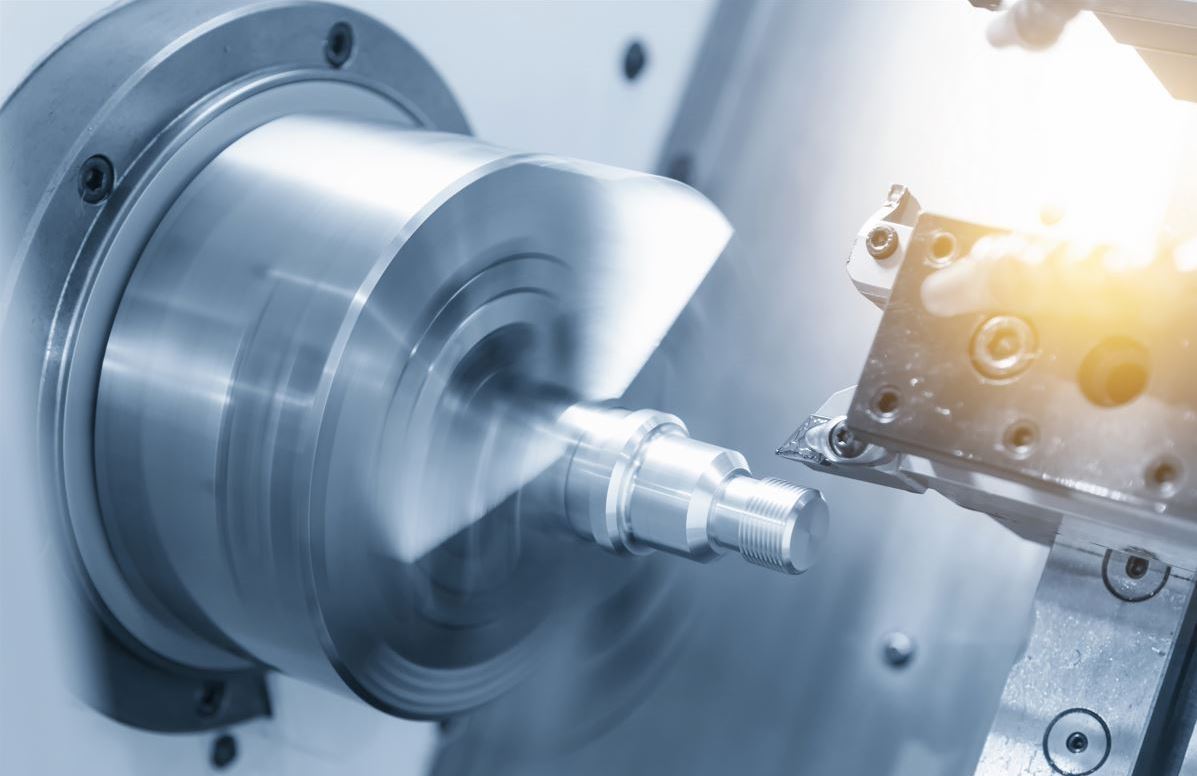
The Benefits of CNC Automation
Automation Builds Successful Manufacturing Businesses
This page discusses the benefits of CNC automation grouped to operational, financial, and business benefits. They all work together to build successful, competitive and sustainable manufacturing. Here’s how that happens:
- Automation has a tremendous impact on operations, drastically improving many manufacturing KPIs (key-performance-indicators)
- Operational development leads to better financial results like revenues, profits, and return-on-equity.
- All this adds up to higher customer satisfaction, stronger employee engagement and makes manufacturing more sustainable.
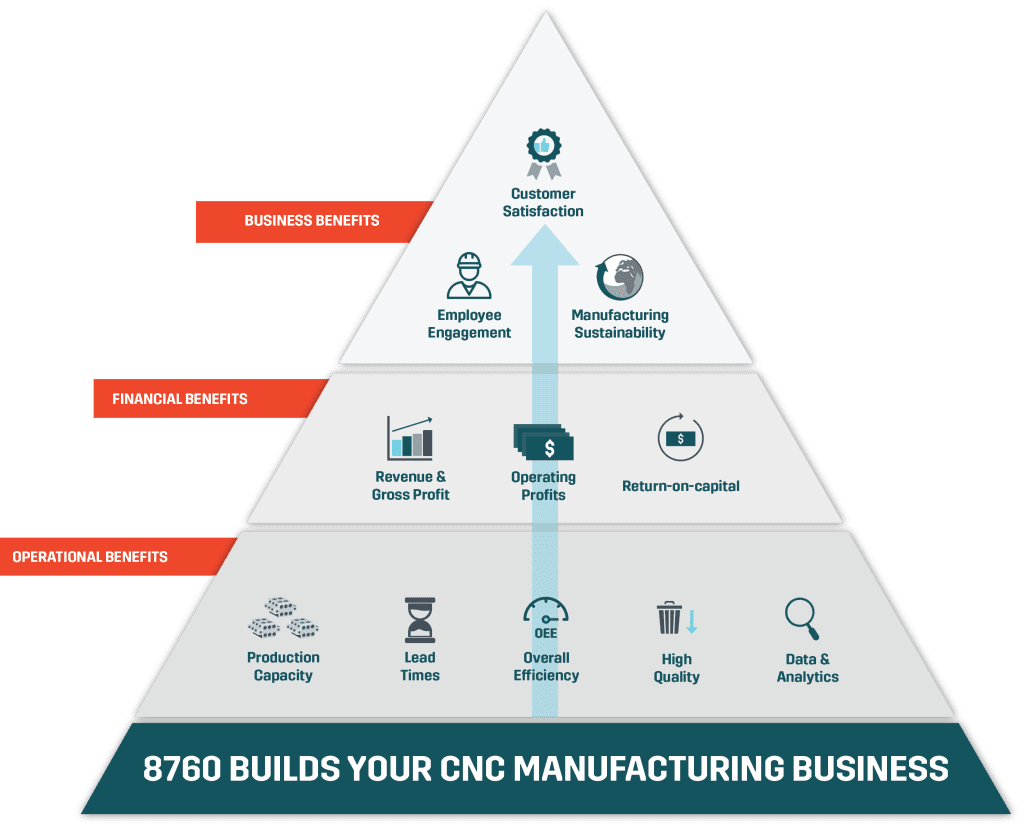
The Benefits of CNC Automation
To summarize, the benefits of CNC automation include:
- Bigger volumes
- Faster and more reliable lead times
- Higher overall efficiency (OEE)
- High and stable quality
- Availability of data and analytics
- Higher revenue and gross profit
- Stronger operating profit (EBIT)
- Higher return-on-capital (smaller inventories)
- Higher customer satisfaction
- Stronger employee engagement
- Manufacturing sustainability
The illustration explains how the benefits come together and have a compounding effect to the success of a manufacturing business. Wonder about the number 8760? The vision behind Fastems’ automation solutions is to have the production only do the right things, at the right time – all the time. The ultimate goal for people and businesses is to make the most out of the time we’ve got. In numbers, that’s exactly 8760 hours each year.
Explaining the Automation Benefits
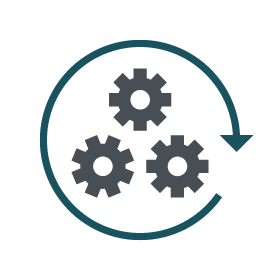
Operational Benefits
The positive effect of automation is based on its tremendous capacity to improve shopfloor operations, visible in almost every possible production KPI (key performance indicator) there is. Below you can find the five essential ones.
Better overall efficiency thanks to less human intervention
When one considers nights, weekends, holidays and all of the ‘normal’ inefficiencies during the usual 1-2 working shifts, the average non-automated CNC machine cuts chip at around 2000 hours in a year – or even with way less. This is only 25-30% of what is realistically achievable with a flexible automation system. In other words, the utilization of the average CNC machine could triple if was automated.
The main reason for low utilization lies in set-ups happening in between of batches and the inaccessibility of the odd-production hours. Automation solves both challenges. In pallet handling automation systems set-ups can be prepared while another pallet is being machined eliminated set-up times almost completely. In robotic automation the part loading sequence is fully standardized and quick – even in high-mix context. Here, possible gripper changes related to handling of different parts can also be automated. With small buffer, automation can run over a night, or a weekend unmanned. Outcome: machine tools can achieve utilization of 6000 or even above 8000 hours vs the yearly 8760 hours.
Higher production capacity
Increasing capacity can be daunting due to floorspace and workforce challenges. Automation can help with both, meaning the business is able to operate twice the size of manufacturing operations from the same shop and with same people. Increased capacity is simply the outcome of higher CNC machine utilization which typically increases 2-3 times when automation is introduced.
High quality means less scrap
In order to automate a process, it needs to be reproducible. With such processes design, automation can run continuously and practically error-free – unlike humans. This means less negative surprises, scrap and higher customer satisfaction. With high-cost part, removing the opportunity for human error in part handling also reduces business risks.
Faster and more reliable lead times
Stable processes combined with good production planning features mean faster lead times – and makes keeping promises much easier. Intelligent automation simulates whether one has the capacity to produce a batch in time tomorrow and furthermore, automatically re-optimizes after sudden changes like machine errors or missing tools. All this means that lead times get faster and there is less unused – wasted – manufacturing potential. The outcome is higher customer satisfaction and stronger profits.
Data and analytics enable process development
Production development can’t happen without data and analytics: one needs to know the current situation and quantify the bottlenecks and targets. Production data collection can also fulfil traceability requirements in aerospace industry for example.
Intelligent automation can track production key performance indicators and give insights for everyone working in production on how to improve. In practice this can mean monitoring the OEE, machine tool utilization and available resources, or improving production with practical tips and hints.
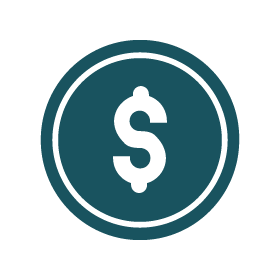
Financial Benefits
Automation improves manufacturing operations which leads to financial results – measured in revenues, profits and return-on capital.
More capacity means higher revenues.
Automation increases the output of a CNC machine significantly. If the machine tool utilization is tripled – from 2000 to 6000 hours in a year – the output similarly triples. Automated production also uses less floorspace meaning that facilities have less limitations on your capacity. Finally, high and stable quality means fewer negative surprises on production volumes in form of scrap.
Lower cost-per-piece: labor
Labor cost per part decreases as CNC machine utilization increases and one operator can support many automated machines. Intelligent automation also requires less manual intervention in production planning and managing NC programs or tools, also reducing the labor component of cost-per-piece.
Lower cost-per-piece: Equipment and floorspace
Higher utilization of manufacturing equipment means that their cost (depreciation) is divided to a larger production volume decreasing cost-per-piece. As CNC machines are usually the most expensive equipment of the shop, tripling their utilization means that the cost-per-piece is cut to a fraction! The scaling can consider measuring, washing, marking machines or tool-presetters, if they’re part of the automated production. The reduced floorspace use also reduces the utilities-component of cost-per-piece.
Less working capital
Intelligent automation reduces unnecessary production buffers as one can keep machine tool utilization high despite producing small and varying batches. Example: If a subcontractor gets and order for 5 pieces it doesn’t have to make 20 to justify the set-up changes. OEM manufacturers can also let their production plan ‘pull’ just the required amount of the right workpieces at the right time. Furthermore, better process reliability also means less ‘safety stock’ needs. Work-in-progress parts can become obsolete and need to be scrapped. Automation means, then, less money tied in inventories and work-in-progress – and potentially less inventory losses.
Stronger operating profit
Thanks to bigger production volumes and lower direct cost-per-piece, the manufacturer can run at higher operating margin – that is, it makes more money. Automation scales fixed expenses like buildings, IT staff and intangible costs, too, as they don’t grow along with the production volumes that make up the revenues. This means automation helps you running a bigger business.
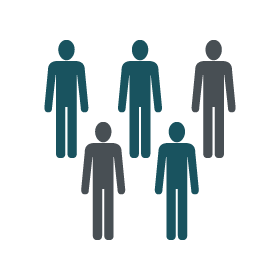
Business Benefits
In addition to financial results, long term business success is built on customer satisfaction, employee engagement and sustainability. Again, automation supports them all.
Customer satisfaction
In contract manufacturing stable quality, reliable and fast deliveries and cost competitiveness are fundamental drivers of customer satisfaction – all supported by automation. In OEM manufacturing the primary customer is internal but reasons of satisfaction are similar. Cost competitiveness, stable quality, and the ability to produce the right parts in right amounts is essential to business success of an OEM manufacturer. Eventually these developments support the satisfaction of end customers as well, in form of high-value products.
Employee engagement
Finding and keeping skilled employees in manufacturing jobs isn’t easy today. By making jobs safer and more meaningful, automation helps keeping your people motivated and in good health. Since intelligent automation offers in-advance view on the upcoming jobs and resource needs, people can easily plan their own work ahead, which typically increases job satisfaction and decreases stress. Furthermore, working with automation, for most people in manufacturing, is inherently meaningful as it supports the motivation for continuous learning and improvements. Increasing efficiency and decreasing the amount of waste also fit the worldview of the most.
Manufacturing Sustainability
As automation multiplies the utilization rate of machine tools, it enables manufacturers to reduce the CO2 emissions related to their production development investments. This happens by reducing the amount of machine tools necessary to reach a certain production capacity. With a typical flexible manufacturing system (FMS) with two integrated machine tools running on utilization rates of 60 % each, the system can replace six stand-alone machine tools that can’t yield more than about 20 % of utilization. Furthermore, automation reduces production floorspace creating savings in utility costs. Read more about CNC automation and sustainability.
Read More About the Companies Who Have Benefited from CNC Automation:
Or rather talk or mail directly with us?
Give us a call or send an email
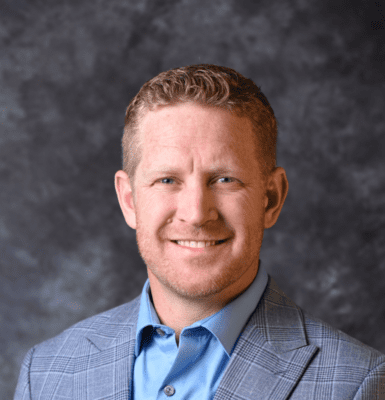
Contact us
"*" indicates required fields