FMS for Low-Volume, High-Mix Shop Provides Stable, Predictable Process
What’s in a name? In some cases, a lot. “It’s in our DNA to live by our name,” said Scott Shortess, CEO of Advanced Machining & Fabricating and Advanced Plastics in Owasso, Okla. However, they are known simply by the name “Advanced.” Shortess’s father, Steve Shortess, started the company in 1979 as a component producer for the oil and gas industry—out of his garage with only a truck and $5,000 worth of inventory. He chose the name Advanced for one specific reason: it would be listed before his competition in the phone book’s “Yellow Pages.” Through its 40 years of success, though, the name “Advanced” really became a philosophy and objective, woven into every strand of the company’s DNA.
For example, Advanced has always fought to keep pace with rapidly evolving manufacturing technology, and the result is a company that exploded from a small raw material supplier to a Tier 1 supply chain partner for OEMs in aerospace, defense, energy, and oil and gas. “My father loved new technologies. He was always that first person to have a car phone, a radar detector, or a portable computer,” said Shortess. “He was constantly on the lookout for emerging technology.”
Originally published on SME.org and written by Advanced Machining & Fabricating
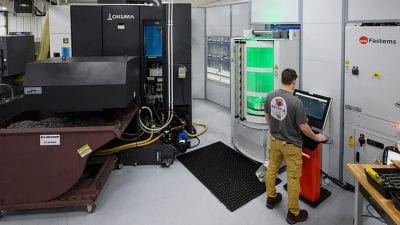
Advanced uses a Fastems ROBOOne Flexible Manufacturing System (FMS). The new system’s largest benefits happen on the front end of the process through the MMS controller’s functionalities for scheduling, forecasting, data collection, and document control.
This dedication to progress, coupled with the booms in the aerospace and oil and gas industries, turned Advanced into a powerhouse of the southwest. Advanced’s customers began to increasingly request complex components rather than simple ones. Soon, the small garage shop needed and purchased more sophisticated machines to operate next to its manual equipment. Shortess hired additional people to keep up with customer demand. Today, Advanced employs 35, even after a reconfiguration during the coronavirus pandemic that called for a slight decrease in workforce.
The pride of Advanced’s shop is currently its five-axis machining section, and its beacon is a Fastems flexible manufacturing system (FMS) featuring 36 pallets connected to two Okuma MU 5000s. In that area are also three stand-alone Okuma M460-5AX machines. The entire area is dedicated to five-axis hard metal machining, primarily of aerospace parts. Most days, the section is running aerospace grade titanium such as 6AL4V to create parts such as nacelle and thrust reverser components.
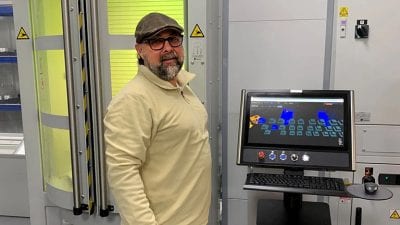
Scott Shortess, CEO of Advanced Machining & Fabricating and Advanced Plastics.
Shortess is firm in his dedication to efficiency and shares his father’s appreciation for advanced technology. That’s why he made the decision to rely more on automation. In the last decade, he and his team started measuring spindle utilization. “We started with a very rudimentary methodology of measuring,” he explained. “Someone would take a picture on a smartphone of the diagnostics from each piece of equipment, and then they would go back to their desk to calculate time and productivity from those graphs.” The shop team analyzed how long each machine was in cycle and how long each sat unused. “We started seeing these numbers, and we realized how underused our spindles were.” So Shortess reached out to Risto Niemi, business area director at Fastems, the developer of automation solutions.
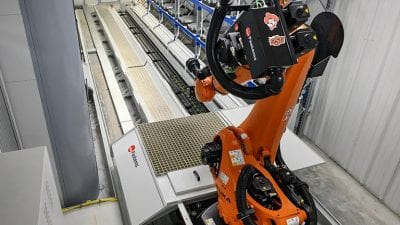
Advanced’s 36 pallet system is connected to two Okuma MU 5000s and run by Fastems ROBO-One Flexible Manufacturing System (FMS).
Niemi visited Advanced to introduce solutions for manufacturing management software (MMS), automation systems, lifecycle services, and digital manufacturing. “He really expanded our minds to all of the possibilities in automation,” said Shortess. “We’ve spent tens of thousands of dollars traveling, going to trade shows, looking at new technologies, and we never scored a home run until that meeting, along with the ongoing support and knowledge that he and the Fastems team provide.”
Advanced had the Fastems RoboFMS ONE (FMS – Flexible Manufacturing System) installed in June 2019. The RoboFMS ONE, which comes with MMS to handle production scheduling and execution, automates the five-axis Okuma machines and has slashed setup time. Shortess said that the RoboFMS ONE and MMS have had “enormous impact on efficiencies such as first-pass yield, spindle utilization and increased capacity, while increasing the company’s reputation for producing quality products and service.”
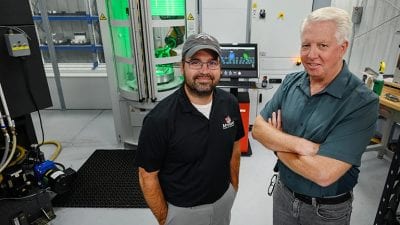
Jason Adkins, Director of Operations & Kim Parrish, President at Advanced.
“We build to demand as opposed to building to inventory. We can upload the ERP data and let it schedule everything, and it’ll tell us what resources are required.”
He explained that the predictive MMS and pallet automation system is the most efficient solution for a company like Advanced, because it is a high-mix, low-volume shop. Advanced customers need one to five parts at a time, not thousands. “The flexibility of the system is one of its best attributes for us, because we’re a contract manufacturer. We build to demand as opposed to building to inventory. We can upload the ERP data and let it schedule everything, and it’ll tell us what resources are required,” said Shortess.
In a shop with many changeovers, the easiest way to save time and money is to reduce setup time. Shortess recalled a complex titanium aerospace hinge assembly part that used to be run on traditional stand-alone machines. This particular part took two hours in setup time alone, even more than the part’s one hour and 40-minute cycle time. “We basically put it back through new product development with our new system, and our setup time went from that two hours to really nothing—zero—because it is always in the Fastems system,” Shortess said. “We gained that changeover time, and that helps increase spindle utilization.” Advanced is currently running semi lights-out, and complete lights-out manufacturing is the ultimate goal.
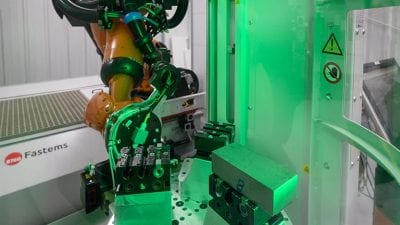
Advanced reduced the load-to-load changeover time required to begin machining a titanium aerospace bracket through standardized workholding solutions and immediately saw an increase in spindle utilization after trusting it to Fastems automation.
“We can’t crunch the amount of data that the MMS can crunch. The system looks at tool data, cycle time, everything to predict what it needs. Now we’re talking about stable, predictable processes. If people are not investing in this type of technology in manufacturing, they are just falling further and further behind, in my opinion.”
The new system helps develop processes on the front end before jobs are even started. Advanced uses it to track tool wear and to take advantage of all that can be recorded. “We’re running it in automatic mode, not manual. We’re letting it do what we paid for it to do,” explained Shortess. “We can’t crunch the amount of data that the MMS can crunch. The system looks at tool data, cycle time, everything to predict what it needs. Now we’re talking about stable, predictable processes. If people are not investing in this type of technology in manufacturing, they are just falling further and further behind, in my opinion.”
Advanced plans to expand into another facility in the next few years. This new facility will have an additional Fastems FMS with even more processes such as Fastems Gantry Tool Storage (GTS), robotic deburring, and advanced metrology. The GTS system uses traveling gantry robots to store and deliver up to 4,000 cutting tools to and from individual machines, minimizing the need for an operator during setup. “I don’t think we could get to world-class spindle utilization numbers without a GTS. That’s the core of it. You marry an FMS system with a GTS system, and you can really crank out some parts,” said Shortess. “With our new automation technology and direction at Advanced, we are definitely living up to our name.”
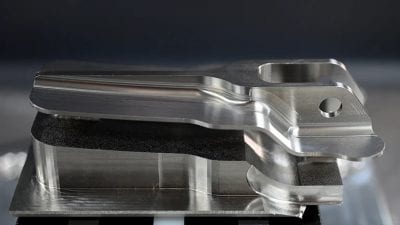
The bracket took two hours in machine and workholding setup time alone before the FMS was installed at Advanced. Today, that time has been reduced to almost zero.
Originally published on SME.org and written by Advanced Machining & Fabricating
Executive Summary
-
Case: Advanced Machining & Fabricating: A company that exploded from a small raw material supplier to a Tier 1 supply chain partner for OEMs in aerospace, defense, energy, and oil and gas.
-
Problem: Advanced’s customers began to increasingly request complex components rather than simple ones. Soon, the small garage shop needed and purchased more sophisticated machines to operate next to its manual equipment. Shortess hired additional people to keep up with customer demand.
-
Solution: The pride of Advanced’s shop is currently its five-axis machining section, and its beacon is a Fastems flexible manufacturing system RoboFMS ONE featuring 36 pallets connected to two Okuma MU 5000s. The RoboFMS ONE, which comes with MMS to handle production scheduling and execution, automates the five-axis Okuma machines and has slashed setup time.
-
Outcome: An enormous impact on efficiencies such as first-pass yield, spindle utilization and increased capacity, while increasing the company’s reputation for producing quality products and service.
-
Plans for the future: Advanced plans to expand into another facility in the next few years. This new facility will have an additional Fastems FMS with even more processes such as Fastems Gantry Tool Storage (GTS), robotic deburring, and advanced metrology.