Investing In Technology
Since its founding, Hirsh Precision Products has continually invested in advanced manufacturing technology. “We try to understand what the return is on certain new functions or features and be sure to take advantage of those innovations in a smart way,” said Chief Operating Officer Peter Doyle.
Today the company has 22 CNC machine tools, distributed nearly evenly between mills and lathes. There are six production cells with three or four machines per cell. Five-axis machines are prominent, used largely for positioning that enables one-and-done machining. Positioning accuracy is critical in medical manufacturing for maintaining part registration, tolerances, and interrelationship of features. The shop makes parts ranging in size from 1mm turned components up to items as large as three feet, but “80 percent of our work will fit in the palm of your hand,” said Steven Hirsh, founderand Director of Engineering for the company.
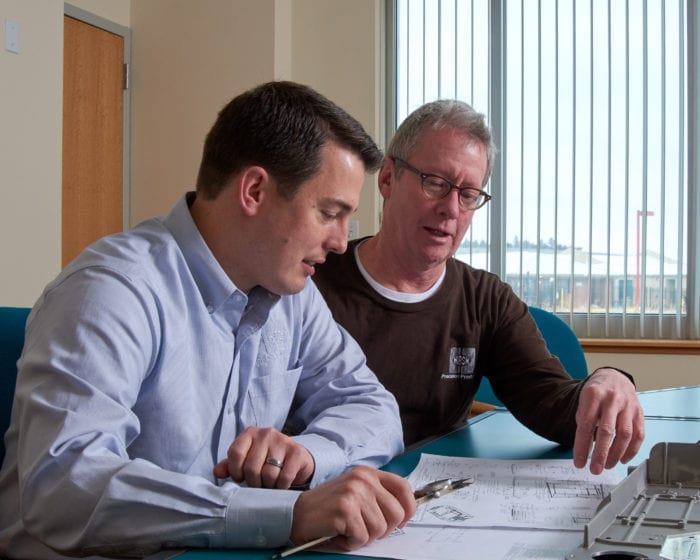
Hirsh Precision Products Chief Operating Officer Peter Doyle (left) and Director of Engineering Steve Hirsh discuss a new customer’s application.
Evolution of Automation
Hirsh Precision Products has always sought ways to automate its processes. Seeking to expand its application of FMS strategies, the company investigated options available in multi-machine FMS systems. “We go to IMTS every two years as a team to stay abreast of technology relevant to our customers and their parts,” Hirsh said. After thorough pre-show research, at IMTS 2016 the company purchased an FMS system consisting of an Okuma MU-4000 trunnion-style 5-axis CNC vertical machining center, featuring a 740 mm x 460 mm x 460 mm X-Y-Z work envelope, served by a model MDR-750 FMS ONE manufacturing system from FMS provider Fastems LLC.
The shop has since acquired and installed a second MU-4000 mill on the Fastems system, which has thirty-six 400 mm diameter pallets, three levels of pallet storage and one LSC loading station. The system is expandable to handle five machine tools and 120 pallets.
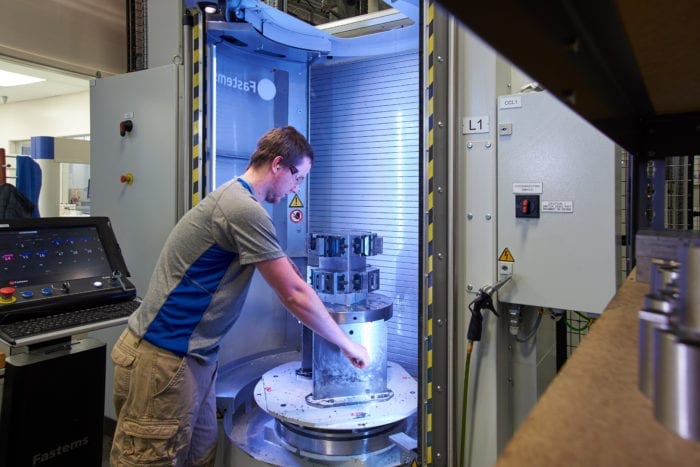
Hirsh Precision Products team member Sawyer Hayes secures pallet in the loading station of the shop’s MDR-750 FMS ONE manufacturing system from FMS provider Fastems LLC.
Fastems Manufacturing Management Software (MMS) is the operational foundation of the system. MMS makes production prioritization decisions based on the availability of personnel, tools, machine time and raw material. It devises a schedule, moves pallets to and from the pallet racks, and directs machining of parts autonomously. “We communicate the due date and the quantity required,” Doyle said, “then MMS can ‘play chess’, look at the work that’s scheduled and come up with a plan that will meet the delivery dates, take advantage of the resources available, and maximize spindle time. That’s led to excellent spindle utilization.” The shop inputs its personnel schedules and the system retrieves finished parts when team members are available to unload them. “Operating Fastems highlighted for our team the importance of keeping the spindles running. Our job is organizing any required prerequisites, such as fixturing,” Doyle said.
“We communicate the due date and the quantity required, then MMS can ‘play chess’.”
The multiple pallet system is a good match with the repetitive nature of most Hirsh parts. “Set-ups are one of the bigger variables for us,” Hirsh said. The shop can practically eliminate setup times by leaving fixturing intact on the pallets. “With 36 pallets, we can leave jobs set up. Changing pallets allows us to minimize lead times while maximizing utilization,” Hirsh said. In a study the shop performed on three typical part-making processes, setup hours showed reductions of 72 percent, 54 percent, and 92 percent with an average reduction of 73 percent.
Perhaps most importantly for the shop, the FMS system enables lights-out operation on nights, weekends and holidays. “The goal is running the spindles 24 hours a day,” Hirsh said. Palletized work fixturing also permits increased part density. “That aids us in lights-out production,” Doyle said. “Working with a five-minute cycle, 36 pallets wouldn’t last very long. But if you have one hour or two-hour cycles then you can make it through nights and weekends. The Fastems system allows full utilization of unattended time. Instead of having somebody there every 15 minutes, we can let the system go off and run overnight and we change the parts out the next day.”
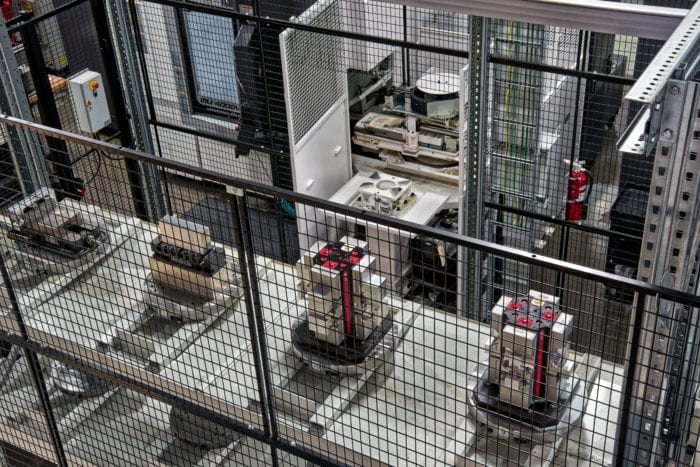
At Hirsh Precision Products, pallets preloaded with fixtures and parts await transfer via the Fastems MDR-750 FMS ONE manufacturing system to one of two Okuma MU-4000 5-axis CNC vertical machining centers.
Doyle said, “What I like about Fastems’ FMS is that it enables our team to focus on solving problems that technology can’t solve, while it frees the team from tasks that the technology’s proving to be very good at. For example, the Fastems system is great at repetitive actions and its ability to prioritize work and keep the spindle running is fantastic. But it is not going to be able to tell us how to design a fixture, how to think about material properties or how best to design a production process. So it allows us to focus on the areas which are a sweet spot for our company.”
Balancing High Tech with High Reliability
When researching different FMS systems, Hirsh looked for durability and reliable performance rather than leading edge, early-adopter technology. “We wanted to balance investment in latest technology with wanting something that has been well-tested and not a liability,” Hirsh said. “Fastems is the right choice for us. It’s a strategic investment for us that we expect to fit our business for many years to come.”
This is a shortened version of the full text that was originally published in Manufacturing Engineering – August 2018 Issue. Read the full story here.
Editor-in-Chief: Alan Rooks
Media Contact: Lynn Gorman
"*" indicates required fields