Avant Tecno Doubled Production Capacity by Automating a Horizontal Machining Center
Avant Tecno, the world-leading manufacturer of multi-functional loaders, decided to invest in an automated 4-axis horizontal machining center to answer the increasing demand and to manufacture higher part variety in-house.
The Finnish loader manufacturer Avant Tecno started as a small family business in 1991 and is today a global technology leader with over 80,000 loaders delivered for customers in various industries like landscaping, construction, agriculture, property maintenance and farming. “We have grown a lot, and we are under a process to double our manufacturing capacity during a five-year period. Every Avant is made-to-order for the customer’s unique needs from hundreds of available modules. Therefore, a traditional line production would not work for us – we want to be both efficient and flexible to meet and even exceed our customers’ expectations,” explains Saku Vastamäki, Vice President of Production at Avant Tecno.
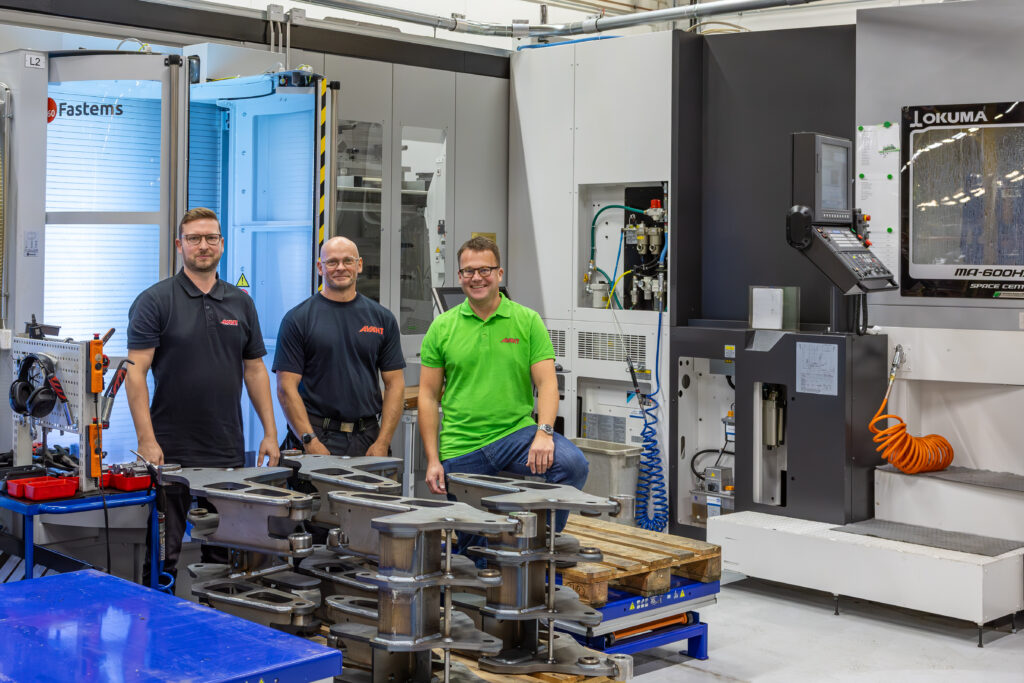
The New 4-Axis Machining Center Runs Any Part with Single Clamping
The machining department of Avant Tecno manufactures components for bodies and boom lifts for the different loader series. When the capacity of the old 3-axis vertical machine tool reached its limits, the company started investigating the possibilities of 4-axis machining where they could not only manufacture parts with a single clamping but also run their whole part mix in-house to reduce subcontracting. “The project started by considering our manufacturing mix and selecting a machining center that had the right size class, high efficiency, and precision level,” tells Mikko Ojanperä, Production Development Engineer of Avant Tecno.
After investigating their options, Avant Tecno selected a 4-axis horizontal OKUMA MA-600 HII from the Finnish dealer company MTC Flextek. “Compared to our old 3-axis vertical machine tool, we have already been able to reduce cutting times by 15 % and can probably still get a bit more out of them”, says Ojanperä.
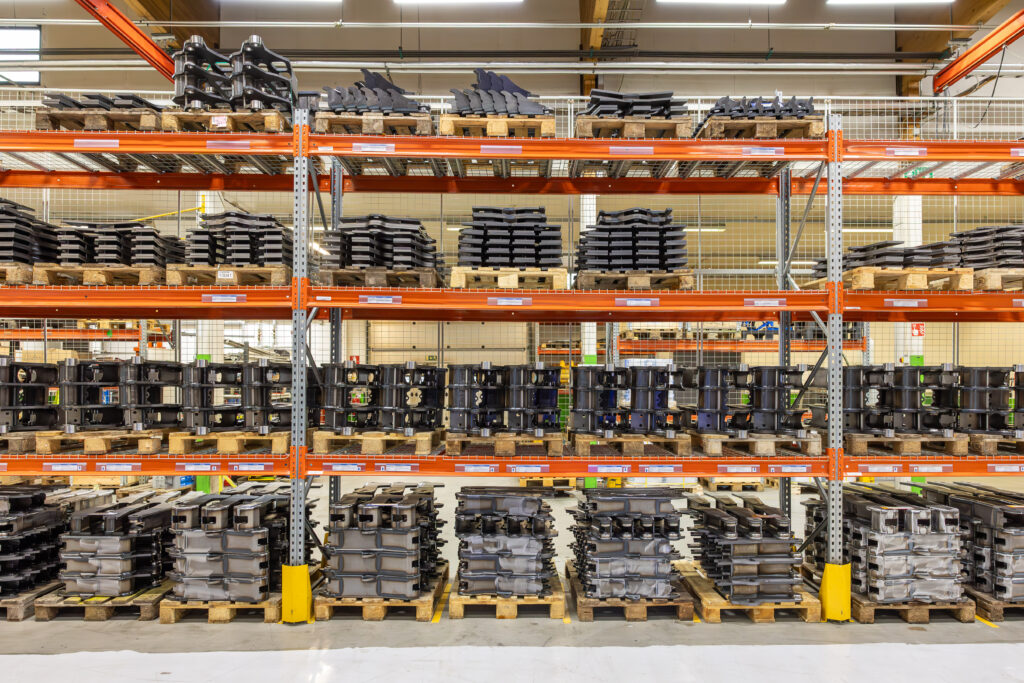
Automation Cuts Down Setup Times and Enables Unmanned Machining
The next step for Avant Tecno was to ensure they can keep the powerful machine tool running at maximum spindle utilization. This means enabling unmanned machining and making sure the machining setups are as quick as possible. With these goals in mind, Avant Tecno started discussing with Fastems about automating high-mix machining – and ended up investing in Flexible Pallet Container (FPC). FPC is a compact flexible manufacturing system (FMS), and it is specifically designed to run a high mix of parts efficiently, precisely, and with low unit cost.
“Previously, we needed to change fixtures manually between every batch, which took 15 to 20 minutes – three or four times a day. In addition, the NC program needed to be uploaded and adjusted – not to mention the cutting tool preparations! Since the setup was to be made on the machine table, the machine always stopped during setups,” describes Jani Pihlajamäki, the Lead Machinist at Avant Tecno. “In the FPC’s pallet storage, we have a permanent fixture for each part, and we can clamp workpieces into those fixtures in the automation system’s loading station. The machine tool stops now only for seconds to change jobs, and if we load all our 12 pallets full, we can run an entire shift unmanned.”
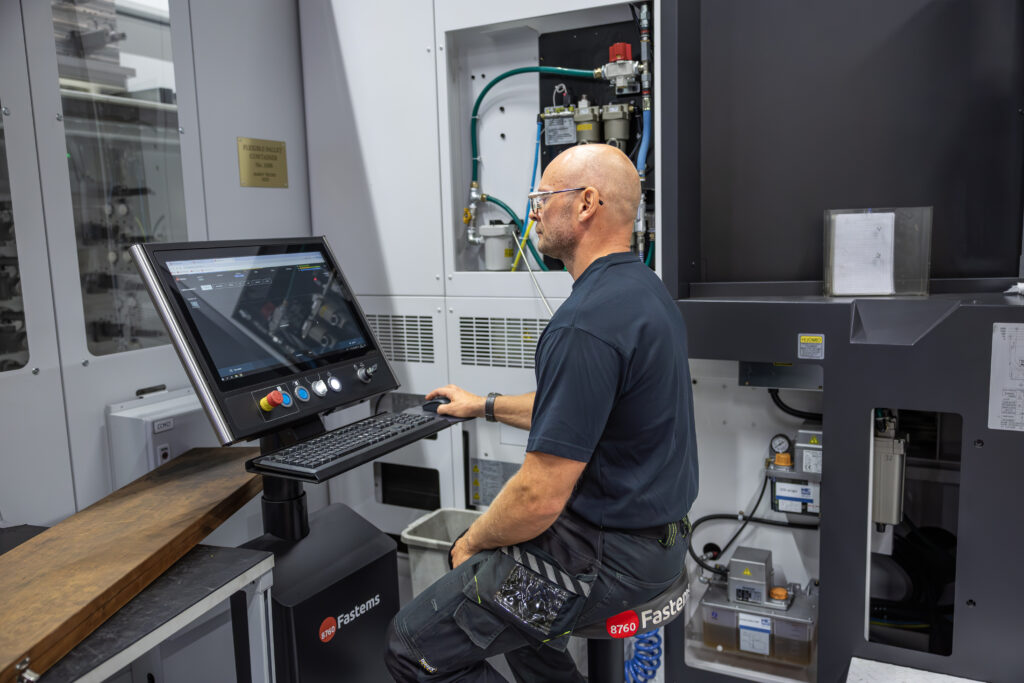
Production Started Straight Away in the System Training
“We literally pressed production ’play’ in the end of Fastems system training,” smile all the gentlemen Vastamäki, Ojanperä and Pihlajamäki. As a factory-tested and assembled automation unit with ready machine tool interfaces, FPC is technically fast to install. However, automation is not just about installing a system – it is a way of manufacturing that requires change from the team as well.
“Avant Tecno’s team did an extraordinary job when preparing for automated machining. As effortless as we try to make the ramp-up process for our customers, it does require work to turn the processes automation-ready: the tested NC programs, enough cutting tools, fixture design and build, indoor logistics around the system,” lists Matti Nenonen, Fastems Sales Manager in Finland. “Avant Tecno committed to the process and started to prepare for automation in advance. When our training specialist arrived, Avant Tecno had everything ready so that they could practice the system use with the real parts. That allowed us to really help them to find the best automation practices for their unique needs.”
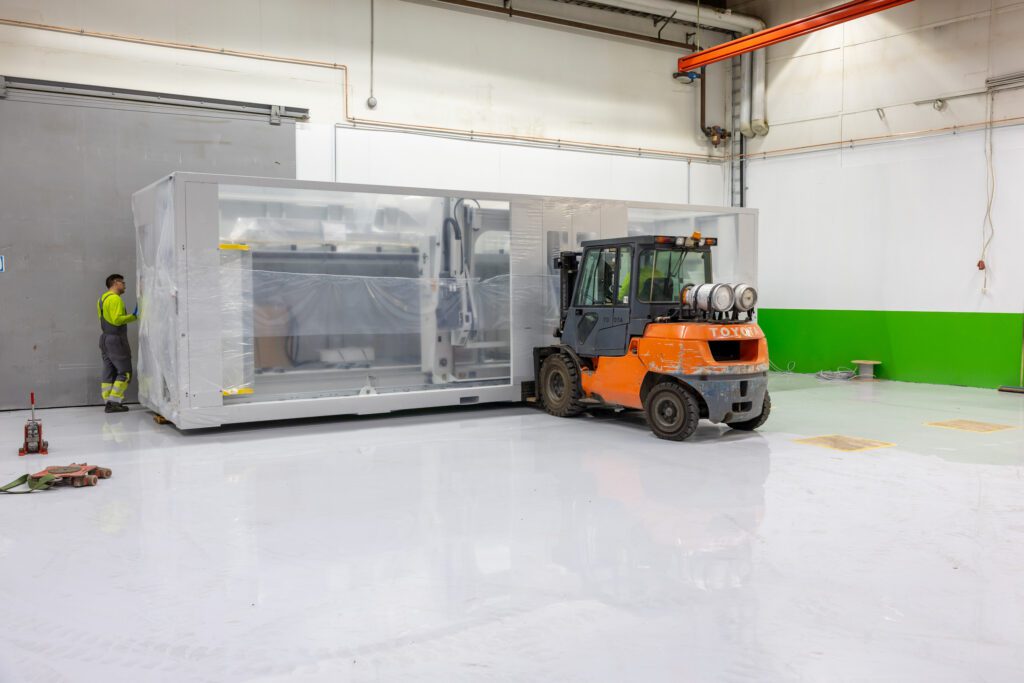
Peace of Mind with 24/7 Service and myFastems
“In manufacturing, you need not only reliable equipment but also reliable service. For us, this was one crucial factor when selecting automation partner,” tells Ojanperä, and Pihlajamäki continues: “Fastems has a 24/7 service that can solve most of the issues remotely straight away – and the onsite service is only 30 minutes away from us. We have been very satisfied with the service – we have had a couple of system errors, and those were fixed extremely fast.”
“Also, one thing we appreciate is the customer service platform myFastems. We can easily see the system service history, service reports on what has been done and what is recommended to do in future, as well as order service in one click. Best of all, we would receive automated alerts in case our system stopped during lights-out machining – so we really have peace of mind even when we are not onsite ourselves,” says Ojanperä.
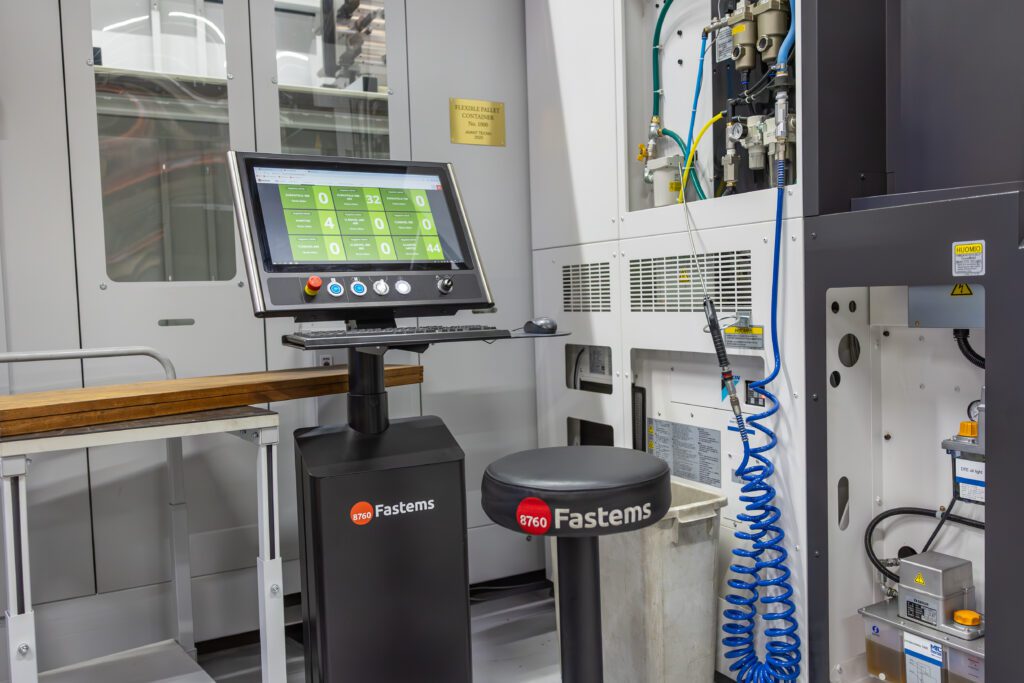
Future: Possibility to Add a Second Machine Tool in the System
When asked about future plans, Vastamäki smiles and tells they aim to grow and are prepared for growth. “We can extend our FPC with another machine and 12 more pallet places – and double our production capacity again when we need to. For our team that will not be a huge change because we can continue operating in the exact same area and the exact same way. The job planning for two machines is not going to be a problem because MMS will do it for us, automatically.”
“It has been exciting to work together with Fastems as another high-technology company in the area. Our team has been extremely glad of how their work has improved – so much that even getting back to work after summer vacations was much easier this year to what I heard,” laughs Ojanperä.
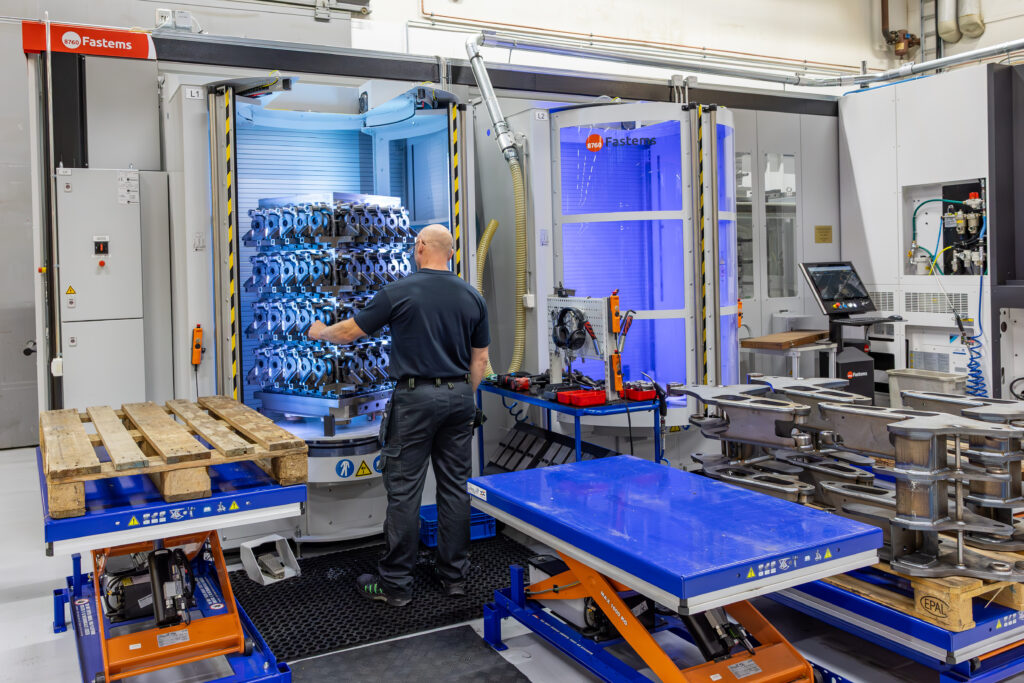
Five Tips to Prepare for Automation by Avant Tecno and Fastems
- Fixture design and purchasing. Fixturing is not where you should save in when it comes to automated machining! Design fixtures so that you can utilize your machining envelope well and optimize cycle times. If your parts have short cycle times, place many of them on the same pallet – and remember that you can also place many different parts on a pallet. Aim to have your fixtures ready by your system commissioning to ensure your automation provider can train your team to use the system with your actual production parts.
- NC programming. If you know what you manufacture (even partly), pre-program parts already before your machine tool arrives. In this project, Avant Tecno utilized OKUMA IGF to program parts beforehand – allowing a jump start to machining real parts right after the installation.
- Cutting tools and tool data. Ensure you have large enough tool magazine to run your part mix – also lights-out. Prepare your tool set in advance, and ensure you have sisters for those tools that are needed often or have short lives. Use a tool library that allows the system to call certain tool IDs, not certain tool pots – this allows efficient use of sister tools.
- Practice automation system use beforehand. Utilize the digital version of the automation control software and have your team learn the basic logic and features already before your system gets installed. This helps you to understand how each part is handled in the system, what to prepare for and which questions to ask from your automation trainer.
- Utilize knowledge of your automation partner. No one knows machining automation better than your automation partner who has helped other manufacturers to ramp-up automation thousands of times. Expect and let your partner guide you, and do not hesitate to ask for help. The sooner you learn the best automation practices for your company, the faster is your system pay-off!