Increasing spindle utilization and lights-out manufacturing; minimizing lead times and scrap; offering safe, ergonomic and interesting jobs…everyone has a reason to automate. The real question is: how to automate? Here is our practical checklist for automating milling machining centers, based on over 5,000 automation projects for over 90 machine tool brands.
1. How to Ensure Your Machine Tool Can Be Automated?
The first step is to ensure your machining center has a suitable design and configuration for automation. As long as the following conditions are met, you technically can – and from the economical point should – automate your machine tool.
- Production mix defines machine tool size. Any size of a machine tool can be automated, that is not an issue. But to ensure yourself a system that pays off in a long run, take a step back and think about your manufacturing mix. Considering that an automated machine tool spindle can run up to 90% of time, you want to have jobs for it not only today but also in five, ten or 15 years. Map the size of a machine tool envelope that would fit a large share of your manufacturing mix – and select your machine tool size based on that.
- Capacity & durability. Since automation typically multiplies the machine tool spindle time, the machine tool itself needs to be designed for high usage. The modern 4 and 5 axis machining centers have high spindle speed and high thermal stability – and compared to cheaper models, their lifetime when automated is averagely five times longer. Since a CNC automation system can last for decades, it doesn’t make sense to invest in such system with machine tools that need a replacement after a year or so.
- High precision level. The idea of automation is to enable repeatable quality – and that cannot happen if the machine tool itself is not able to keep or repeat the tolerance.
- Automation access. The milling machine tool needs to have either an automatic pallet changer or an interchangeable table (i.e. zero-point technology) so that it can be automated. Machining centers with a fixed table can be theoretically adjusted for automation by retrofitting a zero-point technology but it is always a case-by-case project with the machine tool builder and sometimes does not make sense from the economical point of view.
- Tool capacity. To highly utilize spindle capacity, cutting tools cannot form a bottleneck. Therefore the machining center also needs to have a large enough tool magazine for rapid tool changes and long enough unmanned machining periods. Based on our experience, the recommended minimum magazine size for an automated machining center is 80 tools. Tool capacity can be also extended with tool automation solutions which reduces need for large machine tool magazines.
2. How to Match Automation with Your Production Mix?
The second and most important factor for a successful automation project are your actual manufacturing needs – the production mix, volume, lead times, manufacturing phases, etc.
- Part numbers and amount of operations. If you belong to majority of manufacturers that run multiple – or even hundreds – of different parts, you are likely to benefit the most of a flexible automation that enables you to run high mix and low volumes just as efficiently as you would run large series. And even when your part mix is not high but each of your parts require many machining operations – you benefit of flexible automation. If you run only a couple of different parts with a few operations each, a more traditional manufacturing line is what you should go with.
- Changing demand. How far to the future can you to predict your manufacturing needs? If the visibility is anything less than five years (in our customer base it is often less than two weeks), we highly recommend to go for flexible automation that adapts to changes fast, including new workpiece manufacturing.
3. How to Prepare Your Facility for Automation?
The third important factor for automation is the actual production facility. The physical dimensions, layout and surrounding processes all play a large role when selecting and configuring machining automation.
- Production hall. Especially in existing production halls, the space impacts largely to the automation type and system configuration. If you space is narrow, can you utilize your space vertically? Or if your space is both narrow and has low ceiling, how can your system be configured to maximize lights-out manufacturing capacity? Gladly there are solutions for every need, and you should take advantage of the automation partners design team to utilize your space to the maximum.
- Production flow. Consider the day-to-day production flow: how are the raw materials brought into your automation system, and to where will the machined parts move next. Automation is a tool for your team to work more efficiently, safely and ergonomically – therefore you need to ensure the work around it is as effortless as possible. Remember that it is also possible to optimize the flow and utilize space even better by integrating material logistics or other work phases into your automated system.
- Future extendibility. Based on our experience, 80% of automation systems are extended within a few years after installation because of their positive business impact. If possible, take this scenario into consideration when planning your machine and automation investment in the first place – you don’t want the space being a limiting factor for your growth.
Learn to Automate Milling CNCs in AMB and IMTS 2024!
Joining in AMB in Stuttgart or IMTS in Chicago in September? Join our “How-To-Automate Tuesday” 10 September or reserve your own demo to learn more about this topic and see how flexible automation works in practice!
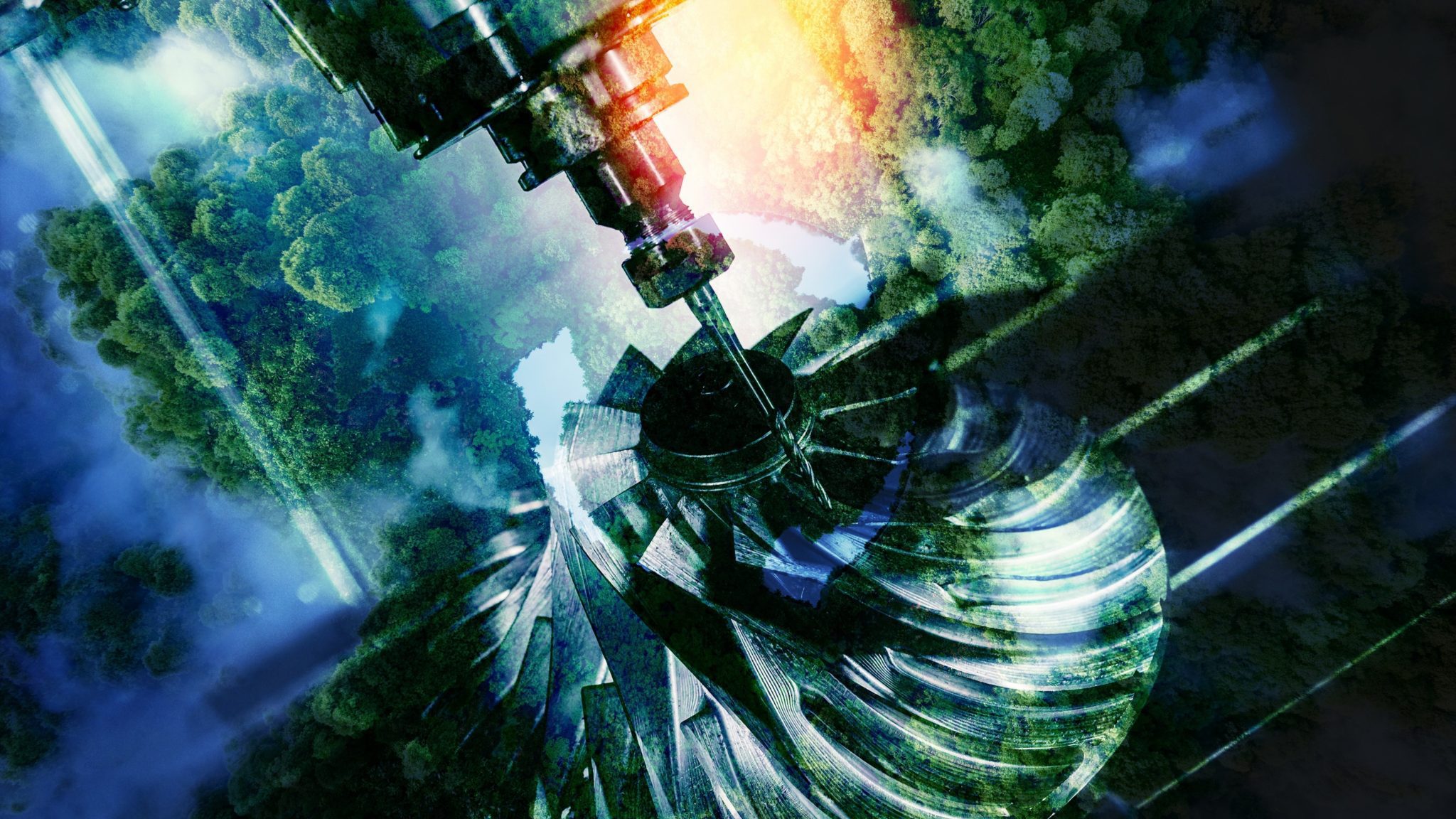
10 SEPTEMBER 2024
IMTS: How-To-Automate Tuesday
Our IMTS showcase includes practical tips, learning sessions and demonstrations on how to automate milling machining centers. Join the common sessions or reserve your own demo!
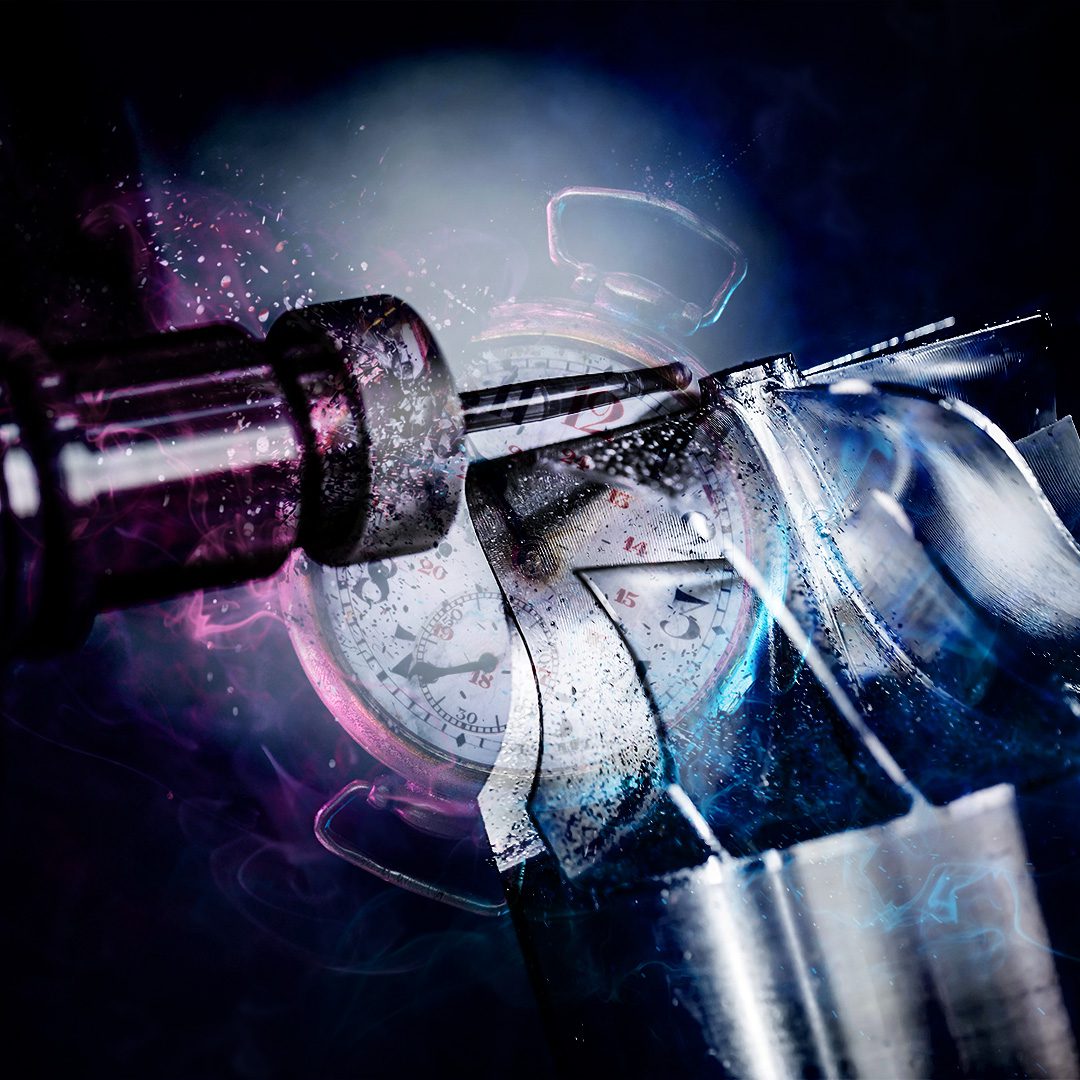
10 SEPTEMBER 2024
AMB: How-To-Automate Tuesday
In AMB we are advising and demonstrating how to automate milling machining centers. Join the sessions in the booth program or book your own demo!