What if the unit cost would be 1:1 no matter
if you produce a single part or 100 of them?
Do you want to improve the return of your CNC investment? Great – this blog series is for you! During the past 40 years we have witnessed thousands of successful CNC investments – and many that could have paid off much faster. In this post we focus on batch production and how to optimize the unit cost without needing to produce more than ordered.
Talk with Fastems automation specialistDownload the ultimate high-mix-low-volume automation guide
Large batches = lower unit cost but also slower turnaround
The unit cost of a produced part depends on how much production time and resources you need for it: labor time, CNC time, raw materials, tools, fixtures, etc. A significant portion of these costs occur when you prepare a job for machining (incl. NC programming, raw material & tool preparation, fixture building, test runs) and plan your production: what to produce and when? Between the machining OPs you have re-clamps, and after machining you might need to finish, measure, mark, hone, assemble – or otherwise process your part further. The more effort you need to put in, in order to get everything done, the higher the unit cost.
Furthermore, if your process is not repeatable (=it can’t be simply re-produced) your unit costs remain high even if the same job(s) repeat. Does this sound familiar? You need to:
- prepare every order from the scratch even with recurring jobs,
- make test runs before the actual machining to ensure precision,
- have relatively high WIP, and
- avoid making too quick or precise delivery time promises because the process time varies so much.
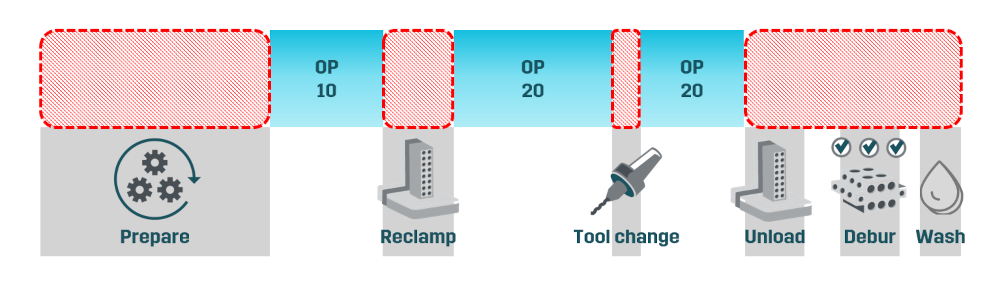
Here is an example machining process that includes lot of time consuming and manual work – generating more costs per part. If all your production runs – even recurring jobs – look like this, how efficiently can you utilize your machining capacity? Can you estimate your delivery times? Do you have labor challenges? How much WIP do you have?
To push the unit cost down, most of CNC manufacturers choose to produce larger batches than the customer orders require, and stock the extra for the possible future orders. Producing larger batches does help you in pushing the unit cost down but it also means slower turnaround. This basically means you’re compromising the following in order to keep your unit costs down:
- longer lead times for every order, also the urgent ones,
- higher WIP because different machining process phases require different times and batches are piling up between those phases to wait, and
- slower earnings because there is extra capital tied in inventory that realizes as a turnover with a delay.
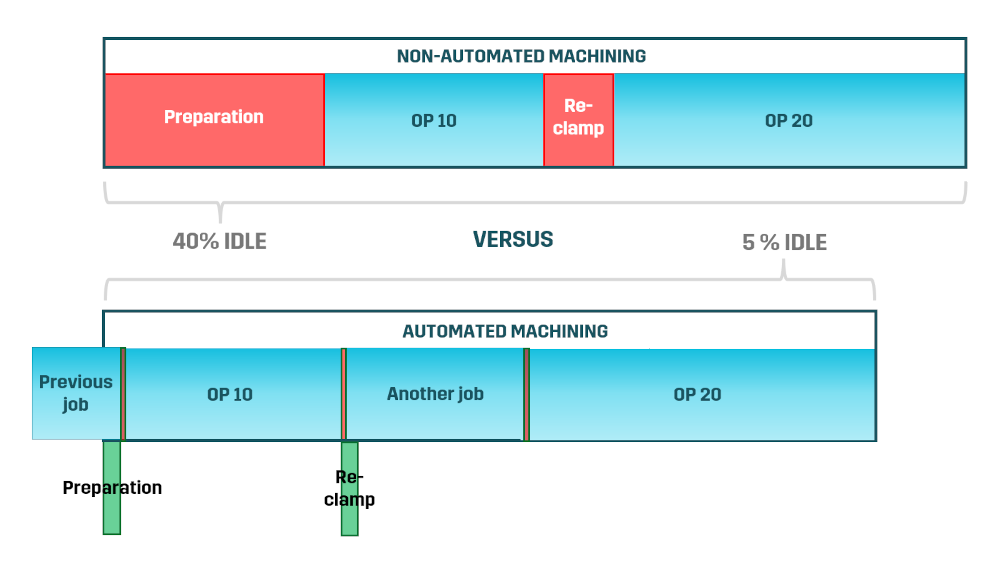
There are two main factors you need to focus when wanting to produce small batches economically. First, make sure your machines run other jobs meanwhile you prepare, re-clamp or otherwise manually process your parts. Second, you need to minimize the manual effort needed for each order. Here is a comparison of (1) a non-automated process that requires machine tool to stop for job preparations and re-clamps and (2) reproducible, automated process where a single machine can run any job and the effort needed for setups and re-clamps is minimized.
How to produce small batches with low unit cost?
Profitable and flexible production is essential in high mix, low volume manufacturing and it requires that production jobs are easily reproducible – this is where automation can help. The flexibility of the automation is what enables the cost benefits for the production at large. Here’s the ‘recipe’ of how flexible automation enables profitable and flexible high-mix-low-volume production:
1. Production scheduling based on orders and available resources
Flexible automation has visibility over your order backlog and your production resources: machine tools, raw materials, NC programs, tools, fixtures, pallets and auxiliary devices. Since it has all the needed data for producing any of your parts, it can schedule your production to run just the right orders at the right time – all the time.
2. Job & production resource sharing
“Flexible” means that the automation shares your production jobs between your CNC machines. This means, any of the capable CNC machines could run the job, depending on which one has the capacity at that moment. Because flexible automation integrates all your machines, devices and resources into one system, it can easily share everything between the CNC machines. This also makes your production resilient: if your machine breaks or an urgent customer order arrives, the system can adapt in real-time by reallocating the jobs to the available machines.
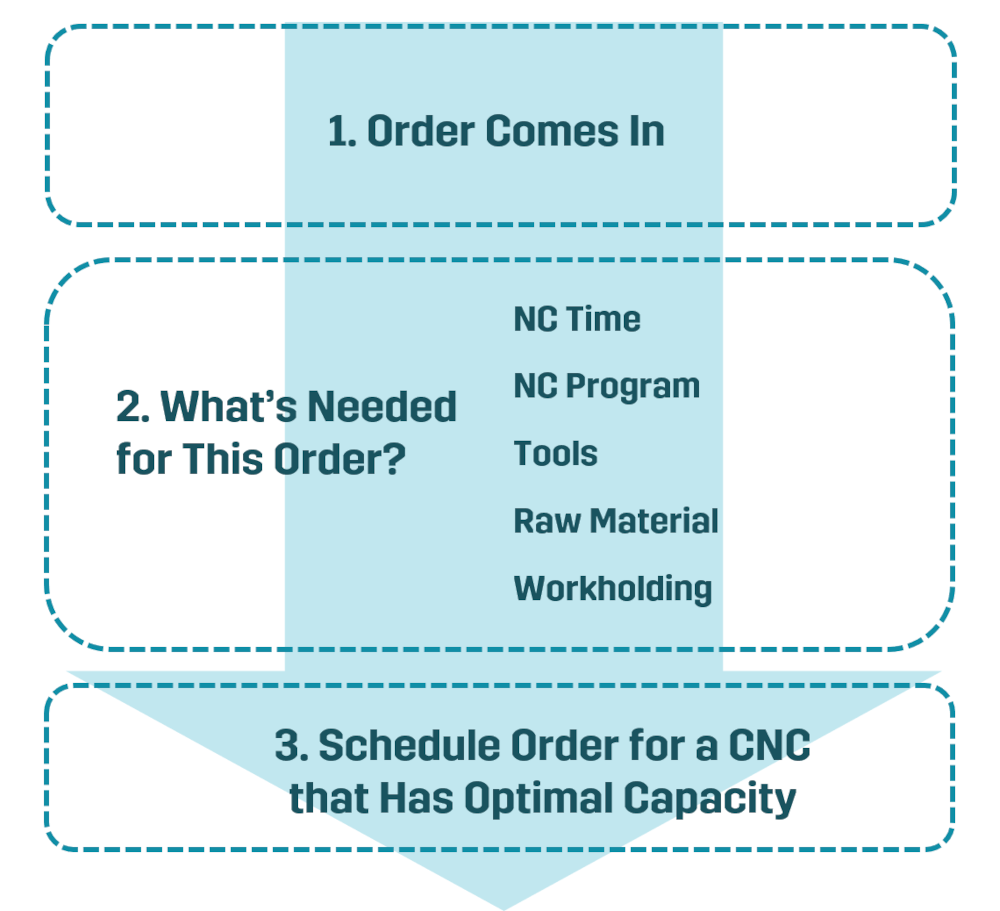
Flexible automation has visibility over the order backlog and production resources. After receiving information on what needs to be produced by when, the automation system checks the production resources and schedules the production job.
3. High unmanned production capacity
Did you know that the nights and weekends alone make about half of the 8,760 hours in a year? Flexible automation has a pallet or part storage large enough to keep your machine tools fed also during the lights-out periods (= when your operators are not working). You dedicate each of your pallets and fixtures to specific jobs and load enough of them into the storage in advance during your manned shift. When your operators enter the shop floor again, they can simply unload ready parts from the system – this means any parts in your portfolio, depending on your production orders.
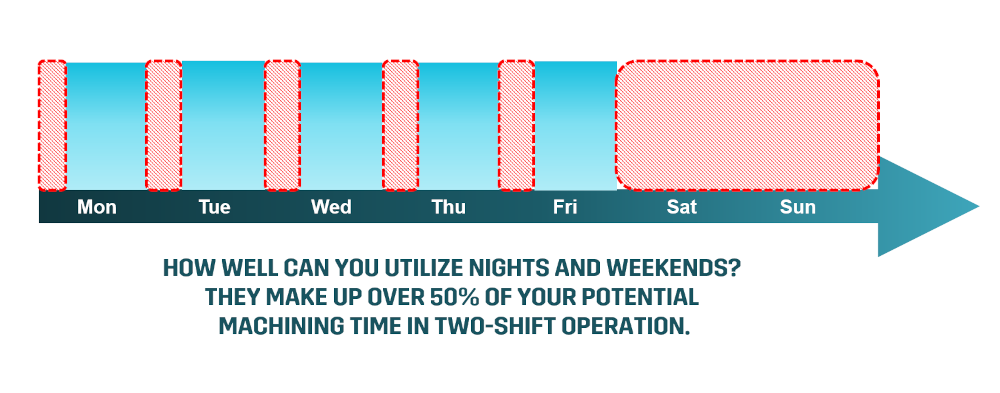
Even if you utilized your machine tools well during manned shifts, you would be losing over a half of your capacity without unmanned production capacity for your unmanned periods. Flexible automation stores enough pallets or parts for your production to run unmanned during nights and weekends.
4. Minimum preparations needed for recurring orders
Because the automation system has everything needed to produce any of your jobs, it can re-run any job without need to build fixtures, make test runs or fine-tune the NC programs. Your automation simply checks which NC program is needed for an order, which tools and fixtures does that order use, which machine has capacity for the job, and does the system have the needed pallets and tools. If something was to be missing, the automation system would inform your operator IN ADVANCE. Once you have a job in flexible automation, it is permanently there and always ready to be re-run.
5. Integrate other process phases than just machining
Machining is only one part of the production process. Every transfer you need to make between your machines and devices takes time and thus generates costs. The less manual intervention your process requires, the more reproducible and predictable your production is. Flexible automation can integrate with various robotic applications such as finishing, deburring, measuring, marking, pallet loading or even automated turning machine tending where you handle work pieces directly instead of pallets. Flexible automation works together with AGVs or AMRs that might be transferring your tools and raw materials; as well as with CMMs, washing machines, tool presetters, and any other device you might have on your shop floor. Flexible automation integrates with your ERP, tool manager, CAD & CAM, PDM, MES, fleet managers, you name your data systems. Fastems’ over 5,000 global installations include over a hundred different machine tool, device and software brands, and as an open integrator we make sure your machines, data systems and people can work as one.
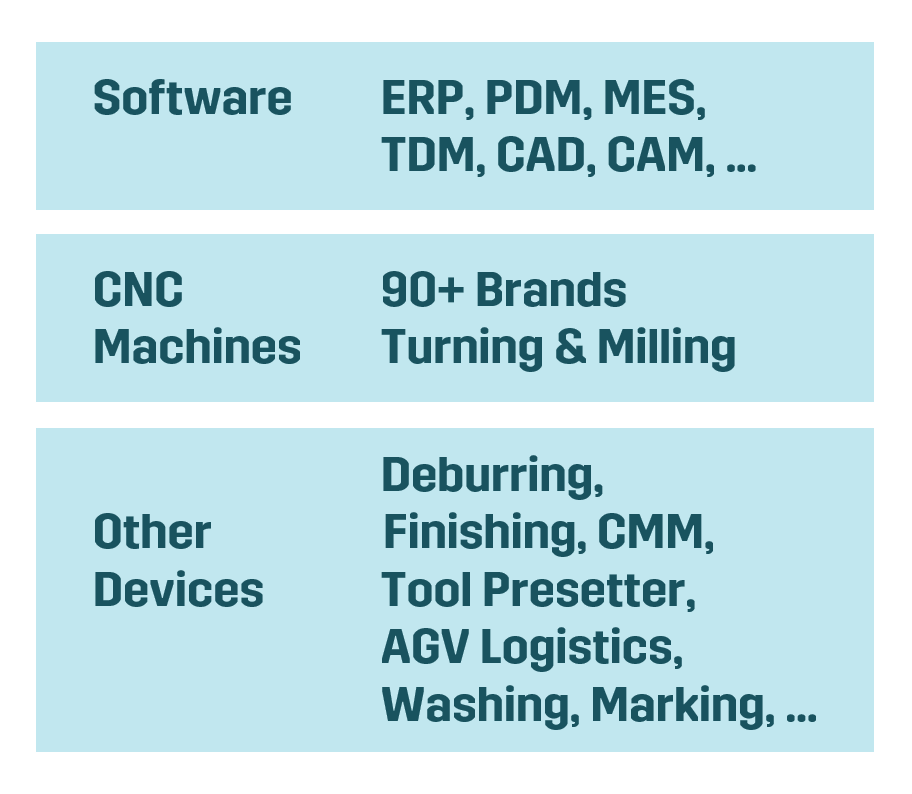
Machining is only part of the manufacturing process. The more integrated your process, the less manual intervention and lower unit cost. Flexible automation integrates with hundreds of machine tool, device and software brands.
It is all about your machining process. How to make sure everything is done efficiently and timely for every job – and how to push the unit cost to the minimum when you run short series and high mix? When done in steps, you can fine-tune your manufacturing processes to perfection without needing to turn everything upside down at once. After going through this process with thousands of manufacturers with one to tens of CNC machines, we are here to help you. Are you ready to make more money with your CNCs?
Talk with Fastems automation specialistDownload the ultimate high-mix-low-volume automation guide
In case you want to read more on how to make the most out of CNC investment, read the other blogs in this series:
Make More Money with Your CNCs – Minimize Machine Idle Times
Make More Money with Your CNCs – Get Rid of ‘1-man-1-machine’ Production Philosophy