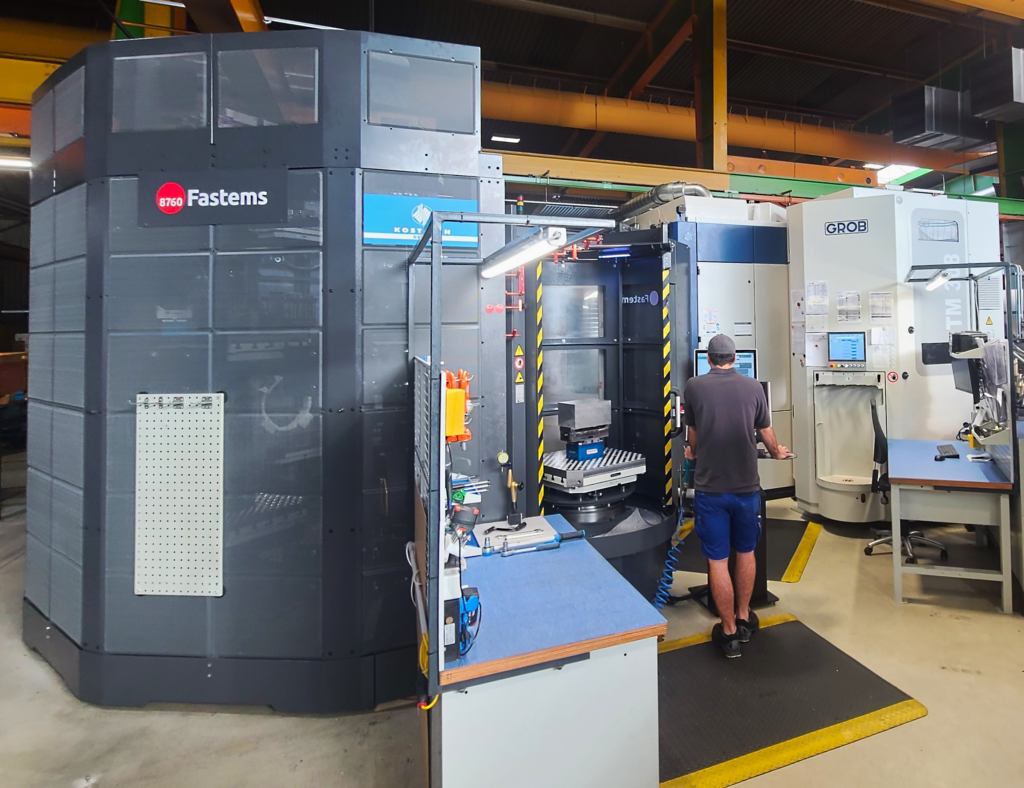
A New Way to Schedule Production
The production control of FPT is Fastems’ Manufacturing Management Software (MMS), which Thomas Baumann considers one of the key factors for their success.
Unlike conventional automation software that reacts passively to operator’s requests, MMS actively guides the operator throughout the production process. MMS schedules production 96 hours in advance and also takes care of manufacturing execution and monitoring. Before coming production jobs, MMS performs resource checks so it knows exactly which raw materials, NC programs, cutting tools and pallets are required and when. Additionally, it monitors tool wear times and informs the operator about missing resources in advance.
“The easiness of use has really convinced me – we only needed two days for training! Despite its capability to plan and run varying work, the system’s user interface is very logical and transparent, which helps avoiding many potential errors. MMS significantly eases our production planning, particularly enabling high manufacturing flexibility in high-mix-low-volume production. I haven’t seen anything like it before,” says Thomas Baumann.
An additional advantage of MMS, according to Stefan Kostwein, is its high compatibility with over 90 different machine brands. “With this automation software, our employees no longer need to learn and master various different software.”
“All in all, we made the right decision – our automated 5-axis manufacturing has met all the expectations!”