Emerson’s Productivity Skyrocketed After CNC Automation Take-Off
Emerson Professional Tools AG automated horizontal 4-axis machining to manufacture high mix of press jaws and rings for tools more efficiently. Today, they have an unmanned night and weekend shifts – and up to 95% spindle utilization.
Emerson Professional Tools AG in Sissach, Switzerland, is part of the global Emerson Group which employs around 85,000 people and specializes in process automation solutions for example to chemical plants and refineries. “We are part of the Productivity and Safety division and belong to Professional Tools Europe, with various locations in Germany, Belgium, Slovakia, and Romania. As a Center of Excellence in Machining, we manufacture components for professional pressing tools for sanitary and electrical sectors, with around 65 employees at our site,” explains Stefan Rüdisühli, Managing Director of Emerson Professional Tools.
Lacking Production Resilience and Efficiency
Emerson had experience of simple CNC automation systems already, but those solutions lacked flexibility. First of all, there was no production resilience: for example in a machine failure situation, moving production to another system was not possible. Second, the systems were not designed for lights-out production, meaning that unmanned shifts were not possible. Third, the different systems were all separate instances without any connectivity to each other. As Erik Liebscher, Advanced Manufacturing Engineer for all structural and investment projects at Emerson Professional Tools manufacturing explains: “With the Swiss franc being strong, and at the same time having a shortage of skilled workers in the market, automation is essential for us to remain competitive in Switzerland. Before automating, our production processes were not stable enough to allow a single worker to oversee multiple machines. Each machine basically needed its own operator at all times.”
Selecting Machining Technology and Automation to Achieve the Manufacturing Vision
A few years ago, Stefan Rüdisühli and Erik Liebscher approached Gennaro Teta, Fastems’ Sales Manager in Switzerland, considering how to stabilize manufacturing processes and at the same time increase production flexibility and efficiency.
“Mr. Teta helped us to explore our options by showcasing us several automated sites and giving us detailed understanding of Fastems solutions – aligning everything with our own manufacturing vision,” says the Managing Director. After investigation, Emerson chose to replace several older machine tools with Starrag-Heckert H50 horizontal milling machine and Fastems Flexible Pallet Container (FPC). “The machine tool we needed to produce press jaws and rings for our professional tools was available on short notice, so we wanted to invest in an automation system that could be implemented quickly and is proven to work seamlessly with the machine,” explains Erik Liebscher.
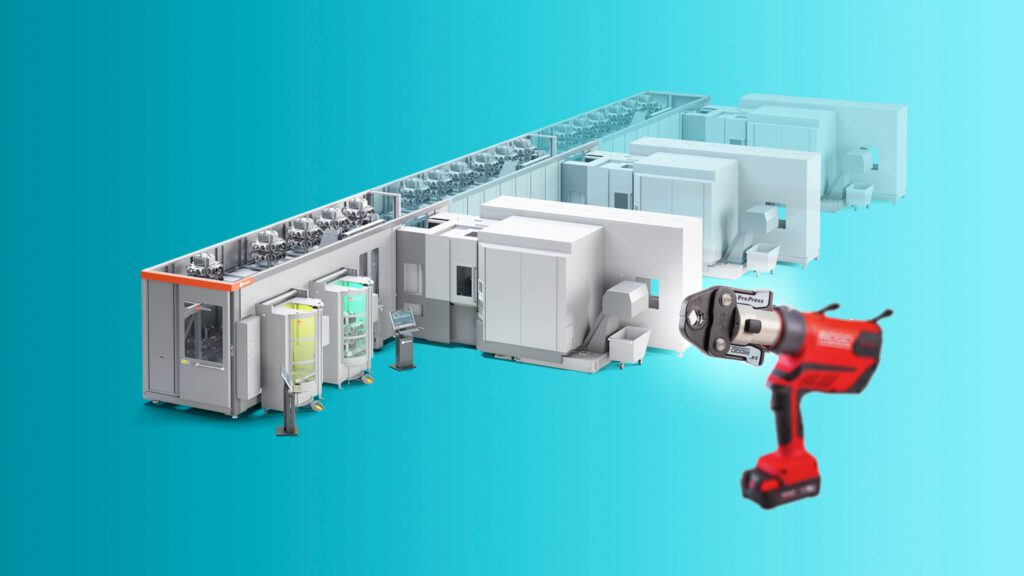
FPC is a standardized and cost-efficient flexible manufacturing system (FMS), designed for high-mix production. As a factory-assembled system and a wide library of ready machine interfaces, FPC is fast to deliver and ramp up. And like all Fastems FMSs, also FPC can be extended to automate up to three machine tools.
Emerson chose the highest expansion level of the FPC that can integrate three machine tools and 30 machine pallets. The first machine was connected in 2022 – Stefan Rüdisühli explains the automation implementation strategy: “We started with a single machine and 10 pallets to properly develop the process, and gradually scaled the system after ensuring everything from the individual interfaces to part master data creation worked seamlessly. Adding the extra machines was then just a plug-and-play!”
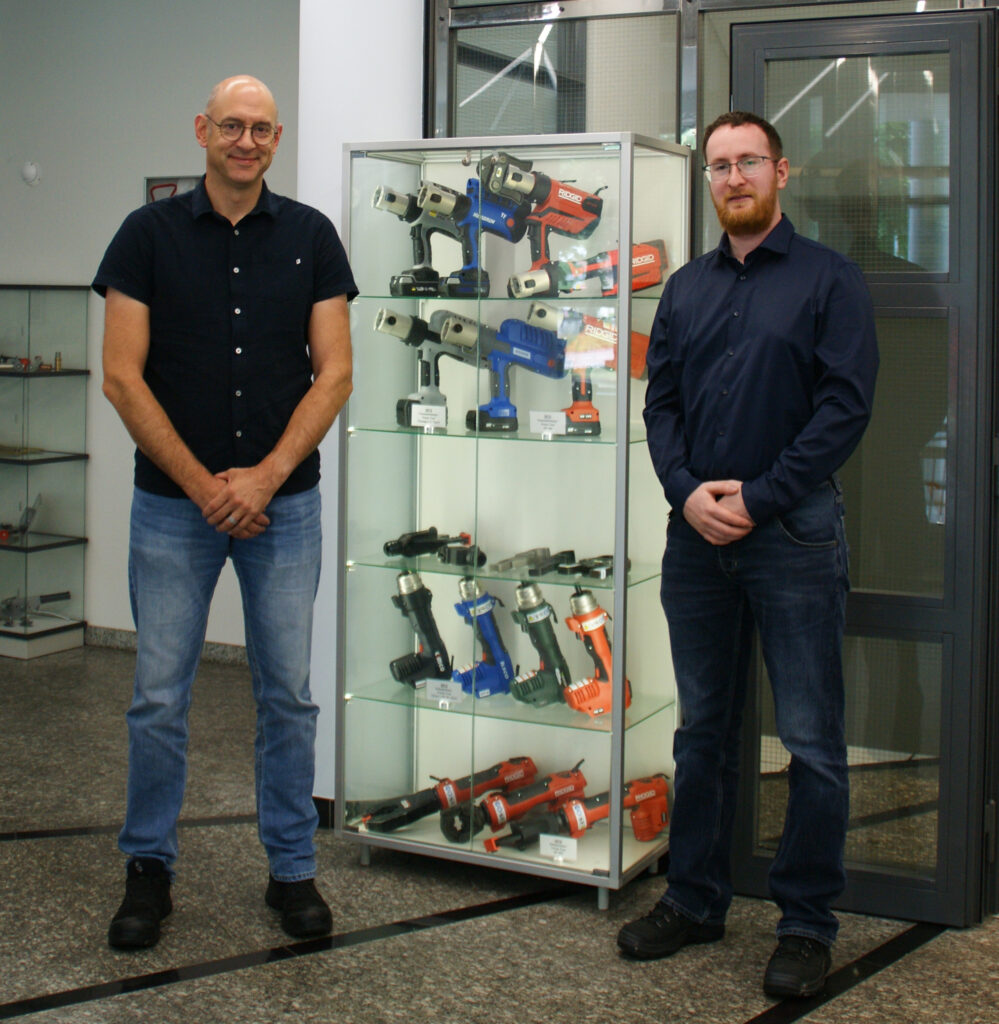
Continuous Production Without Downtime
The clamping towers on the machine pallets hold various blanks from which different jaws or rings can be manufactured. This allows for highly flexible production of a diverse part mix – even though some of the clamping devices are workpiece-specific. Depending on the product and quantity, machining times per fixture range from three to ten hours. “Realistically, with our product mix, we can currently run from 15 to 30 hours unmanned,” says Stefan Rüdisühli.
“Working on two day shifts for 16 hours plus eight hours unmanned, we’ve already achieved 72 consecutive hours of production with the three machines. And on several occasions, we’ve reached a capacity utilization rate of 95%! We can literally see our productivity skyrocketing.”
Also, the parallel integration of new workpieces increases productivity. “While one machine is being set up for a new part, the other two continue production normally. Once the part introduction is completed, the machine is immediately ready to operate again, ensuring high flexibility and productivity without downtime. Also loading and unloading parts from the pallets is done outside the machine tool – ensuring there are no machine stops due to setups. Even in an automated system, this level of efficiency cannot typically be achieved in terms of setup and non-productive times.”
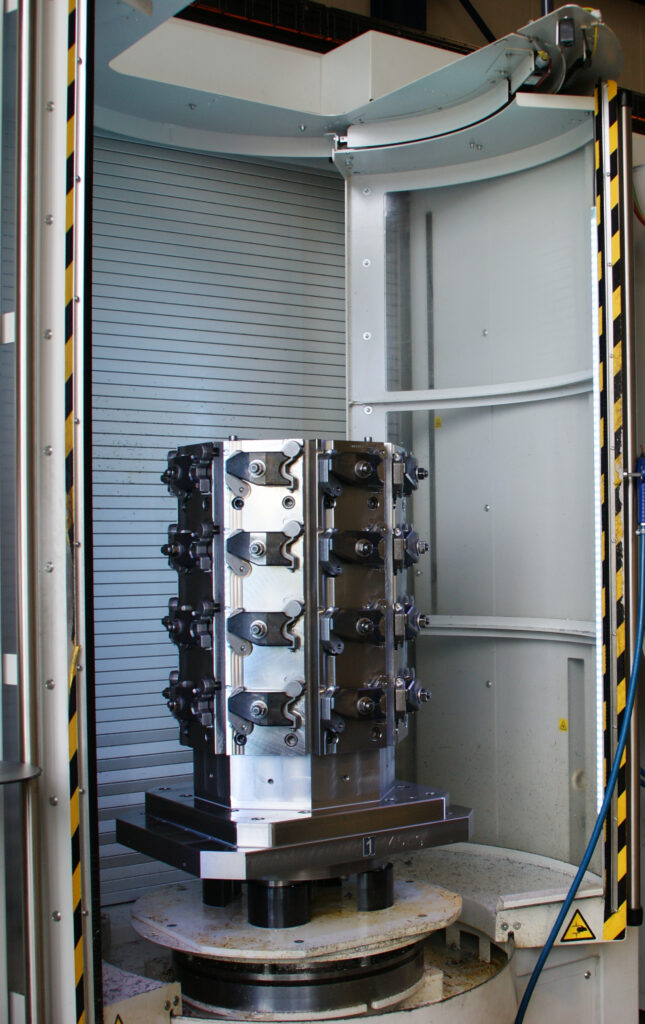
Automated Production Scheduling with MMS
The automated production at Emerson Professional Tools is planned, controlled, and monitored using Fastems’ Manufacturing Management Software (MMS). MMS is the production control of all Fastems systems, taking care of NC program management, tool management (including tool life monitoring), and resource checks for planned production, such as raw materials, fixtures, tools, and NC programs. Erik Liebscher notes that these features enhance the system flexibility: “We use the MMS fine scheduling, which gives us full production visibility up to 96 hours in advance. Because the master data for recurring parts is already entered in MMS, we simply input the planned orders and quantities. MMS then determines which machine will take care of each order.”
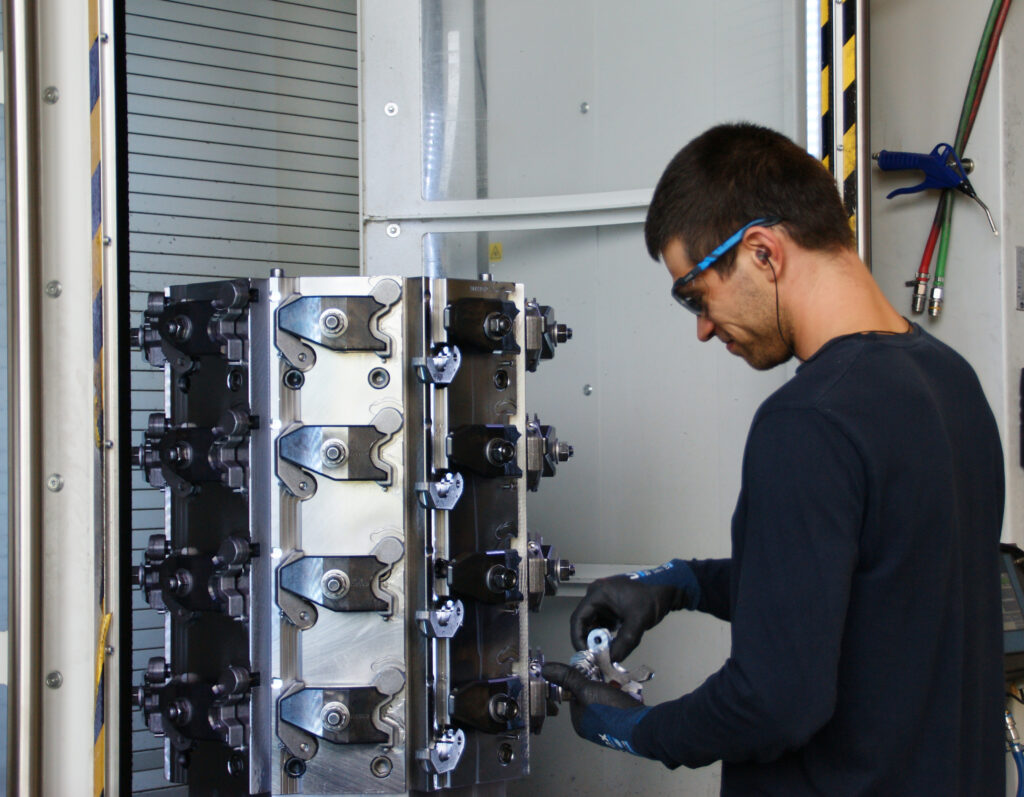
Ongoing Transition to FPC
With FPC, the operator effort is minimal. During the day shift, a skilled worker can monitor the process, clamp new workpieces into towers, and manage stand-alone machines at the same time. Once the system is fully loaded, Emerson Professional Tools can manufacture unmanned almost throughout the weekends. “We currently have 20 pallets in the system, and we are steadily moving more production into FPC. This ongoing process is significantly boosting our productivity,” says Stefan Rüdisühli, who has been very pleased with the automation results so far. “For example, working on two day shifts for 16 hours plus eight hours unmanned, we’ve already achieved 72 consecutive hours of production with the three machines. And on several occasions, we’ve reached a capacity utilization rate of 95%! We can literally see our productivity skyrocketing.”
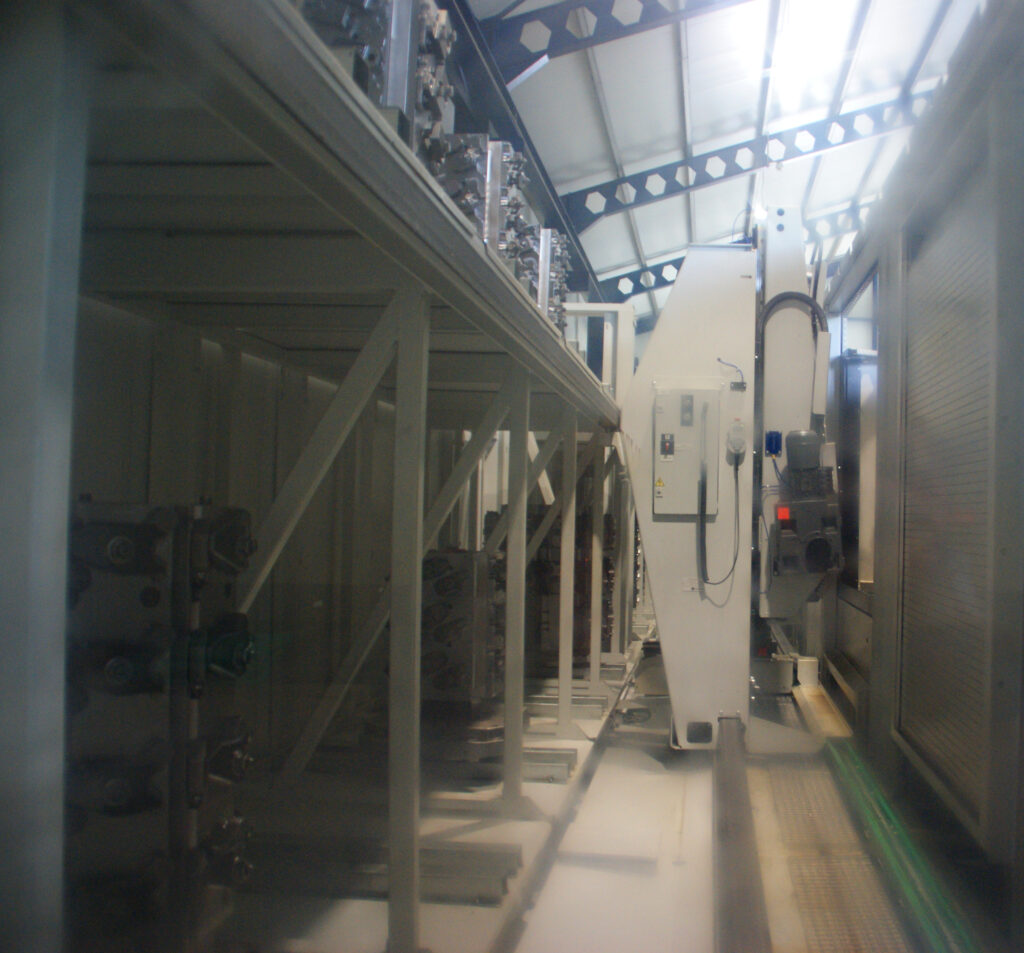