Are you producing in large batches to optimize unit cost?
Batch driven production means producing larger batches of parts than the current order backlog consists of. The idea is that the larger the produced batch, the lower the cost per piece. In industries where orders are often recurring, batch production is natural and in its own way, a cost-efficient choice. The main reason to produce in batches is the high production start cost per part. This consists of production planning, start setup, and test drives to get the part and the quality right. These costs recur every time a new batch is started, regardless of whether the same part has been produced before or not. Larger batches mean less production starts and less production start costs per part.
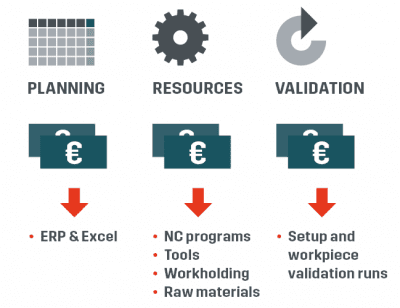
Besides the actual raw material, production start setup typically has the biggest influence on unit cost.
That said, producing larger batches to lower the production start cost and optimize cost per unit means having to accept the negative consequences:
- Higher work-in-process (WIP)
- Longer lead times
- Slower earnings when part of the batch is going to inventory
From batch production to order-driven production
Today’s automation technologies offer a variety of possibilities to optimize production. This makes manufacturing economical for batches of all sizes, meaning that the unit cost of producing a single piece is the same as when producing a batch of 100. Not only is the unit cost lower with order-driven manufacturing, it also frees capital from WIP and inventory, and allows just-in-time deliveries with shorter lead times and high quality.
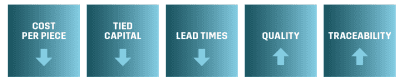
Today’s automation technologies enable flexible and cost-efficient production, even for batches of one.
Six solutions blocks for order-driven production
There are two steps to achieve order-driven and economical production: (1) optimization of the six key production bottlenecks, and (2) making the production process reproducible. This requires looking at the entire production and identifying the exact process phases that could be further optimized. After that, the data and integration between all people, machines, data systems and resources is inspected and turned into one efficient and flowing process.
Production processes vary depending on what kind of a part or product is being manufactured. The process can have a couple to hundreds of different phases which all take different skills, times and resources. Typically, single phases are optimized but process-wide optimization is lacking. Let’s take a look at an example shop floor. The production bottlenecks are different in every case – typically some are in good condition while others need optimization. Here are the six typical bottlenecks we find manufacturers to often have:
- Production planning (ERP + Excel)
- Production start setup (resources and validation runs)
- Tool management (low machine tool utilization due to machine dedication and tool waiting time, quality issues and spindle crashes due to setup errors, continuous tool setup work)
- Transfers and loading between production process phases
- Quality and tracing (how to ensure efficiency?)
- Machine tools (resourcing, machine dedication, operator skill sets and substituting challenges)
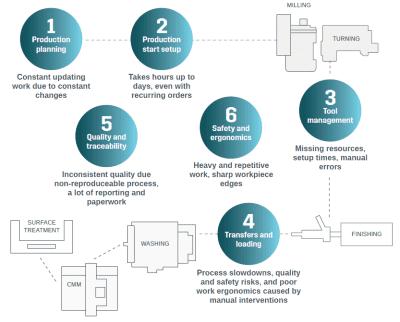
There are six typical challenges on a shop floor. Tackling these means achieving economical small-batch production.
Want to know more? Watch our webinar recording for “Six Solution Blocks for Economical Small Batch Production”!
When these six are in shape, one can truly master order-driven production and manufacture economically. If you’re interested in learning more on how to practically tackle these bottlenecks, I hosted a webinar + Q&A on this topic. Here we will discuss this topic more in detail – a warm welcome!