Two weeks ago I started this blog series by introducing ways to achieve economically feasible production of small batches with smart fixturing solutions.
Before machining, the workpiece needs to be fixed to the machine table and we went trough some ideas on how to make it efficiently.
In this post I focus on another possible development area: robot handling and more specifically, gripping different kind of workpieces. To automate the workpiece exchange, it needs to be gripped with a robot. Unfortunately, the gripper of an industrial robot is not as flexible as the hand of a human, which quite often means that several grippers are needed to make the robot able to grip all the manufactured parts.
Luckily, unlike us humans, the robot can easily be equipped with changeable gripper.
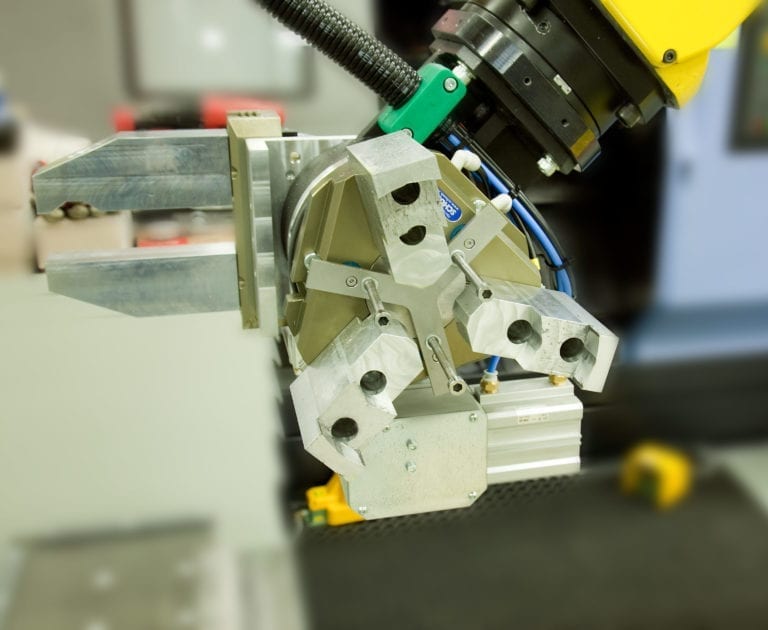
Minimize the number of grippers
To keep the number of different grippers and thus costs in a reasonable level, the manufactured workpieces should share some common features. The feature can be a specially designed “automation interface”, i.e. a hole pattern of that is the same in all variants, or some geometrical similarity. For instance, cubic workpieces of rather large size variety can be gripped by using a long stroke gripper, either a conventional or pneumatic one, or a servo driven design. Despite the higher price, servo-based design allows some additional functions, such as part width measuring and more accurate gripping force control, and is therefore recommended in many cases.
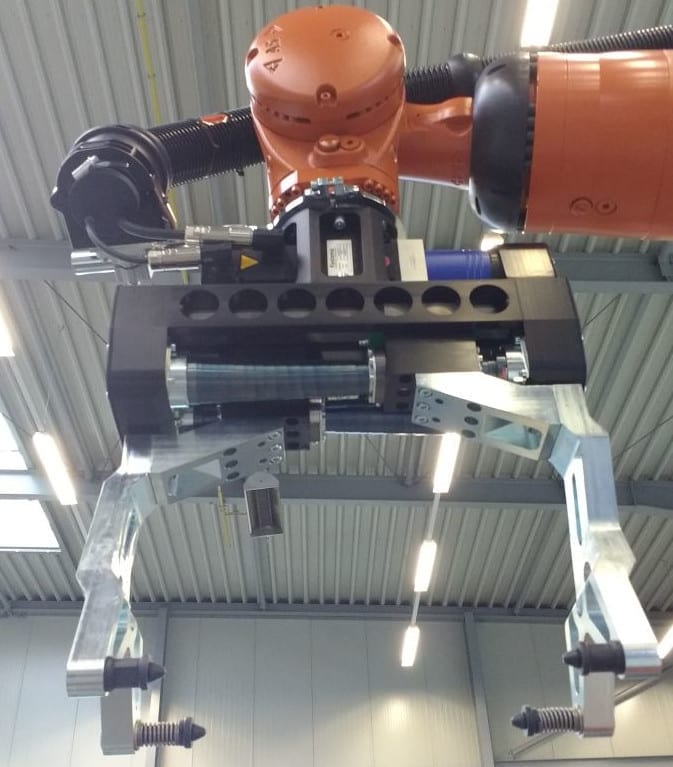
Gripping a round workpiece is still challenging
Unfortunately, for round workpieces the available options of “universal grippers” are very limited. Apparently, this application area is still waiting for the players on the field to introduce new gripping products. Luckily this is limiting mainly the handling of thin, flange-like products. Longer, axial type of products can typically be handled with the similar long stroke grippers as prismatic parts.
In the next post we will move from the very physical challenges to the software side – more specifically, to time consuming and quality-wise critical NC programming and resource management.