Up to 90% Spindle Utilization – Swiss Precision Manufacturer Automating Horizontal CNCs with a FMS
HÖGG AG Produktionstechnik, a contract manufacturer of high-precision parts automated two milling machining centers with a flexible manufacturing system (FMS) from Fastems. This testimonial describes how they fully exploited the potential of the system in a high time pressure – with rewarding results.
The HÖGG Group consists of HÖGG Liftsysteme AG, simplify engineering AG and HÖGG AG Produktionstechnik. The companies operate as independent companies with a total of 180 employees under the umbrella of HÖGG Holding AG. The core of the group is HÖGG AG Produktionstechnik, a contract manufacturer in Wattwil specializing in high-precision parts for wide range of industries. The company sees itself as a machining specialist with core competence in turning, milling, grinding and profile milling. They also specialize in the assembly of components and systems, as well as in profile manufacturing.
“With around 55 CNC machines and 105 employees – out of which around 85 work in production – we are an ideal partner for all customers looking for a contract manufacturer with high vertical integration level and wide range of machining capabilities,” says Stefan Kaufmann, Co-Managing Director and Production Manager at HÖGG AG Produktionstechnik.
Combating the Labor Shortage with Automation
Like almost all contract manufacturers in Switzerland, HÖGG AG Produktionstechnik is struggling to find and retain skilled workers. “This is a real challenge, because it is very difficult for us to find qualified employees who are also willing to work in shifts. And the situation has become even worse during the past five years. With the right range of parts, automation can allow us to offer more flexible working hours for our employees. In addition, we need to invest in new, more efficient machines,” says Kaufmann.
In 2019, HÖGG AG Produktionstechnik invested in a Starrag Heckert milling machining center HEC 500 for processing steel, and also planned to replace one existing machine in the same production area with a second HEC 500.
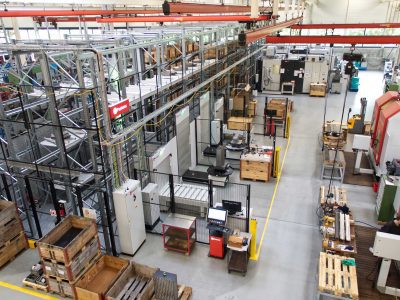
FMS from Fastems Plus Intelligent Control Software
To automate the two HEC 500s, HÖGG Produktionstechnik opted for an FMS from Fastems, with the option of adding another machine later to increase the production capacity even further.
With a length of 36 meters and a height of 6 meters, the FMS accommodates 68 machine pallets (500 x 500 mm and 500 x 630 mm), and 96 material pallets. For ergonomic and safe operation, the system has two pairs of material and loading stations where the raw materials and ready parts can be taken in or out – as well as the parts clamped to the machining pallets before each operation.
The FMS is controlled by the Manufacturing Management Software (MMS), which is one of the most powerful solutions for plan, run and monitor automated processes in machining production. Using the master data stored for various orders, MMS automatically plans production several days in advance, taking all necessary resources (e.g. NC programs, tools, raw materials, etc.) into account and informing operators what to prepare by when.
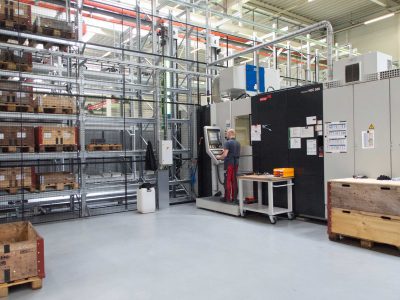
Machine Damage Requires Quick Response
The FMS was delivered in December 2022, and the first HEC 500 was prepared to be integrated into the system at the same time as it was being installed. But even with the best planning, things can and will sometimes turn out differently, as Stefan Kaufmann knows from experience: “At around the same time, our older existing machine had to be taken out of service due to a damage. Because the second HEC 500 was not yet available, we could only fall back on the HEC 500 that was already part of the FMS, for future orders. We therefore took the system into use on the day one.”
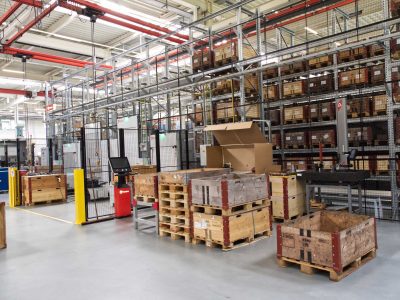
Dynamic Job Routing Increased Efficiency
When automating with an FMS from Fastems, there is a choice between static (EasyRoute) and dynamic routing of the pallets in the system.
“In order to fully exploit the potential of the FMS right from the start, we opted for dynamic routing, even though we were under a lot of time pressure,” reports Mathias Schnyder, Head of CNC Steel 2, and specifies:
“While static job routing specifies a certain sequence for processing the pallets with previously assigned machines, dynamic routing enables far more flexible planning and control of production since it truly optimizes all the capacity to be maximally used. Among other things, this leads to better transparency to the items in the system, higher machine utilization, and significantly reduced set-up times for repeat orders. Added to this is a wealth of valuable production data.”
Over 300 NC Programs Implemented in a Short Time
A crucial prerequisite for automated production is that the production process of each part is stored as master data in the MMS. The master data means the NC programs, tools, raw materials, fixtures, article numbers, drawing numbers, order numbers, etc. required to manufacture the part. “This initially involves a certain amount of time, but it becomes less time-consuming as the database increases because, for example, once fixtures have been stored in the MMS, they can simply be selected for another order,” explains Mathias Schnyder.
Within a very short time, around 330 NC programs from the older existing machine were run in and transferred to the MMS master data with appropriate adjustments. It is a remarkable achievement that has continued – the number today is around 400 programs, some of them for multi-sided machining. “During this period, we have already been able to produce around 150 to 200 different jobs with the FMS, especially as the second HEC 500 has also been integrated in the meantime,” says Schnyder.
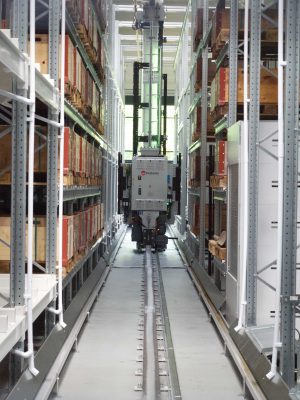
Set-up Times Reduced by Up to 85 Percent
Stefan Kaufmann and Mathias Schnyder are very satisfied with the progress of the project so far in the view of the achieved results. “We have a 60 to 70 percent share of repeat orders, and we have been able to reduce set-up times by up to 85 percent. This is particularly noticeable within specific part families, for which we leave a certain number of pallets with fixtures in the system until the production order comes again, and we only have to clamp the workpieces. The set-up times for the machines are completely eliminated here. The dynamic routing also offers us significantly more flexibility, as we can now run a number of orders with either machine and process a mix of material – currently steel, stainless steel and aluminum,” emphasizes Stefan Kaufmann.
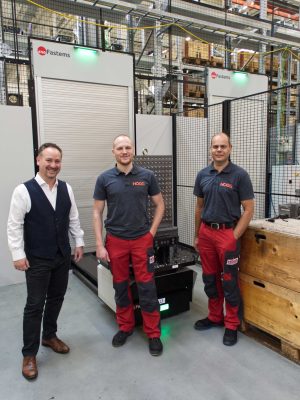
Valuable Data, Targeted Optimizations and Higher Transparency
For Mathias Schnyder, the data supplied by the MMS of the ongoing production is also highly interesting:
“For example, we have already been able to make targeted optimizations to tool service life based on the data, because we can now see exactly which tools are used the most often and are therefore subject to greater wear.
Overall, the production is now much more transparent because we have valid data available, for example on machine running times, on machine tool utilization and on the use of devices, to name just a few examples. All information is valuable and makes it easier for us to calculate orders.”
Machine Utilization of Up to 90 Percent per Day
The FMS currently produces in two manned shifts. Some specific orders can also be processed in an unmanned third shift. “This is not yet happening across the board. But we are taking every opportunity,” says Stefan Kaufmann, drawing a positive conclusion:
“It should be noted that we are still in the ramp-up phase, but are already achieving significant benefits, as can be seen from the set-up times, among other things. The investment has definitely paid off, and the FMS is a real asset in our production – we have already had days with 80 to 90 percent machine utilization rate. We are currently expecting around 160 production hours per week for both machines, although we are continuing to consistently expand the production spectrum for the FMS.”
“We are currently expecting around 160 production hours per week for both machines, although we are continuing to consistently expand the production spectrum for the FMS.”